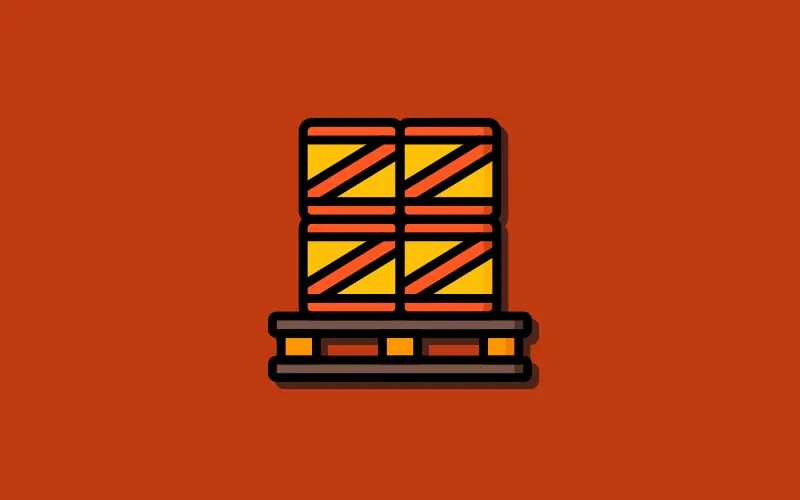
Update for 2025
As of 2025, RFID usage in pallet tracking has seen significant advancements tied to rising global adoption and market expansion. The pallet tracking system market alone is estimated to reach $588 million in 2025, growing at a CAGR of around 12% through 2033 (via Achieve Market Research).
Meanwhile, the broader RFID market is projected to hit $17.1 billion in 2025—expanding at approximately 11.9% annually to reach $37.7 billion by 2032 .
The standard U.S. pallet is typically 13.333 square feet in size, but plays a massive role in ensuring a warehouse runs efficiently. Pallets are a fundamental component of warehouse operations, serving as the primary method for storing, handling, and transporting goods.
But for a multitude of reasons, pallets are far too often lost, misplaced or stolen. In fact, companies are losing millions of dollars each year to stolen or lost pallets.
Keeping track of pallets is essential because they represent not only the storage units for goods but also a critical logistical asset. Lost, misplaced, or damaged pallets can lead to inventory discrepancies, increased operational costs, and potential delays in order fulfillment.
Proper tracking ensures that the right products are in the right place at the right time, which is crucial for maintaining smooth warehouse operations, minimizing waste, and delivering a higher level of customer service.
Current State of Pallet Tracking
In the United States, it is estimated that there are around 1.9 billion pallets in circulation, with most warehouses holding several thousand pallets at any given time, depending on their capacity and operational needs. The number of pallets used in a warehouse can vary significantly based on the warehouse’s size, purpose, industry, and layout. However, on average:
- Small Warehouses: May have 5,000 to 10,000 pallets in use at any given time.
- Medium-Sized Warehouses: Often store between 20,000 and 50,000 pallets.
- Large Warehouses: Large distribution centers or regional warehouses may contain 100,000 to 200,000 pallets or more.
Source: Virginia Tech Center for Packaging and Unit Load Design
Currently, many warehouses use barcode scanners or simply manual tracking systems. But in order to better track such a large amount of equipment, organizations need a more streamlined approach. RFID (Radio Frequency Identification) technology is increasingly used in modern warehouses for tracking pallets.
In this article, we will explore what RFID pallet tracking is, how it works, its benefits, challenges, and why it is crucial for the future of supply chain management.
Lost Reusable Equipment
Lost reusable packaging assets (include not just pallets but also crates, containers, rolling carts, and trays) end up costing American business $750 million to $1 billion each year.
Source: Food Marketing Institute
Revolutionizing Supply Chains Management with RFID
RFID is radically changing warehousing and distribution by enabling real-time visibility, increasing operational efficiency, and reducing labor costs. Unlike traditional barcode systems that require manual scanning and line-of-sight, RFID tags can be read automatically from a distance, allowing for faster, more accurate tracking of inventory and pallets throughout the supply chain.
Improved Inventory Accuracy
RFID technology can boost inventory accuracy in warehouses to nearly 99%, compared to 85-95% with barcode systems.
Reduced Labor Costs
RFID automates inventory tracking and reduces the need for manual scanning, which can lead to labor cost reductions of up to 30%.
Time Savings
RFID systems can scan multiple tags simultaneously, speeding up inventory counts and reduces time spent on inventory management by up to 80%.
Minimized Shrinkage
Using RFID technology reduces inventory shrinkage by providing better visibility – this leads to a decrease in lost or misplaced items by up to 50%.
Increased Efficiency
RFID tagging helps warehouses to achieve a productivity increase of 20-30%, as automated tracking accelerates the processes of receiving, picking, and shipping.
Out-of-Stock Reduction
The use of RFID technology helps reduce out-of-stock situations by up to 50%. Real-time inventory visibility ensures prompt replenishment.
Using RFID for Pallet Tracking
RFID pallet tracking uses RFID technology to monitor and manage pallets across the supply chain. RFID uses radio frequency signals to automatically identify and track tags attached to pallets. Tags store electronic details about each pallet’s contents, location, and movement.
Unlike traditional barcode systems that require manual scanning, RFID tags can be read automatically, even at a distance, providing real-time information on pallet movement throughout a facility or across different locations.
A combination of RFID tags, readers, and a software system work together to ensure smooth operation. RFID tags are affixed to the pallets, and the readers are placed strategically at locations like entry and exit points, storage racks, warehouse bins, and loading docks to gather information from the tags. The data is then processed and visualized in the software system, giving companies a clear picture of their inventory.
How Does an RFID Pallet Tracking System Work?
RFID pallet tracking makes it possible to see exactly where your pallets are — automatically, in real time, and without manual scanning.
Each pallet gets an RFID label with its ID, contents, origin, and destination. You can use passive tags, powered by nearby readers, or active ones with built-in batteries. RFID readers pick up tag signals at key points like loading docks. The software processes the data and shows real-time location updates.
As pallets travel through your facility, RFID readers — or portals — pick up their signals. These portals are installed at key choke points: dock doors, staging areas, warehouse zones, and even aisle entrances. When a tagged pallet passes through a portal, the system logs its location and movement instantly. No scanning, no delays.
Each portal sends its data to your central tracking system, which updates instantly. This gives your team a live view of where pallets are, what’s ready to ship, and where potential issues might be building. Whether you’re managing inbound receipts or outbound shipments, RFID portals ensure nothing gets missed — and nothing gets lost.
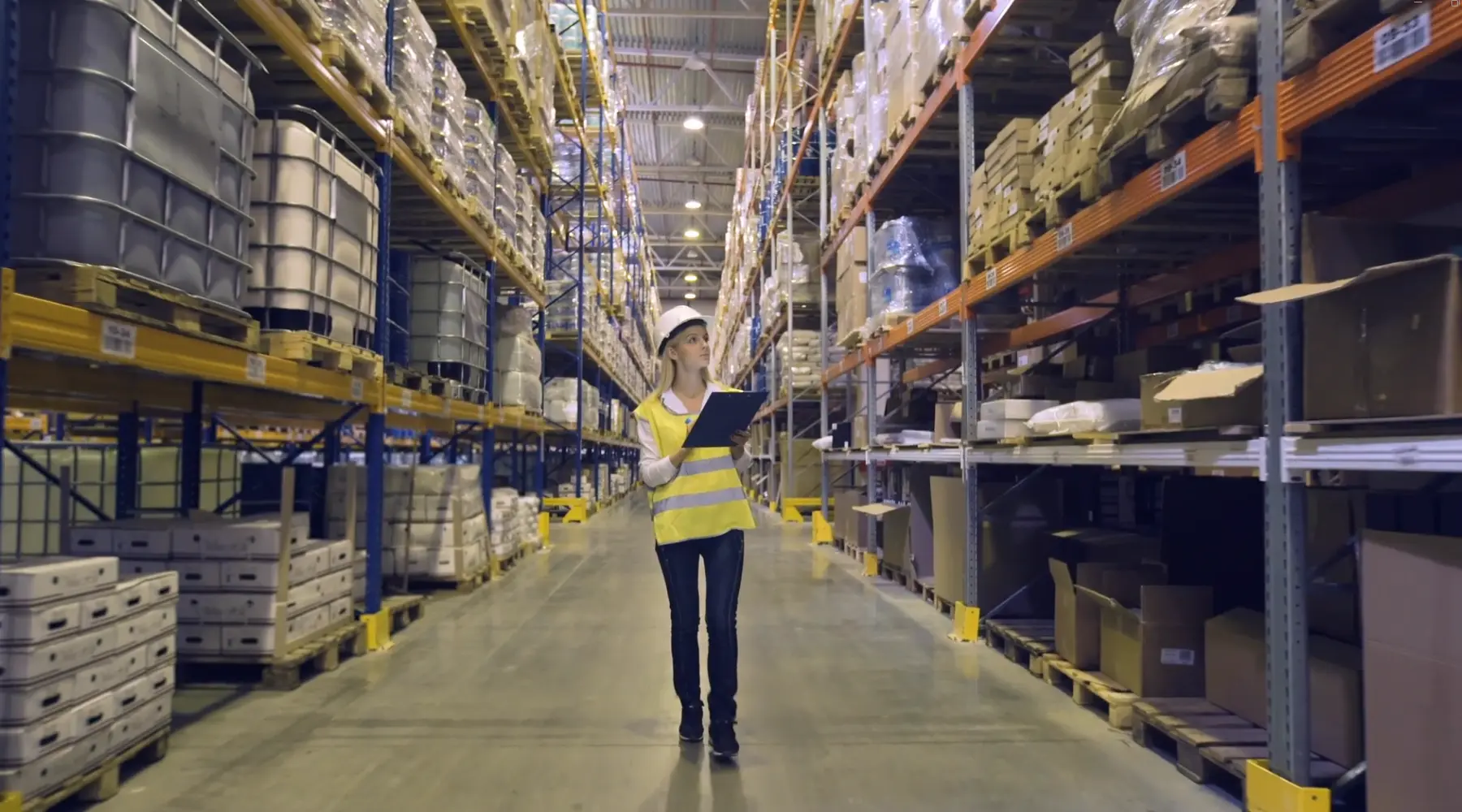
Benefits of RFID Pallet Tracking
RFID pallet tracking offers numerous advantages to businesses striving to improve their supply chain operations. Here are some of the key benefits:
Enhanced Inventory Visibility
One of the most significant advantages of RFID pallet tracking is its ability to provide real-time inventory visibility. Knowing where each pallet is at any given moment helps companies manage their stock more efficiently. This improved visibility reduces the chances of misplaced goods and facilitates accurate inventory management, leading to better decision-making.
Improved Efficiency and Reduced Labor Costs
Traditional inventory management systems often require manual barcode scanning and logging, which is time-consuming and prone to human errors. RFID automates the entire process, reducing the need for manual labor and increasing operational efficiency.
Workers no longer need to manually scan each pallet, which significantly cuts down on labor costs and speeds up warehouse operations.
Reduced Errors and Shrinkage
Manual processes often lead to errors, such as mislabeling, incorrect counts, or misplaced pallets. RFID pallet tracking minimizes these issues by automatically capturing accurate information about the pallet’s location and contents. This accuracy also helps in reducing shrinkage due to theft or loss, as the movement of pallets can be continuously tracked and recorded.
Faster Loading and Shipping
RFID readers can quickly scan multiple tags simultaneously without requiring direct line-of-sight. This capability speeds up the loading and shipping processes, as workers do not need to individually scan each pallet.
By reducing delays and ensuring that the right pallets are loaded onto the correct trucks, RFID pallet tracking improves the overall efficiency of outbound logistics.
Improved Traceability and Compliance
Traceability is a key requirement for many industries, especially in food and pharmaceuticals, where strict regulatory compliance is required. RFID pallet tracking allows companies to trace the movement of goods across the entire supply chain. This helps in adhering to compliance requirements and ensures that the origin, storage conditions, and transit information of each pallet are accurately recorded and accessible.
Conclusion
RFID pallet tracking is revolutionizing supply chain management by offering real-time visibility, improved efficiency, and data-driven insights. By reducing manual labor, minimizing errors, and enhancing traceability, RFID technology helps companies stay competitive in an increasingly fast-paced marketplace. Although challenges such as high initial costs and environmental interference exist, the long-term benefits of adopting RFID pallet tracking far outweigh the drawbacks.
As industries continue to evolve, RFID pallet tracking will play an essential role in enhancing supply chain efficiency and ensuring seamless, end-to-end management of goods. Investing in this technology now will not only improve current operations but also pave the way for a smarter, more connected future.
Interested in RFID?
An RFID tracking system can help organizations of all sizes improve their supply chain efficiency. Contact the CYBRA team to schedule a demo today.