RFID in Retail [Updated for 2025]
RFID adoption and usage continues to growth exponentially within the retail sector. Check out how retailers are finding value in RFID by improving inventory accuracy and minimizing supply chain issues.
Updated on 4/11/2025
RFID in Retail: What’s New in 2025
In 2025, RFID has firmly established itself as a critical component of modern retail operations. Once confined to stockrooms and logistics, RFID technology now extends across the entire retail ecosystem—from the supply chain to the sales floor and even the customer experience. Retailers are leveraging RFID for real-time inventory visibility across all store locations, which in turn enables faster restocking, precise order fulfillment (including BOPIS), and smarter shelf management.
With accuracy rates now exceeding 95%, many brands have phased out manual inventory counts entirely. Instead, they rely on passive RFID scans that occur automatically as products move through the store, ensuring continuous, hands-free inventory tracking.
Smarter Systems Through AI Integration
What sets RFID apart in 2025 is how it works in tandem with artificial intelligence and computer vision. Retailers are building predictive systems that not only detect low stock levels but also trigger automatic replenishment from nearby stores or warehouses. Some systems even guide floor associates directly to misplaced items, saving time and minimizing friction.
On the customer-facing side, RFID enhances the shopping experience through RFID-enabled fitting rooms and smart mirrors that suggest personalized recommendations and check sizing availability in real time. Mobile apps, connected to the RFID system, can now guide shoppers to the exact shelf location of an item—creating a seamless, self-service experience that improves satisfaction and drives conversions.
As a result, RFID is no longer seen as just a backend tool. It’s become a strategic asset, helping retailers deliver faster, smarter, and more personalized experiences across every touchpoint.
RFID in Retail Sees Rapid Growth
Since the start of 2022 major retailers have begun issuing RFID tag mandates. Target, Macy’s, Nordstrom, and Walmart have all handed down RFID mandates to their respective partners and vendors. So, why is RFID in retail seeing such a boon?
RFID has many uses for retailers. It can improve inventory visibility and reduce cycle count times by 96%. RFID-enabled inventory counts can be performed more than once a week. With this technology, retailers can learn more about their customers and products. For example, a company like Macy’s can use RFID to list products for sale only when there is only one left. This data can be invaluable in the event of a disaster in the retail industry.
With RFID, retailers see inventory accuracy raise from 63% to 95%. RFID improves labor productivity by 96%, reduces cycle count time by 96%, and cuts out-of-stocks by as much as 50%. (Source: GS1 US)
Accurate inventory information is crucial for efficient supply chains. Traditional inventory count methods require intensive labor and are often inaccurate. RFID has improved inventory accuracy significantly by processing a wide range of data in just a few minutes. It eliminates the need for manual scanning of barcodes on individual objects and eliminating the need for touch-counting every object. RFID is the future of inventory tracking. Its many uses in retail are only limited by the imagination of their users.
RFID has many other uses for retailers. It can help increase transparency on the sales floor. For example, RFID helps stores reduce labor costs. It reduces cycle count time and allows staff to focus on customer service. It can help reduce labor costs by automating reorders at safe-stock levels. Furthermore, retailers can use RFID technology to automate replenishment and inventory processes. This technology allows retailers to monitor stock levels more efficiently and increase productivity.
Table of Contents
- How Does RFID Work in Retail?
- What are some use cases of RFID in retail?
- What is an RFID tag Mandate?
- What are the advantages of RFID Tagging?
- What types of products can you use RFID for?
- How does RFID help in apparel inventory management?
- How does RFID help in replenishing proper stock levels at each store?
- How can business get started with RFID?
How Does RFID Work in Retail?
Retailers such as Macy’s, Target, Walmart, Kohls, Nordstrom and several more are currently relying on RFID technology to ensure end-to-end supply chain efficiency. But, how exactly do retailers use RFID? In some cases, retailers apply RFID tags to their merchandise at the item-level. This means that certain products have RFID directly affixed to themselves.
Retailers often affix RFID tags directly to the following kinds of inventory:
- Jewelry
- Handbags
- Makeup kits
- Luxury brand shoes
RFID is commonly deployed in retail supply chains to improve inventory accuracy. From initial inbound shipments all the way to final sale, retailers can track their goods thanks to RFID. This allows for optimal inventory visibility which makes modern retailing easier. With more accurate inventory, retailers can cater to popular shopping trends such as BOPIS (buy online, pickup in store).
Tagging Requirements
Major retailers may require vendors to tag their own goods and shipments as well. This is known as a RFID tag mandate. Retailers provide vendors with guidelines and expectations for tagging merchandise. Vendors and manufacturers will then be expected to adhere to the mandate. Failure to tag items according to the retailer’s mandate can often lead to financial penalties, chargebacks on merchandise, or a dissolution of the vendor/retailer partnership altogether.
To learn more about what exactly RFID is, read our glossary article.

Key Use Cases for RFID in Retail
RFID (Radio Frequency Identification) has become a game-changer in the retail industry, offering powerful tools to streamline operations, reduce losses, and elevate the customer experience. As retailers navigate the demands of omnichannel fulfillment, real-time visibility, and smarter merchandising, RFID proves its value across a wide range of use cases.
Simplified Cycle Counting
One of the most impactful applications of RFID in retail is cycle counting. Unlike traditional barcode scans, which require line-of-sight and manual effort, RFID allows for batch scanning, enabling store associates to count thousands of items in seconds. This means staff no longer need to close departments or perform overnight audits—inventory can be verified in real time, during normal business hours, with far greater speed and accuracy.
Enhanced Loss Prevention
RFID also plays a critical role in reducing shoplifting and inventory shrink. Retailers can receive alerts when tagged items are moved out of designated zones or exit the store without authorization. Since RFID tags can store detailed item data—such as SKU, color, and size—recovery efforts become more efficient. Paired with sensor-enabled exits, RFID provides a smarter, more proactive layer of theft deterrence.
Powering Omnichannel Fulfillment
With the rise of BOPIS (Buy Online, Pick Up In Store) and other hybrid fulfillment models, speed and accuracy are more important than ever. RFID gives retail teams real-time visibility into exact inventory locations, whether items are on the sales floor, in the stockroom, or in transit. This ensures faster fulfillment, fewer errors, and a better customer experience.
Improving In-store Traffic Patterns
Retailers can receive information from RFID that shows how shoppers move about their store. With this information, retailers can move items around to maximize sale probability. Other advantages include reducing cart/item abandonment, and reviewing traffic movement based on day and time.
RFID Can Speed Up Checkout Process
With RFID, retailers can make their checkout process more frictionless than ever before. With the right combination of RFID tags and sensors, shoppers can simply grab the items they need and walk out without waiting in line or checking out. Amazon Go, a pioneer of such technology, allows their customers a seamless customer experience that improves the shopping experience.
These use cases demonstrate the versatility and value of RFID technology in the retail industry, enabling retailers to enhance efficiency, improve customer experiences, and gain valuable insights into their operations.
As RFID technology continues to evolve, its applications in retail are expected to expand, further revolutionizing the retail landscape.
What is an RFID Tag Mandate?
When a retailer has decided to deploy RFID into their supply chain, they will need to notify its vendors and manufacturing partners. Most major retailers source merchandise from hundreds of brands and suppliers. In order to ensure consistency through their supply chain, the retailer will announce how and when they expect their suppliers to add RFID tags to their merchandise.
Current RFID Mandates
In just the last few years the following retailers have rolled RFID mandates for vendors:
There are numerous moving parts and fine details that go into a RFID mandate. Some mandates may require vendors to tag goods at the item level. This is typically reserved for high value items such as designer bags and jewelry. For consumer goods and apparel, it is generally expected that retail vendors and suppliers tag goods via shipped pallets and bulk packages. Once these pallets or packages are tagged, suppliers can send them to their retail partner for inbound reception.
Retailer Expectations
Retailers will likely have a system set up where shipments are reviewed and tags automatically scanned as they enter their facility. If merchandise is not tagged to the specifications of the retailer’s mandate, the supplier may get penalized or even have their entire order nullified. This is known as a chargeback, and it can cost suppliers and distributors millions of dollars. This is why it is absolutely vital for a retail vendor to make sure their RFID tagging operations are in compliance with its retailers.
These mandates are not just for high value items. As recently as 2025, Walmart has been continued to roll out their RFID mandate to a wide variety of retail products including housewares, hardware, and even crayons.
What Are the Advantages of RFID Tagging in Retail?
RFID tags are often compared to barcodes since the tags will replace barcode scanning during inventory counting and inbound/outbound shipping and receiving. When comparing RFID to barcodes, RFID offers several major advantages for both retailers and suppliers.
RFID Tagging Advantages
- Faster Item Counting – In a matter of seconds, entire sections of RFID tagged inventory can be scanned. This is far more efficient and accurate than having to scan barcodes one at a time.
- Larger Data Storage – Standard 1D barcodes can store 85 characters. RFID tags on the other hand can store much more data. Alien’s Higgs 3 chip, for example, has a memory of 512 bits.
- Durability – Barcodes have a tendency to disintegrate or peel off depending on how they are created and handled. RFID tags on the other hand can be ruggedized in order to handle harsh environments.
What types of products can you use RFID for?
RFID tags are typically applied on shipping pallets or bulk packages. However, there may be a sensible reason to tag individual items such as luxury .goods or high value inventory. As long as the goods are stored in an area where they can be scanned, there aren’t many limitations as to what kinds of products you can tag with RFID.
In retail, equipment may be affixed with RFID tags. The versatility and flexibility of RFID tags make them suitable for various types of products, enabling efficient tracking, inventory management, and enhanced customer experiences. Some of the products that can benefit from RFID in retail include:
Apparel and Fashion
RFID tags can be discreetly embedded in clothing, shoes, and fashion accessories. This allows retailers to track individual items accurately, and manage inventory levels.
Consumer Electronics
RFID tags are used in electronics to track high-value items such as laptops and smartphones throughout the supply chain. This helps reduce theft and enhances stock accuracy.
Beauty Products
RFID can be employed in beauty and cosmetics items like makeup, skincare products, and fragrances. It aids in inventory control and ensures that shelves are well-stocked to meet customer demands.
Pharmaceuticals
RFID tags are utilized in the pharmaceutical industry to track and goods, ensuring better visibility and traceability. This helps prevent counterfeiting and improves inventory control.
Home and Garden
RFID technology can be applied to various home and garden products, such as home appliances, gardening tools, and home improvement items – enabling efficient stock management.
Toys and Games
RFID tags can be integrated into toys and games, offering features like interactive experiences or age-appropriate product recommendations. They also help retailers monitor inventory levels and optimize restocking processes.
Sporting Goods
RFID can be used in sporting goods, including equipment and apparel. It facilitates inventory tracking, helps manage rental items, and improves product availability.
Jewelry and Luxury
RFID tags can be discreetly incorporated into high-end jewelry and luxury items. They serve as anti-theft devices and offer product authentication, ensuring customers receive genuine products.
Pet Products
RFID can be used in pet-related items such as pet food, collars, and accessories, providing retailers with better control over stock levels and product information.
These examples demonstrate the broad applicability of RFID technology in the retail industry, ranging from fashion and electronics to groceries and luxury goods. RFID’s ability to enhance inventory management, improve security, and provide personalized customer experiences makes it a valuable asset for retailers across various product categories.
With that said, RFID tags can struggle to read effectively when they are affixed to liquid materials such as liquor bottles or metals. This is because liquid and metals reflect radio waves, thus making it very hard for the tags to be read.
How RFID Improves Apparel Inventory Management
RFID and apparel make an ideal match for several compelling reasons—most importantly, accuracy. In today’s fast-moving omnichannel retail environment, maintaining accurate inventory data is not just helpful; it’s essential. Retailers rely on real-time inventory visibility to fulfill orders, replenish stock, and keep customers satisfied across both online and in-store channels.
By implementing RFID, store associates can rapidly scan entire racks or backroom shelves using handheld readers, generating accurate inventory counts in a matter of seconds. This speed and precision enable retailers to identify low stock levels early and take timely action to reorder, significantly reducing the risk of out-of-stock items.
As a result, RFID doesn’t just support better inventory management—it directly improves product availability and sales performance.
RFID for High-Value Apparel and Hard-to-Find Items
Beyond basic inventory tracking, RFID is also a powerful tool for loss prevention—especially when it comes to higher-value apparel. Once items are tagged, RFID readers can detect unauthorized movement in real time, alerting staff or loss prevention teams immediately. This proactive approach allows retailers to minimize shrink and better protect their merchandise.
Moreover, RFID proves especially useful in retail environments where locating specific inventory can be time-consuming or challenging. For example, in wedding dress boutiques, where items are often large, delicate, and uniquely cataloged, RFID technology offers a simple solution. Using a reader equipped with geiger counter functionality, employees can quickly zero in on the exact location of a specific dress. Even more impressively, RFID software can display real-time item locations on a digital floor map, helping staff retrieve high-value garments faster and with less disruption.
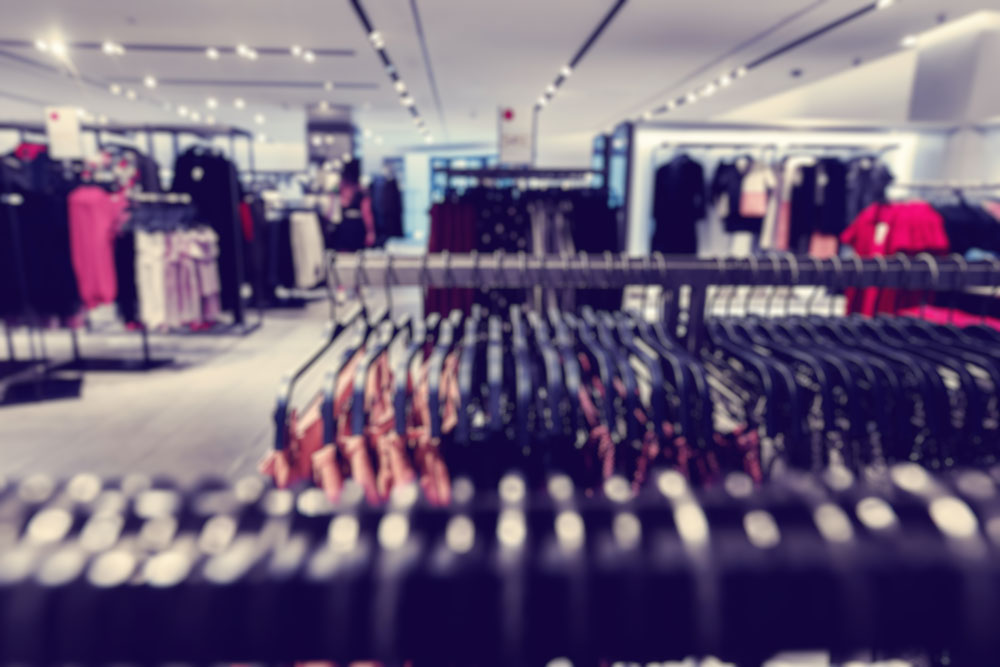
How does RFID help in replenishing proper stock levels at each store?
As we’ve discussed, maintaining accurate inventory numbers is a hugely important element to succeeding in the world of ecommerce. There are numerous ways RFID can help retailers manage inventory stock levels. RFID antennas can be carefully placed along shipping dock doors in order to ensure inventory is accurately accounted for as soon as it reaches the retail store. With this strategy, RFID can help retailers set their inventory accuracy levels to nearly 100% as soon as items enter the facility.
When items are brought to the shopping floor, employees can simply scan the goods in a batch to verify inventory counts. RFID software systems can alert managers when inventory is running low to avoid out-of-stock items.
How can businesses get started with RFID?
Retailers usually start with a RFID project or pilot test. Early on there is a lot of work and logistics that need to be squared away well before RFID is introduced into a retailers supply chain. The environment, required solutions, and overall expectations all play a role in how RFID will be utilized.
Organizations will then need to select their hardware and software. The hardware (RFID tags, antennas, readers, printers, etc.) will depend on the scope of the project. The software will depend on what you want to get out of your RFID investment. Some organizations may just want to run occasional cycle counts and receive basic inventory reports.
Contact your retail partners
On the other hand, some retailers may want a more robust tracking system to prevent theft or lost items. Regardless of the software you choose, the product should allow you to adequately track inventory, locate items, and update inventory data. That’s why it’s important to get in touch with your retail partners so there is little to no confusion.
Once a cost prohibitive solution, RFID is a lot more affordable than ever before. And, organizations can start small. An initial RFID project can be done in a single stock room or department. Even a small RFID pilot can yield higher inventory numbers, improved employee efficiency, and a reduction in lost inventory.
Interested in RFID?
An RFID tracking system can help organizations of all sizes improve their supply chain efficiency. Contact the CYBRA team to schedule a demo today.