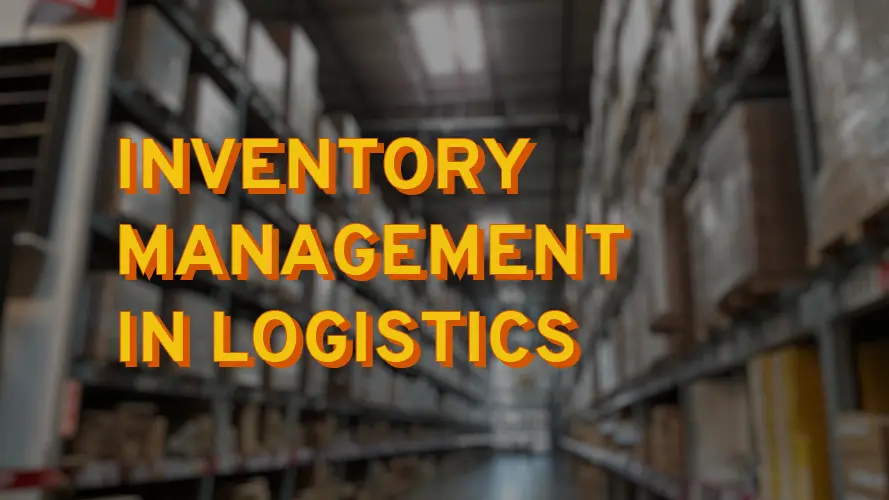
For shippers and distributors, configuring how inventory can be stored and moved effectively is nothing short of essential. The efficacy of their supply chain depends on it – and therefore their entire business. Managing inventory when done at scale will eventually require logistical operations. Inventory management in logistics ensures accurate forecasting and precise inventory levels, as well as fulfilling orders across a wide array of channels. Effective tracking of inventory can help organizations save millions by avoiding unnecessary spending, production, or storage and also increases profits through more efficient use of warehouse space. The right system minimizes costs by keeping just enough (the Goldilocks balance) of raw materials on hand to meet demand. This reduces out-of-stock events and leads to happier customers.
But there’s more to it than just avoiding common warehouse mistakes. In this article we’ll explore how warehousing teams can reach the highest levels of accuracy and fulfillment with inventory management in logistics.
What is Inventory Logistics?
Inventory logistics is the system of managing the movement, storage and control of goods in warehouses and other facilities prior to production, shipping and selling. Companies must understand how to efficiently manage their inventory in order to minimize stockouts and costly delays.
The main inventory types include:
- Raw materials
- Work-in-progress
- Merchandise and supplies
- MRO (maintenance, repair, and operations)
- Finished goods.
The top-level categories can be further broken down into specific types to help businesses classify and track their inventories more accurately and efficiently.
Cycle inventory includes items that are ordered in lots and on a regular basis, often for use in production or as part of some other process. This inventory can also be divided into several different classes, including slow movers and fast movers. The distinction between these classes helps a company determine how much inventory to hold and when it is needed.
In-transit inventory records the products and materials in transit between warehouses, distribution centers and manufacturing plants. This can be a long-term inventory type because it can take weeks for goods to move from one location to another. Safety stock inventory is the product and material a company keeps on hand to mitigate problems in its production processes, supplier delays or unexpected increases in customer demand.
Keeping too little inventory may prevent you from being able to fill client orders, while keeping too much may cause your company to waste money on excess stock. The goal is to find the optimal balance between these extremes by determining the right mix of inventory types for your business.
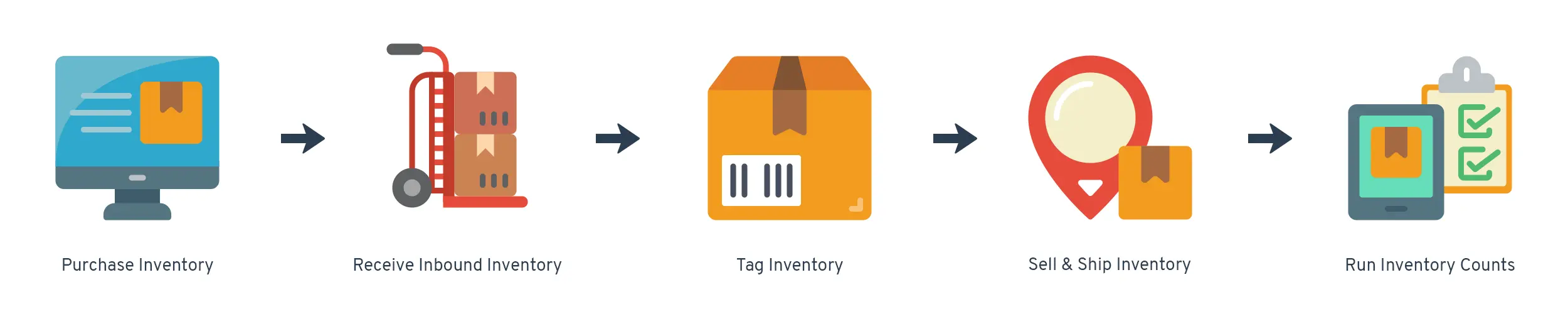
Inventory Logistics KPIs
Inventory management isn’t just about tracking how much inventory you buy and sell. It’s important to go deeper to identify trends, spot operational weaknesses, and to find opportunities for improvement. Here are a few inventory logistics KPIs warehouse teams should keep in mind when evaluating their supply chain operations’ efficiencies.
Inventory Turnover
The inventory turnover ratio measures how fast a company sells its stock-keeping units (SKUs). A higher ratio suggests strong sales and depletion of inventory quickly.
The rate at which a product sells is important because holding inventory costs money: storage, handling fees, transportation, insurance and employee salaries. It also carries the risk of theft, natural disasters and obsolescence.
Knowing which products are moving and at what speed can help inform everything from pricing strategy and supplier relationships to promotions and the product lifecycle. Having the right inventory management system and a clear understanding of different methodologies like FIFO, LIFO and average inventory can make all the difference. This means faster order fulfillment, which leads to a better customer experience. It also reduces the cost of carrying excess inventory, freeing up capital for other investments. A well-organized warehouse can also reduce labor costs and improve warehousing efficiencies. This is particularly critical for fast-moving items and seasonal products, where a low turnover could spell trouble.
Inventory Costs
Businesses can reduce inventory costs by using a digital or centralized system to track and update information. This enables leaders to track several different inventory costs, including the cost of carrying the inventory itself and the costs associated with replenishing it when it goes out of stock.
Companies may carry extra inventory to guard against stockouts, a practice known as safety stock. Typically, the level of safety stock required to protect against stockouts is a tradeoff decision between the risk of a stockout and the carrying cost of the safety stock.
Businesses can also minimize inventory holding costs by optimizing space utilization in leased or contract warehouses through narrow aisle handling equipment, mezzanines and layout changes. They can reduce inventory transaction costs by leveraging EDI, reducing order-processing errors and expediting shipments to prioritize high-demand products. They can reduce cycle stock inventory by prioritizing products based on sell-through rate, minimizing QA and QC work during changeovers and reducing rework of defective product.
Inventory Risk
Inventory consists of goods, materials or supplies in a warehouse prior to production, shipping and selling. This asset is a pillar of a company’s balance sheet and incurs costs associated with purchase, storage, handling and insurance. Inaccurate forecasts and poor inventory management can wreak havoc on profit margins.
For companies that operate a JIT model, a sluggish supply chain can result in insufficient inventory to meet customer demand. This is also known as a stockout or a shortage.
On the other hand, an abundance of inventory can create waste and hide operational issues that need to be addressed. For example, the presence of damaged or obsolete products may result in higher disposal and storage costs or lost sales. Optimized storage and professional handling can minimize these types of damage. The more efficient fulfillment centers are equipped to store and handle inventory safely and efficiently to reduce damage and obsolescence. The resulting reduced risk allows you to maximize inventory turnover.
Inventory Management Software
Whether you’re a small business keeping track of inventory with pen and paper, or a large company using specialized enterprise resource planning software, an accurate and efficient way to count your stock is essential. Counting manually can take time and is prone to error, but using handheld devices to scan product barcodes or RFID tags simplifies the process and minimizes data entry errors.
Once products arrive at your facility, you must inspect, sort and store them to maintain control of your inventory. You may even have to consider using drop shipping or other order fulfillment methods for certain products.
To optimize your stock levels, you must understand your current and projected sales. A good inventory management system determines reorder points and quantities, and makes recommendations to minimize the amount of money you spend on carrying costs, such as storage, handling fees and insurance. It also helps you negotiate better terms with your suppliers.