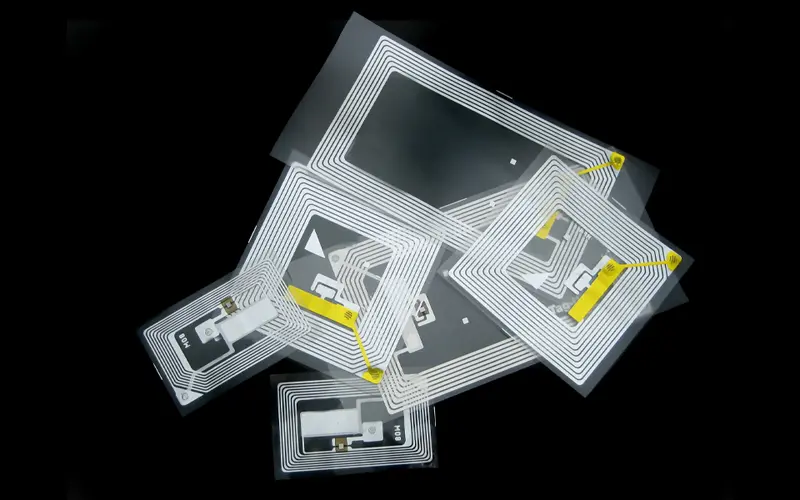
RFID offers a wide range of solutions across numerous industries and environments. In some scenarios, being able to get a live look at an environment is advantageous whereas some operations only needs to review the latest status of items. There are two kinds of RFID tag – passive and active. Active RFID tags come equipped with a battery to ensure the tag can be in constant communication with a frontend RFID system, thereby accommodating for a live tracking application. For projects that don’t require live communication or tracking, passive RFID. Your particular needs will ultimately decide whether your RFID project requires passive or active RFID tags.
What is Passive RFID?
Passive RFID is a form of RFID that does not use a battery. Instead, passive tags reflect radio-frequency signals emitted from an RFID reader to identify assets and hardware. This form of RFID is a cost-efficient solution for tracking lower-value, smaller items. It can also be used to monitor the movement of products and equipment in warehouses and manufacturing environments.
How Passive RFID Works
Tag
Item(s)
Reader Sends Signal
Tag Responds with Data
Data Captured in Real Time
Items or Info Updated
Advantages over Active RFID
Passive RFID offers several key advantages over active RFID in environments like warehouses and manufacturing plants. Most notably, passive RFID tags are smaller, more cost-effective, and require no battery, making them ideal for tracking large volumes of assets or inventory at scale. Because they are powered by the signal from the reader itself, passive tags have a longer lifespan and require less maintenance, which is especially valuable in high-traffic or rugged environments.
Additionally, passive RFID systems are easier to deploy in dense, metal-heavy areas like warehouse shelves or manufacturing zones, where active tags may suffer from signal interference or require more complex infrastructure. For operations focused on inventory accuracy, item-level tracking, and cost efficiency, passive RFID delivers a practical, scalable solution.
Common Passive RFID Use Cases
Passive RFID is widely used across industries due to its affordability, durability, and versatility. These tags are ideal for tracking high volumes of items with minimal infrastructure and maintenance. From inventory control to asset tracking, passive RFID helps organizations streamline operations, reduce manual labor, and gain real-time visibility without the need for active power sources.
Below are some of the most common and effective use cases for passive RFID:

Tracking Inventory
Passive RFID tags are a great way to track inventory. Moreover, they are small, lightweight, and easily readable. In fact, if items or inventory is ordered properly, organizations can expect read rate accuracy of 99% or more.
Keeping track of assets and materials can be challenging for most businesses. Whether it’s components on a production line, finished products being shipped out or industrial containers that need to be returned to the manufacturer, tracking these items can be an important part of efficient logistics.
One of the most common passive RFID use cases is to track inventory in warehouses. This can be done in a multitude of ways – one of which is by placing a tag on each item and scanning it using an RFID reader to determine its status. If inventory is tagged, warehousing teams can place RFID portals at strategic locations such as dock doors to ensure inventory is scanned as soon as it enters or exits the warehouse
The system can also be used to track personnel in facilities. A portable RFID reader allows staff to scan multiple items at once and input them into a tracking system.
RFID inventory systems can help to increase efficiency and reduce costs. They are a cost-effective alternative to barcode-based inventory tracking systems and can be implemented in warehouses and distribution centers. In addition, they allow for greater visibility and more data to be stored on each tag, which can help to improve the overall accuracy of a company’s inventory.
Work in Process Tracking
The manufacturing process can be a complex and challenging operation. Many companies struggle to track work in progress (WIP) to ensure production runs efficiently. Without WIP visibility, companies may waste money or produce products incorrectly if a production error occurs.
RFID can be used to track work in process, and it can help companies maintain a lean manufacturing system by maintaining low inventory levels and reducing wastage. Additionally, RFID can be used to detect any errors that occur on the production floor by reporting deviations or exceptions immediately.
In addition, RFID can be used to track equipment and other assets. This allows companies to reduce lost equipment and improper put away, ensuring a successful WIP methodology.
Active and passive RFID tags are both available for use in asset tracking systems. The type of tag you choose will depend on how you plan to use the system and what you need to track.
Passive RFID tags are often small, but they can be made from different materials and can withstand harsh conditions. They can also be embedded in equipment or be used as labels.
They can be read by an antenna that is attached to an RFID reader. The reader emits radio waves that power the microchip inside the tag, which then sends its information to a database. The reader can be mobile or fixed, and it depends on how far the tag needs to be read.
How NAFECO Improves Work-in-Process System
with CYBRA’s RFID Software Application
NAFECO, a leading provider of safety gear for emergency responders, faced issues in tracking thousands of garments moving through its facility. To streamline its work-in-process operations, NAFECO implemented CYBRA’s Edgefinity IoT RFID software.
Asset Tracking
Asset tracking is a necessary component of any business, but it can be labor intensive and costly to implement. Historically, companies have used barcodes or serial numbers to track assets. However, barcodes require staff to locate the barcode and then scan it or input the serial number into a database.
Fortunately, there are many efficient and cost-effective alternatives to manual asset tracking systems. Modern RFID asset tracking applications can provide more granular visibility into the movement of individual assets than barcode scanning or manual entry.
Passive RFID is a popular option for asset tracking because it uses low-frequency radio waves and doesn’t require batteries. This type of tag is also easy to deploy and can be used on static or moving assets that aren’t constantly changing locations.
For example, passive RFID can be used for tracking construction equipment such as tools and trucks. It’s a great way to get a better understanding of the condition and location of each piece of equipment, which can be useful for maintenance and repair work.
Asset management solutions can also help spot expensive operational delays, which can significantly impact your bottom line. This is because an automated system reduces the amount of human interaction required to track assets, leaving your employees free to focus on their job duties.
Other Use Cases
In addition to core functions like inventory tracking, asset management, and work-in-progress monitoring, passive RFID supports a range of specialized applications in manufacturing and distribution environments. These lesser-known use cases help organizations streamline compliance, improve safety, and tighten control over internal processes.
Some examples include:
- Tool calibration tracking – Automatically log and monitor calibration schedules for mission-critical tools and equipment.
- PPE and uniform monitoring – Ensure employees are wearing the proper safety gear in restricted or hazardous zones.
- Quality control linkage – Connect components or batches to inspection results, test reports, or compliance documentation for easier traceability.
- Returnable packaging identification – Track reusable containers, pallets, or bins as they move through closed-loop supply chains.
- Access control for restricted equipment or zones – Use RFID to grant or restrict access to high-risk machinery or controlled inventory areas.
These use cases demonstrate how passive RFID can go far beyond basic tracking—delivering value in compliance, safety, and resource optimization.
Passive RFID Benefits
There are numerous innovative ways to use passive RFID to improve efficiency and accuracy in a variety of industries. Once RFID is deployed within an organization, teams will enjoy an increase in operational visibility and efficiency.
Here are some additional benefits of using passive RFID:
- Low cost: Passive RFID tags are relatively inexpensive, which makes them a cost-effective solution for many applications.
- Ease of use: Passive RFID tags are easy to use and can be applied to a variety of objects.
- Range: Passive RFID tags have a range of up to 100 meters, which makes them suitable for a variety of applications.
- Durability: Passive RFID tags are durable and can withstand harsh environments.
- Security: Passive RFID tags can be encrypted to protect data.
Overall, passive RFID is a versatile technology that can be used to improve efficiency and accuracy in a variety of industries.
Getting Started with an RFID Pilot Program
Whether you’re managing a warehouse, production facility, or retail operation, the benefits of passive RFID are clear: greater visibility, fewer errors, faster processes, and smarter use of labor and assets. To unlock these advantages, the best first step is launching a focused RFID pilot program.
Start by identifying a specific use case—like inventory management or asset tracking—and define clear goals around accuracy, efficiency, or labor savings. From there, choose the right tags, readers, and software platform to support your needs, and monitor the results closely. A well-executed pilot can demonstrate immediate value while building the foundation for a scalable, long-term RFID strategy.
Interested in RFID?
An RFID tracking system can help organizations of all sizes improve their supply chain efficiency. Contact the CYBRA team to schedule a demo today.