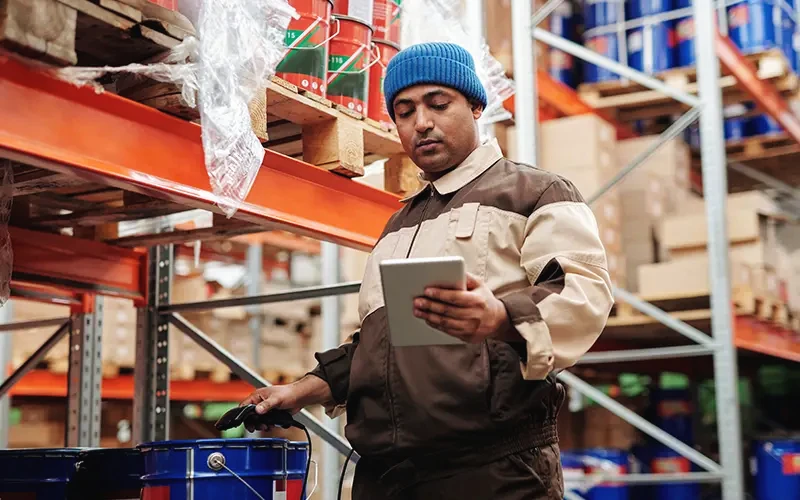
The average size of a warehouse is more than 50,000 square feet (Source: wh1.com). Keeping a warehouse efficiently organized is more important than ever. Space is at a premium for many distribution centers, and for warehouse renters rates are likely going to increase in 2024 (according to dcvelocity.com). Regardless of how well your team keeps track of inventory and equipment it is a challenge to do so in such a large area. Whether your warehouse is large or small, there are certain warehouse mistakes that can hinder productivity and fulfillment efficiency.
The best way to avoid these mistakes is to plan ahead. It can help your warehousing operation grow in a sustainable manner.
Common Warehouse Mistakes
Today, supply chains need to be nimble. Faster turnaround times, higher consumer expectations, and stiff competition requires manufacturers and distributors to deploy highly efficient shipping strategies. Unfortunately, many warehousing teams fail to leverage modern techniques to alleviate common issues such as inventory overstocking or packing errors. Below is a shortlist of the most common warehouse mistakes we see among clients and partners.
1. Overstocking and Understocking
Overstocking, also known as “surplus inventory,” is one of the most common warehouse mistakes that can have serious negative impacts on productivity and fulfillment efficiency. Moreover, it can be a costly business problem for retailers. Via RetailWire, overstock issues costs retailers over 3% in lost revenue
Overstocked items take up valuable shelving or storage space, hindering the placement of other products. In addition, they can cost more to store and ship than a product that isn’t on sale.
In addition, overstocking can create a risk of expired or obsolete stock. This can lead to a loss of revenue and profits.
Managing inventory is critical to the success of any retail or e-commerce company, but it can be challenging. Having the right knowledge, strategic planning, and smart tools can help you ensure that your inventory levels are appropriate – no excess or shortages.
The best way to avoid overstocking is to keep accurate data on how many items you have in stock, as well as customer demand and seasonality. Accurate data can also help you discover trends and predict future sales.
Inventory is a business asset, and keeping it at optimal levels can help you meet your sales goals, maximize profitability, and maintain strong customer loyalty. Having the right data value structure will help you achieve this, and it’s key to have access to the right alerts, tracking, and sales insights.
Overstocking often occurs because of a lack of reliable inventory management tools and strategies. This is especially true if your business is new or has limited resources. Alternatively, your inventory may be inaccurate due to stolen goods, returns, shipment variances, or misplaced items.
Another cause of overstocking is a failure to plan for demand. Fortunately, there are tools that help you forecast and optimize your inventory for peak seasons and demand.
For instance, an advanced inventory management solution like Inventory Planner helps you categorize your stock based on customer priority and demand. This means you focus on Category A items that are most profitable for your business, and you can order them on a regular basis to avoid frequent reordering.
Additionally, you can set up automated notifications when your stock reaches a certain threshold so that you’ll be able to reorder before the item goes out of stock. This will help you avoid the loss of cash and the sunk costs associated with dead inventory.
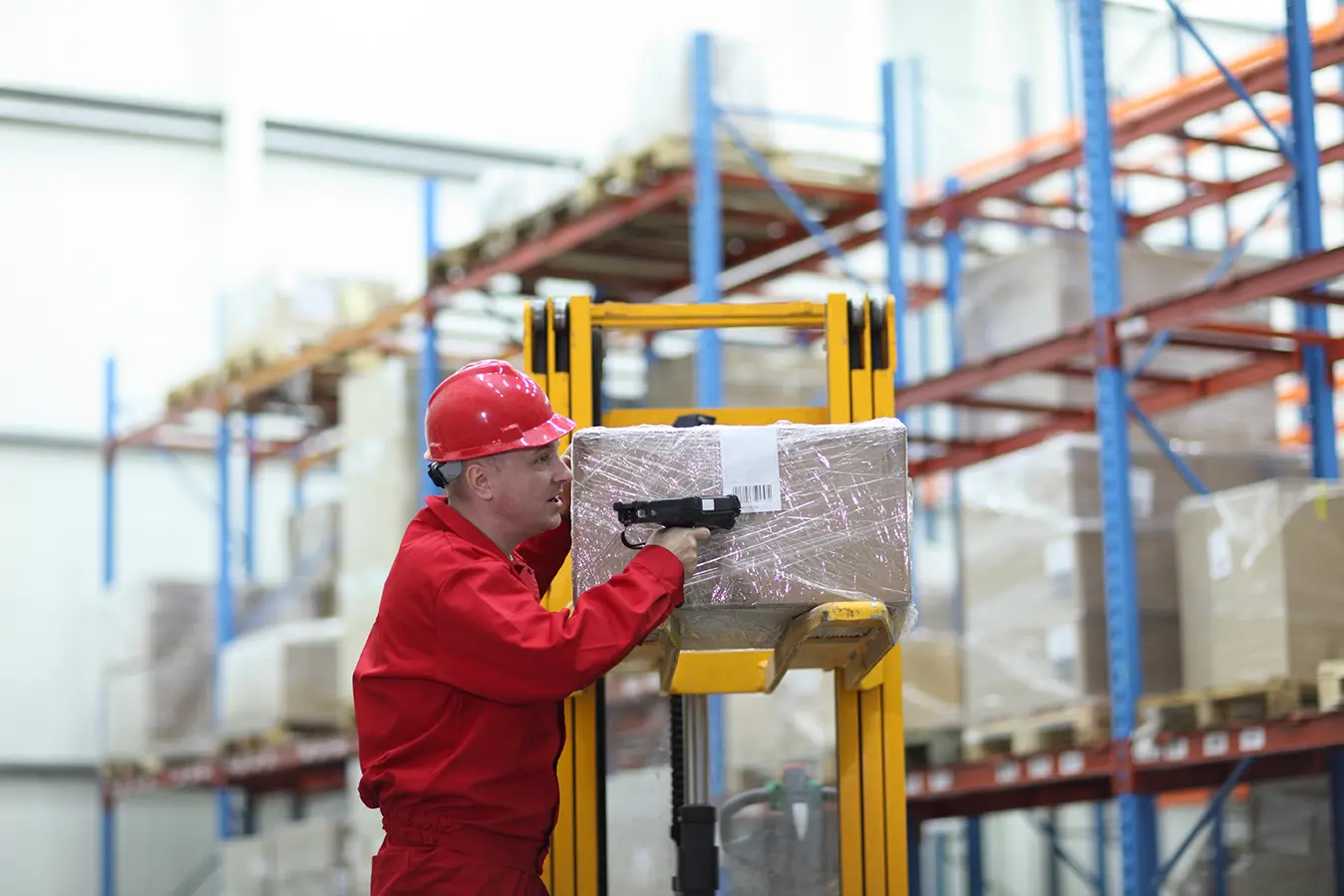
Ignoring basic safety protocols is one of the most common warehouse mistakes that can cost companies.
2. Not Following the Health and Safety Procedures
One of the most costly warehouse mistakes is taking shortcuts on safety protocol enforcement. If your business relies on warehouse operations to deliver goods to customers, it is essential that you implement the necessary health and safety procedures at work. This will ensure the safety of your employees as well as the integrity of the products that they store.
Besides that, adhering to warehouse safety regulations also helps you save on costs like medical expenses and insurance premiums. It can also help you avoid costly legal proceedings that could have a negative impact on your reputation.
In general, implementing safety protocols is important for every type of workplace, but it can be especially critical for warehouses where the risk of injury can be greater than other industries. For example, manual lifting and handling can strain the body and cause serious injuries. In addition, dangerous chemicals can be hazardous if handled without the appropriate training and equipment.
According to the Occupational Safety and Health Administration (OSHA), a large percentage of workplace accidents involve heavy equipment, such as forklifts. In order to prevent these accidents, employees should be properly trained and licensed before they start driving forklifts or operating other heavy equipment.
Another way to prevent warehouse accidents is to create a safety management team. This team should be made up of people who can proactively identify and address the hazards at work. They should then be able to develop a safety plan and communicate it to the employees.
For example, a safety coordinator can be responsible for making sure that employees wear proper protective gear at all times when using machinery. This includes a hard hat, eyewear and gloves, as well as ensuring that the safety signs are appropriately placed in the warehouse and that all emergency exits are clearly marked.
Lastly, employees should be regularly given safety training on how to give first aid in case an accident happens. This could save lives and reduce the severity of the injuries.
It is very important that employees follow the proper safety procedures at work, including following all instructions and guidelines set forth by their managers. This will ensure that they are not only healthy and safe but also productive in their roles.
3. Not Creating a Warehousing Calendar
Creating a warehouse calendar may not be at the top of your list of priorities, but it can save you from the headache of manually rescheduling orders. Besides, it’s a good way to demonstrate your commitment to quality and efficiency. It may even help your sales and service team win new customers.
Warehousing Calendar Tools
If you have multiple warehouses in your organization, it’s a good idea to create a warehouse calendar for daily operations. This will ensure that manufacturing orders are scheduled during the operational days of each warehouse and avoid delays or rescheduling. The warehouse calendar will also be helpful during the planning process when MRP considers the availability of warehouses during the manufacturing order cycle.
Creating a warehouse calendar for weekly operations ensures that your team will know when to replenish inventory and avoid sending orders out with short parts. By planning your replenishment in advance, you can eliminate redundancies in labor costs and ensure that each order is complete from start to finish. Not only that, but it can also help you to reduce the cost of short picks and minimize overflow in your receiving area.
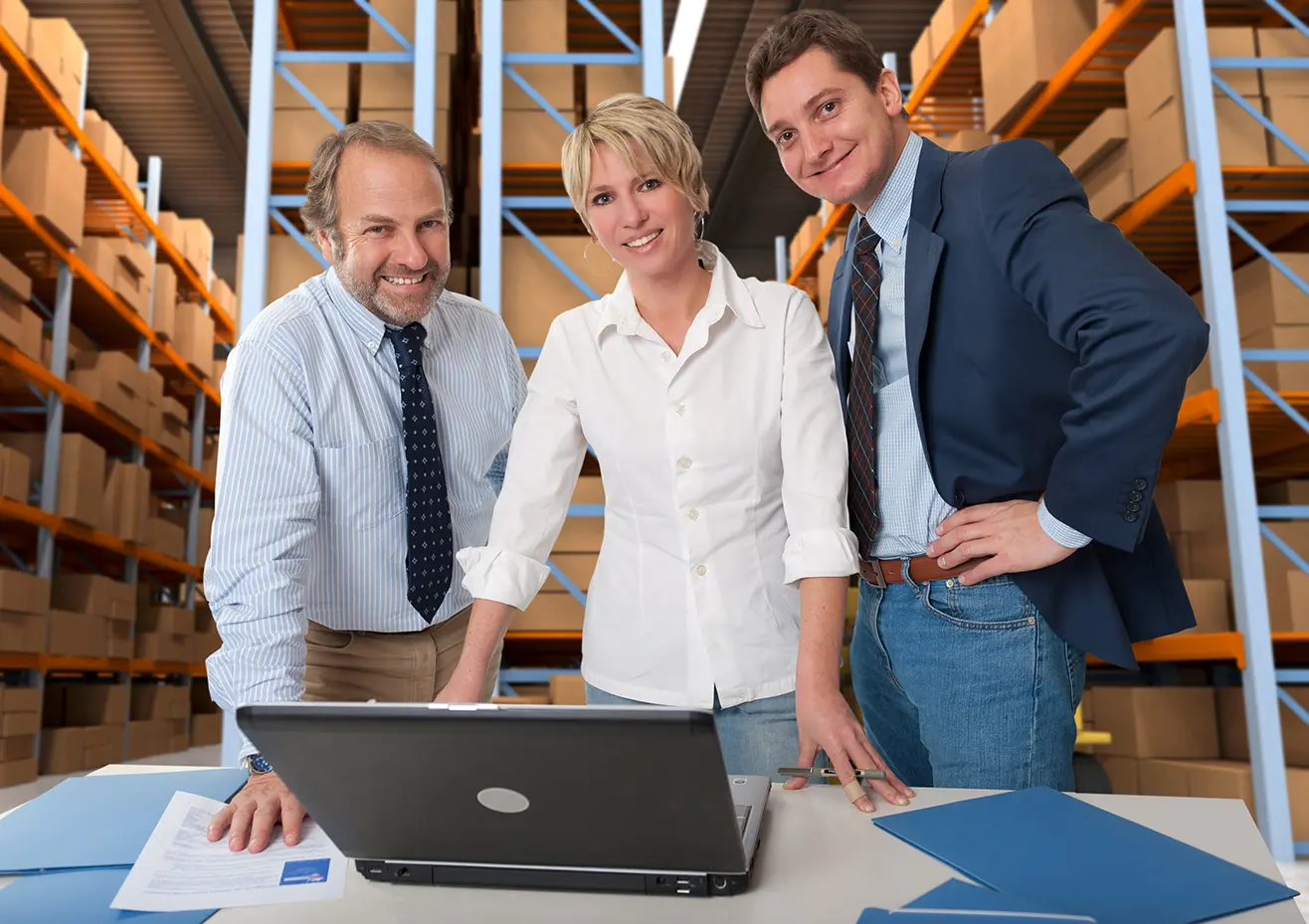
Help your fulfillment mitigate warehouse mistakes by creating a calendar and effective putaway strategy.
4. Not Having a Proper Putaway Strategy
A warehouse is a complex place, and it is important to have a proper plan in place. This will help your workers to work as efficiently and effectively as possible. It will also ensure that you have the right amount of space for your inventory, and it will help to keep your costs down.
If you don’t have a putaway strategy in place, you’re likely to make warehouse mistakes that could affect your operations and your bottom line. These mistakes could cost you a lot of money and lead to long-term damage to your business.
The first step in creating a putaway strategy is to gather relevant data and information. This includes traffic patterns, inventory numbers, shipping regulation information, and receiving schedules. This will help you determine which metrics are the most important and which ones you need to track in order to run your operations effectively. Additionally, these data points should help you identify bottlenecks as well as opportunities to speed up operations.
You should also make sure that you have the necessary tools in place to collect the data and analyze it. This will allow you to identify problems and opportunities that you can address in a timely manner.
Another mistake that can make a big impact on your business is not having a good barcoding system in place. This can result in a variety of issues, including lost inventory, incorrect inventory levels, and faulty records. A barcoding system can help you to easily track your inventory, and it can also help to eliminate manual data entry for increased accuracy.
Having a barcoding system in place will also help you to avoid reversing orders because of incorrect inventory levels. This can save your business a huge amount of money and time in the long run.
The next step in creating a proper plan is to involve your employees in the process. This will ensure that they have a clear understanding of how your warehouse works and will allow them to give you feedback on the layout.
You should also try and incorporate your friends and family in this process as well. This will ensure that they are able to role-play their jobs and see where changes should be made.
5. Not Utilizing Modern Technology
When it comes to warehouse technology, there are many options for businesses. These solutions can help automate tasks, increase efficiency and improve communication between employees. However, they can also create new problems.
The key to implementing a piece of technology is to make sure that it will benefit the entire warehouse. This can be accomplished by taking a long look at your processes and layout before making any changes, and then choosing products that are a good fit for those areas.
For example, a modern warehouse management system can be a great way to streamline your operations and ensure that you are able to keep up with demand and inventory records. This is an important step to take because it will allow you to ensure that you are able to fulfill customer orders in a timely manner without any errors.
Another common mistake warehouse managers make is not utilizing technology at work. This can lead to a variety of issues, including missed deadlines and low productivity.
One of the biggest ways that a company can avoid this problem is by utilizing technology to communicate with each other and their customers. Using group chat applications and mobile devices can help keep everyone connected and on the same page.
It can also be helpful to set up project management software so that workers can delegate their responsibilities and track progress. This is a way to make sure that each employee is working on the right projects at the right time and that they aren’t wasting time on tasks that aren’t critical.
Similarly, when it comes to employee training, it is always best to ensure that employees are fully educated on the use of new technology. This includes both training them on how to use it properly and teaching them the benefits that they can get from using it.
It is also a good idea to create a company-wide policy about technology usage so that every member of the team understands what they are expected to do when it comes to using it at work. This will help them to feel more empowered and engaged with their jobs.
One of the most robust modern technologies available for manufacturers and distributors is RFID. With an RFID tracking system, brands of all sizes can improve inventory accuracy, and reduce warehouse mistakes by ensuring equipment, products, and even employees are where they should be.
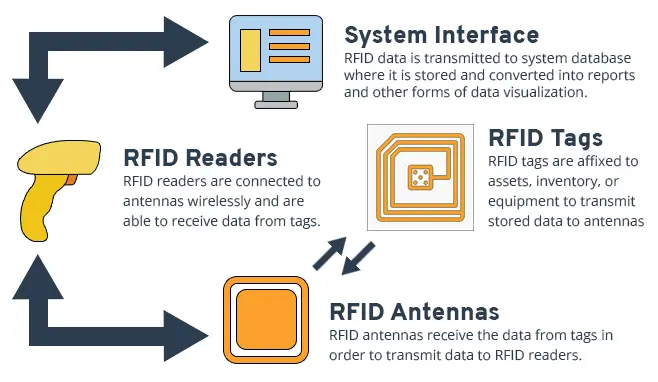
How RFID Can Help Fix Common Warehouse Mistakes
RFID is a technology that can be used to track inventory and items in warehouses. It has a number of benefits for warehouses, including ensuring that they are operating efficiently and effectively.
It can help them avoid a lot of common problems that may occur in warehouses, such as inventory inaccuracy, redundant processes, and poor quality control. It can also help them save money and time.
Using RFID to Locate Products
For brands with thousands of SKUs, looking for one product can be a major challenge. This time spent searching for a particular item can be a waste of valuable resources that could be better invested in other areas of your business.
But if you have an inventory management system that is integrated with RFID, then you can see what items are in which area of the warehouse at any given moment. This can help you reduce the amount of time that your staff spends locating goods, which in turn can increase your warehouse’s productivity and efficiency.
You can even use RFID to verify that the right products are being added to your inventory and shipped to retail stores or customers if you sell online. This will help you avoid inventory inaccuracies that can cause a customer to be dissatisfied with your products or services.
Fixing a Recurring Problem with Your Inventory
If your warehouse inventory is not accurate, it can be difficult to keep track of it. This can lead to many different issues, from in-store stockouts to shipping errors. To prevent these issues from happening, you need to make sure that your inventory is correct and updated all the time.
The most effective way to achieve this is by using RFID. This technology can be used to scan the barcodes that label your products and then send the information directly to a software application.
In addition to scanning barcodes, you can also use RFID to keep track of your inventory using passive tags that can be placed on the items. When the RFID tags come into contact with the fixed readers, the data is automatically transferred to your software.
You can also use RFID to track the movement of your products, so you know when they need to be reordered or replenished. This helps you avoid out-of-stock situations and provides you with a timeline for when to reorder to keep your inventory up to date.
Handling the Cost of Your Inventory
The number of items in your inventory can be a big part of your revenue, so it’s important that you know how much you have to sell. This can help you make informed decisions on how much to restock your warehouse, which in turn can help you maximize your profits.
Conclusion
Warehouse management is a complex process that requires careful planning and execution. Even the most experienced warehouse managers can make mistakes from time to time. But, by adopting new technologies and strategies, you can help to avoid common warehouse mistakes and improve the efficiency and accuracy of your warehouse operations.
Interested in RFID?
An RFID tracking system can help organizations of all sizes improve their supply chain efficiency. Contact the CYBRA team schedule a demo today.