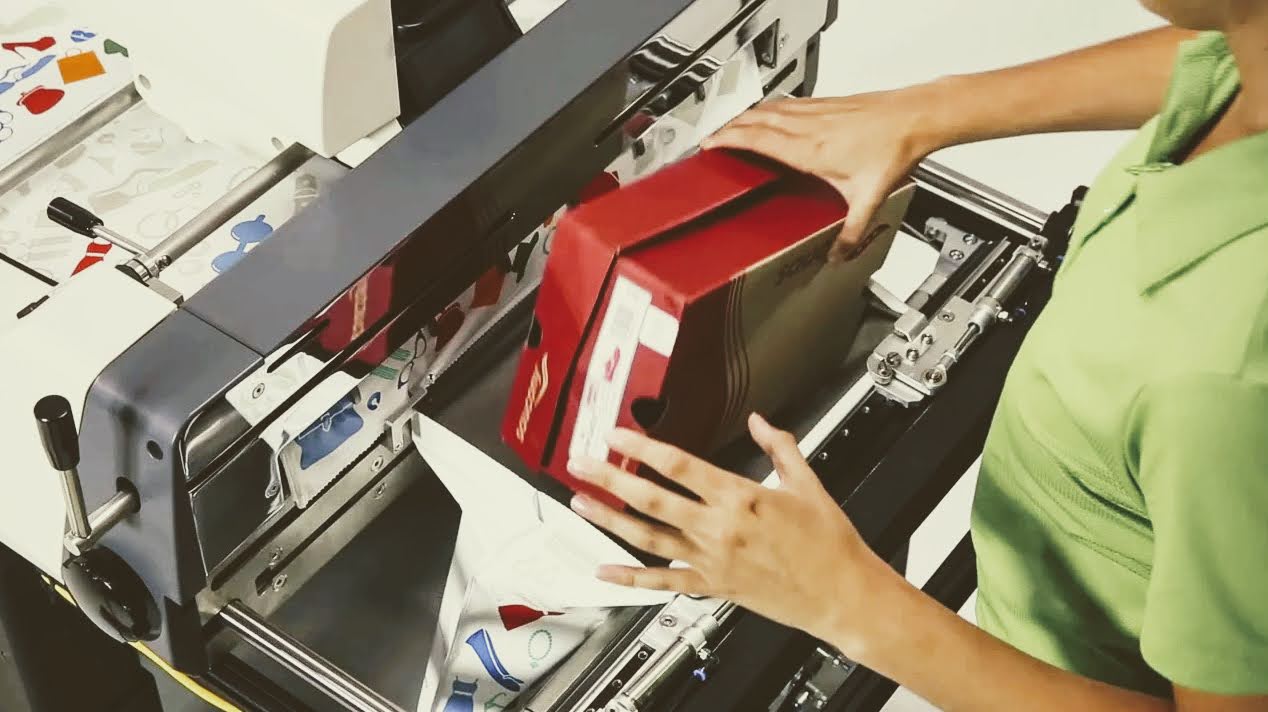
Investing in Automated Packaging Systems
Having automated packaging systems in your business can provide a number of benefits. These benefits include increased production speed, reduced labor costs, and increased product throughput. These benefits can make your products safe, appealing, and cost-effective.
Automation increases product throughput
Investing in automation has a number of potential economic benefits, including higher throughput, lower labor costs, and increased quality. It can help to improve safety records and reduce human error. Automation can also help to streamline day-to-day work. It can improve the work environment and allow employees to focus on critical matters.
The pace at which automation occurs will vary based on supply and demand dynamics, wage rates, and technical progress. It is also affected by regulatory acceptance and organizational processes.
The cost of technology and integration are also key factors. For example, in manufacturing, automated systems can improve quality and streamline day-to-day work. Robotic automation is a common way to increase production throughput. Similarly, automated driving of cars and trucks can reduce labor costs.
Automation has the potential to improve the productivity of companies, and create new jobs. However, it is important to note that not everyone will benefit from automation. Those who lose their jobs will find it difficult to find new employment. Similarly, those who gain employment will need to develop new skills and adapt to the new work environment.
Automation is a global phenomenon. It has the potential to impact the economies of all countries. Countries with advanced economies will likely adopt automation ahead of those with emerging economies.
The business case for automation is dependent on the type of industry and the level of capital intensity. It is also affected by the sector mix. Industries with heavy safety regulations, for example, may need to wait longer to see the benefits of automation.
Reduces labor costs
Investing in automated packaging systems can save manufacturers a significant amount of money. Compared to manual packaging, these systems require minimal labor and can be set up to run at high production speeds. By improving product quality and consistency, they can also increase profitability.
The use of automated packaging systems can also improve worker productivity. Automated machines can handle tasks like pallet wrapping, pallet strapping, and carton sealing. They also track production cycles and preventative maintenance schedules. These processes also reduce downtime due to employee absences.
Automated packaging can also free workers from repetitive tasks and reduce the risk of employee injury. Additionally, the system can increase productivity by allowing workers to be put in positions that are more profitable. The equipment may also allow for capacity expansion.
Automated packaging systems can also reduce overhead expenses. By improving productivity, they can help keep costs down during peak seasons. These systems also enable companies to recapture lost dollars.
Automated packaging equipment can also decrease shipping costs. Because the packaging process involves fewer product touches, there is less damage to the product. This reduces the need for more materials to protect products. Compared to manual packaging, automated systems are more consistent, and they make fewer mistakes.
The use of cohesive materials can also reduce costs. Cohesive materials can be used to wrap and seal packages, as well as for other purposes. They can also be used in conjunction with automated cohesive equipment.
Makes your products cost-effective, safe and appealing
Using automated packaging systems can help improve production, increase safety and enhance efficiency. Automated packaging systems can help prevent back injuries. In addition, they can make your products cost effective and appealing.
Aside from the obvious advantages, automated packaging systems also boast of some cool tech. One example is the micro chipped soft drink container. These miniature computers allow the bottle to be read by an RFID chip. Another is the ability to create custom packaging solutions. In addition, automated packaging systems can help create a buffer period before the package leaves the facility. These innovations ensure that the end product is a safe and secure one.
Another cool technological advance is the PLC system that is used to control the automatic packaging machines. The technology is able to improve the accuracy and speed of the machine, and help keep costs down in the process. In addition, the technology is able to handle many different products at the same time, and even accommodate products with different attributes.
The best automated packaging systems have been able to make many of the industry’s leading manufacturers more efficient. This includes Coca-Cola and the University of Reading. They have been able to develop micro chipped soft drink containers to allow for direct billing of these beverages. In addition, automated packaging systems can also provide pre-assembly spaces for packaging. These spaces can be used to improve the quality of the packaging.
Increases production speed
Whether you’re running a small business or a major corporation, automated packaging systems can boost your production speed. This can free up employees to focus on higher-value tasks, which improves productivity and increases profitability. It also allows you to achieve economies of scale. This can increase your revenue and provide a better customer experience.
Automated packaging systems increase production speed by minimizing human input and waste. They also reduce the number of errors and product faults. This reduces the risk of injuries to workers.
The automated packaging process also provides consistency and reliability. With the right equipment, you can perform multiple packaging tasks at the same time. You can even label a product in one step. The result is consistent packaging that increases productivity.
Automation also reduces labor costs. In addition, it reduces the risks of repetitive tasks and injuries. These repetitive tasks can lead to musculoskeletal disorders and ergonomic injuries. In some cases, they can take weeks to heal.
Automated packaging systems also improve quality control measures. Input devices collect data from conveying equipment and send it to a Programmable Logic Controller (PLC), which makes decisions about packing orders. The PLC then converts the electric signals into actionable steps. These steps are then sent to output devices, which move products through the automated packaging system.
Automated packaging systems also provide longer productive labor hours. The more you can automate, the more money you can save on labor costs. Adding robotics to your manufacturing line can also improve worker safety.
Multitasks
Using automation in packaging lines can improve quality control, reduce ergonomic injury risk, and increase productivity. It can also help improve employee efficiency and reduce costs.
Automated packaging systems allow workers to operate packaging lines remotely. This frees up workers to do higher-level tasks. It can also increase speed and improve product throughput. It also reduces the number of employees present on the production floor.
Automation can also help decrease the risk of repetitive work injuries and stress injuries. It can also reduce repetitive work tediousness and increase productivity. It can also reduce the number of errors in the packaging process. This increases consistency and improves brand recognition.
One of the most common ways to automate a packaging line is to use a pick and place robot. These robots can pick and place a product, increasing speed and consistency.
Another way to automate packaging lines is to multitask multiple steps in the packaging process. This frees up workers to do higher-level task and improves efficiency.
In simple multitasking systems, cooperative scheduling is used. This allows tasks to run at the right time. It also allows tasks to run in parallel.
If your system involves a lot of repetitive work, you should consider process automation. These systems can replace workers in repetitive motions and can eliminate errors in the packaging process. Using an automated system can also help increase your productivity and reduce the number of errors in the packaging process.
Payback calculator
Using an automated packaging system can increase your productivity, save you money, reduce defects, and improve product quality. But deciding whether or not to automate your packaging process comes down to a cost-benefit analysis.
A payback calculator for automated packaging systems is a great way to estimate the benefits of investing in an automated packaging machine. However, it’s important to understand that a payback calculator for automated packaging systems isn’t exactly as simple as it sounds.
To calculate the payback of an automated packaging system, you’ll need to know the cost of the equipment, how much money you’ll save, how much time you’ll save, and how much money you’ll make. To get an idea of how much you could save, you can take a look at the calculators available from many manufacturers. Alternatively, you can perform a more sophisticated analysis using industry-specific data from the Center for Automotive Research, the Center for Automotive Research, the Center for Packaging Technology, or the Center for Automotive Research.
The simplest way to calculate the payback of an automated packaging system is to estimate the number of packages you produce each year. This is done by multiplying your throughput specifications (typically in bags per minute or cartons per minute) by the number of days you operate each year, and the number of hours you package per day. Using this information, you can estimate how many packages you’ll produce per hour, which can give you an idea of how much more productivity you’ll experience.
Integrate with Your Label Management Software
Now that you’ve decided to make the investment into an automated packaging system, you’ll need to integrate the system with your current labeling operations.