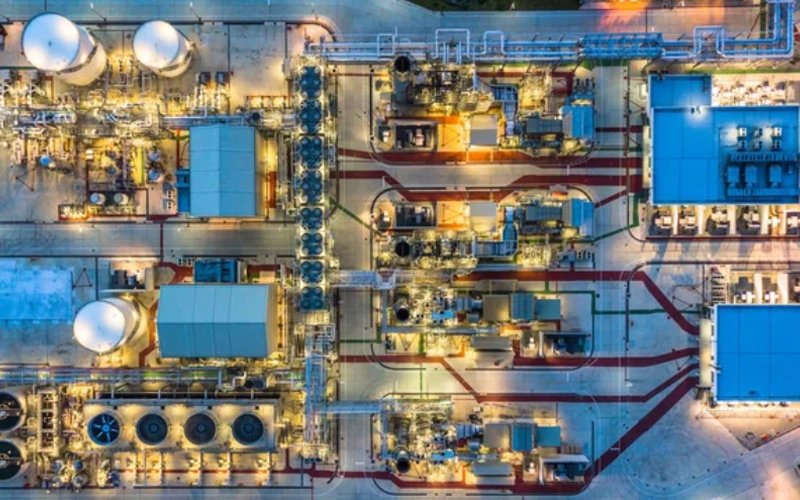
Welcome to the world of plant maintenance, where machines hum with vitality, and the heartbeat of industry resonates through the halls of production. In this dynamic realm, every gear turns with purpose, every piston pumps with energy, and every valve pulses with potential. Yet, amidst the symphony of manufacturing, there lies a crucial player often overlooked—the maintenance team. These unsung heroes are the guardians of productivity, the sentinels of efficiency, and the architects of reliability. From preventing breakdowns to optimizing performance, plant maintenance professionals are the linchpin of operational success, ensuring that the machinery of industry continues to hum harmoniously. So, strap in and prepare for an exhilarating journey through the world of plant maintenance, where every twist of the wrench and every click of the meter holds the promise of unlocking new levels of efficiency and excellence.
What is Plant Maintenance?
Plant maintenance encompasses the set of activities and processes undertaken to ensure the efficient and reliable operation of manufacturing facilities. It involves the inspection, upkeep, and repair of equipment, machinery, and infrastructure within the plant to prevent breakdowns, optimize performance, and minimize downtime.
Plant maintenance includes various tasks such as preventive maintenance, which involves scheduled inspections and maintenance activities to prevent equipment failures before they occur, and corrective maintenance, which addresses issues identified during inspections or in response to equipment breakdowns.
Additionally, plant maintenance may involve predictive maintenance techniques, which utilize data and analytics to forecast potential equipment failures and schedule maintenance proactively. Overall, effective plant maintenance is essential for maintaining safety, compliance with regulations, and operational efficiency in manufacturing operations.
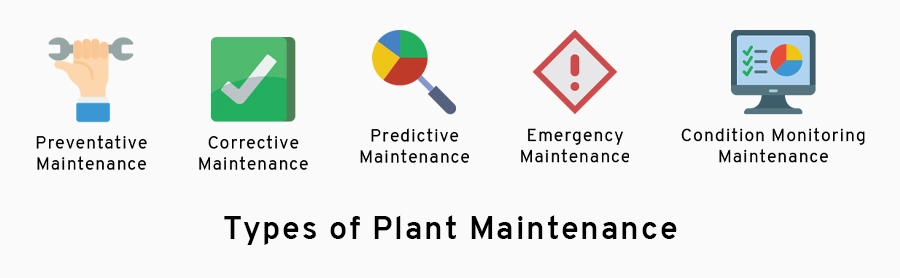
Types of Plant Maintenance
There are 5 main types of plant maintenance:
1. Preventive Maintenance
Preventive maintenance involves scheduled inspections, repairs, and replacements of equipment and machinery to prevent breakdowns and prolong the lifespan of assets. It aims to identify and address potential issues before they escalate into costly failures, reducing downtime and improving reliability.
2. Predictive Maintenance
Predictive maintenance utilizes data and analytics to predict when equipment is likely to fail, allowing for timely interventions to prevent unplanned downtime. It involves monitoring equipment condition and performance using sensors, IoT devices, and predictive analytics tools to detect early signs of deterioration and schedule maintenance proactively.
3. Corrective Maintenance
Corrective maintenance, also known as reactive maintenance, involves addressing equipment failures and breakdowns as they occur. It focuses on restoring equipment to working condition quickly and efficiently to minimize downtime and production losses. While corrective maintenance is unavoidable, proactive preventive and predictive maintenance strategies can help reduce the frequency and impact of unplanned breakdowns.
4. Condition-Based Maintenance
Condition-based maintenance relies on real-time monitoring of equipment condition and performance indicators to determine when maintenance is needed. It involves continuously monitoring equipment parameters such as temperature, vibration, and lubrication levels to detect abnormalities and trigger maintenance actions based on predefined thresholds.
5. Reliability-Centered Maintenance (RCM)
Reliability-centered maintenance is a systematic approach to maintenance that prioritizes the most critical assets and failure modes based on their impact on safety, production, and costs. It involves analyzing equipment failure modes, consequences, and risk factors to develop customized maintenance strategies that optimize reliability, safety, and cost-effectiveness.
Each type of plant maintenance has its advantages and limitations, and organizations often use a combination of these strategies to ensure the reliability, availability, and performance of their assets while minimizing costs and downtime.
Goals and Objectives for Improving Plant Maintenance
Manufacturers and distributors aiming to enhance plant maintenance should set clear goals and objectives to guide their efforts effectively. These may include optimizing equipment reliability and uptime by implementing preventive maintenance schedules and predictive maintenance technologies. Here are some specific objectives to key in on:
Maximizing Efficiency: The Importance of Plant Maintenance for Manufacturers
In the dynamic landscape of manufacturing, where operational efficiency and productivity are paramount, plant maintenance plays a crucial role in ensuring smooth operations and minimizing downtime. From automotive plants to food processing facilities, manufacturers across industries rely on effective maintenance practices to keep their production facilities running at peak performance. In this article, we’ll explore the significance of plant maintenance for manufacturers and delve into key strategies for optimizing maintenance processes.
Ensuring Equipment Reliability
One of the primary objectives of plant maintenance is to ensure the reliability and availability of critical equipment and machinery. Regular inspections, preventive maintenance, and predictive analytics help identify potential issues before they escalate into costly breakdowns. By implementing proactive maintenance strategies, manufacturers can minimize unplanned downtime, extend the lifespan of assets, and maximize overall equipment effectiveness (OEE).
Enhancing Safety and Compliance
Safety is a top priority in manufacturing environments, and proper plant maintenance plays a crucial role in ensuring a safe working environment for employees. Regular equipment inspections, safety audits, and adherence to regulatory standards help mitigate workplace hazards and minimize the risk of accidents or injuries. Additionally, maintenance activities such as equipment calibration and testing contribute to compliance with industry regulations and quality standards, fostering trust among customers and stakeholders.
Optimizing Operational Efficiency
Efficient plant maintenance practices are essential for optimizing operational efficiency and reducing production costs. Scheduled maintenance tasks, such as lubrication, cleaning, and equipment adjustments, help prevent performance degradation and maintain consistent product quality. Furthermore, predictive maintenance techniques, such as condition monitoring and predictive analytics, enable manufacturers to identify opportunities for process optimization, energy efficiency improvements, and waste reduction.
Minimizing Downtime and Production Losses
Unplanned downtime can have significant financial implications for manufacturers, resulting in lost production capacity, missed deadlines, and dissatisfied customers. In fact, the average manufacturing plant runs at about 60% of its full potential. Effective plant maintenance strategies aim to minimize downtime by proactively addressing equipment failures, minimizing repair times, and optimizing spare parts management. By implementing preventive and predictive maintenance measures, manufacturers can maximize uptime and meet production targets consistently.
Investing in Technology and Automation
Advancements in technology, such as sensor-based monitoring systems, internet of things (IoT) devices, and predictive maintenance software, are revolutionizing plant maintenance practices. Manufacturers are increasingly leveraging these technologies to collect real-time data, monitor equipment health, and predict potential failures before they occur. Automation tools streamline maintenance workflows, improve data accuracy, and enable proactive decision-making, ultimately enhancing overall plant performance and competitiveness.
Technologies for Leveraging Better Plant Maintenance Strategies
In order to maximize the operational potential throughout your facilities, adding more technologically advanced systems and tools are vital. Several technologies can be leveraged to improve plant maintenance, including:
- Predictive Maintenance (PdM) Systems: Predictive maintenance utilizes data analytics and machine learning algorithms to predict equipment failures before they occur. By monitoring equipment condition in real-time and analyzing historical performance data, PdM systems can identify early signs of degradation or impending failures, allowing for timely maintenance interventions to prevent unplanned downtime.
- Condition Monitoring Sensors: Condition monitoring sensors, such as vibration sensors, temperature sensors, and pressure sensors, are deployed on critical equipment to continuously monitor key parameters indicative of equipment health. These sensors provide real-time data on equipment condition, enabling early detection of abnormalities or deviations from normal operating conditions.
- Computerized Maintenance Management Systems (CMMS): CMMS software helps organizations manage and track maintenance activities, work orders, and asset information efficiently. By centralizing maintenance data and automating maintenance workflows, CMMS systems enable better planning, scheduling, and execution of maintenance tasks, leading to improved asset reliability and maintenance efficiency.
- Radio Frequency Identification (RFID): RFID technology uses radio frequency signals to identify and track assets, equipment, and inventory in real-time. By tagging equipment and assets with RFID tags and deploying RFID readers throughout the plant, manufacturers can automate asset tracking, streamline inventory management, and improve maintenance workflows.
- Real-Time Location Systems (RTLS): RTLS technology utilizes wireless communication technologies, such as Wi-Fi, Bluetooth, or Ultra-Wideband (UWB), to track the real-time location of assets, personnel, and equipment within the plant. By integrating RTLS with plant maintenance systems, manufacturers can improve asset visibility, optimize equipment utilization, and enhance safety and security.
Conclusion
In today’s competitive manufacturing landscape, plant maintenance is more than just a routine task—it’s a strategic imperative for driving operational excellence and maintaining a competitive edge. By prioritizing equipment reliability, ensuring safety and compliance, optimizing operational efficiency, and leveraging technology and automation, manufacturers can maximize the performance of their production facilities and achieve sustainable growth in the long term. With proactive maintenance practices in place, manufacturers can navigate challenges, mitigate risks, and capitalize on opportunities for continuous improvement and innovation.