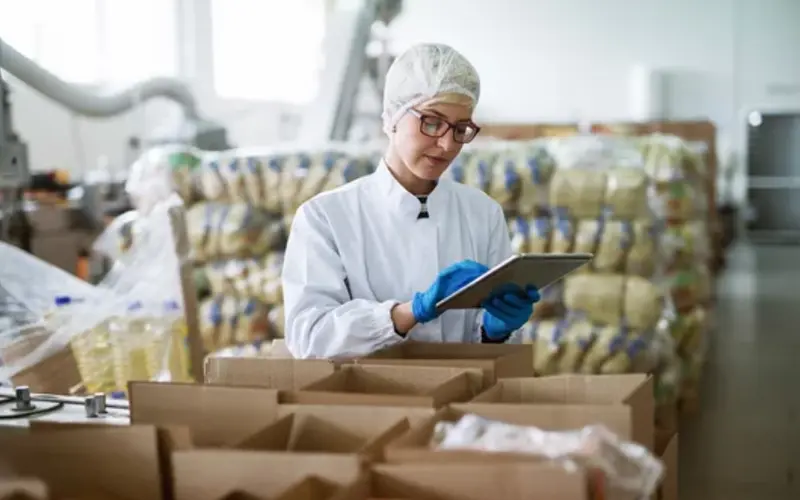
For organizations in food and beverage manufacturing, food waste in their supply chains is incredibly costly. According to a report by McKinsey & Company, estimated $600 billion worth of food is lost globally during or just after harvest. For these organizations, identifying solutions that can curtail such is of the utmost importance
One method gaining prominence in reducing industrial food waste is the integration of RFID technology with the First Expired, First Out (FEFO) inventory management principle. This combination offers a powerful solution to manage perishable food materials, ensuring items are used in the order they are due to expire throughout the manufacturing process.
What is FEFO?
FEFO (First Expired, First Out) is an inventory management principle used primarily for perishable goods. It ensures that products with the earliest expiration dates are used or sold first, reducing waste and ensuring freshness. FEFO is particularly crucial in industries like food and beverage, pharmaceuticals, and cosmetics, where product shelf life is a key concern.
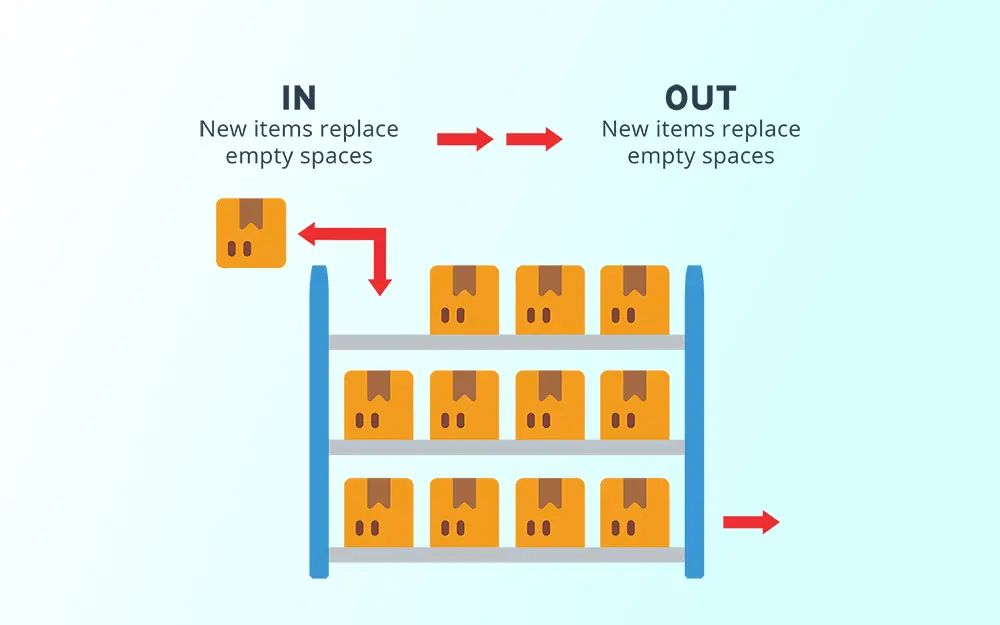
Understanding RFID Technology
RFID, or Radio Frequency Identification, is a technology that uses electromagnetic fields to automatically identify and track tags attached to objects. These tags contain electronically stored information, such as a unique identifier and other relevant data. An RFID system consists of three main components:
- RFID Tags: Small devices containing a microchip and an antenna. These tags come in two types: passive (no internal power source, powered by the reader’s signal) and active (powered by an internal battery).
- RFID Readers: Devices that emit radio waves and receive signals from RFID tags. Readers can be fixed or handheld and vary in range and capabilities.
- Inventory Management System: A software platform that integrates with RFID readers to collect, process, and manage data from the tags.
How RFID Enhances FEFO Inventory Management
Integrating RFID technology with the FEFO principle brings significant advantages. Here’s how RFID works with FEFO to streamline inventory management:
1. Tagging and Data Encoding
When new products arrive at a warehouse or storage facility, each item is tagged with an RFID label. This label includes a unique identifier and critical data, such as the expiration date. The tagging process can be automated or done manually, depending on the scale and resources of the business. Once tagged, these items are ready to be tracked and managed using RFID technology.
2. Automated Data Collection
RFID readers placed at strategic points within the facility automatically scan the tags as items move through the supply chain. These readers can be positioned at entry and exit points, storage areas, and along conveyor belts. The readers capture the unique identifier and expiration date from each tag and send this data to the inventory management system in real-time.
3. Real-Time Inventory Management
The real-time data collected by RFID readers is processed by the inventory management system, which continuously updates the database. This system provides an accurate and up-to-date view of inventory levels, locations, and expiration dates. With this information, businesses can efficiently manage stock, ensuring that items are used or shipped according to their expiration dates.
4. Prioritizing Expired Products
The core benefit of integrating RFID with FEFO is the ability to prioritize items based on their expiration dates. The inventory management system uses the expiration date data from RFID tags to organize products accordingly. When fulfilling orders or restocking shelves, the system ensures that items with the nearest expiration dates are picked first. This automated process reduces the risk of human error and ensures compliance with FEFO principles.
5. Proactive Alerts and Automation
An advanced inventory management system can generate proactive alerts based on RFID data. For example, it can notify staff when items are nearing their expiration dates, prompting timely action such as discounts, promotions, or donations to prevent waste. Additionally, the system can automate reordering processes, ensuring that stock levels are maintained and that new items are received and tagged promptly.
Benefits of RFID and FEFO Integration
The integration of RFID technology with the FEFO principle offers several key benefits:
1. Reduced Waste
By ensuring that items with the earliest expiration dates are used first, businesses can significantly reduce waste. This is particularly important for perishable goods, where expired products can lead to financial losses and environmental concerns.
2. Improved Efficiency
RFID automates data collection and inventory management processes, reducing the need for manual labor. This leads to faster and more accurate stock management, freeing up staff to focus on other critical tasks.
3. Enhanced Accuracy
Manual inventory management is prone to errors, which can result in stock discrepancies and inefficiencies. RFID technology provides precise and reliable data, ensuring that inventory records are always accurate.
4. Better Inventory Control
Real-time tracking and monitoring enable businesses to maintain optimal stock levels. This prevents overstocking and understocking, ensuring that products are available when needed without tying up excessive capital in inventory.
5. Compliance and Traceability
In industries like pharmaceuticals and food, regulatory compliance and traceability are essential. RFID technology provides a comprehensive audit trail, making it easier to comply with regulations and track the movement of products throughout the supply chain.
FEFO + RFID Challenges and Considerations
While the integration of RFID and FEFO offers numerous benefits, there are challenges and considerations to keep in mind:
1. Initial Investment
Implementing an RFID system requires an initial investment in tags, readers, and software. However, the long-term benefits often outweigh the upfront costs.
2. Integration with Existing Systems
Integrating RFID technology with existing inventory management systems can be complex. Businesses need to ensure compatibility and seamless data flow between systems.
3. Environmental Factors
RFID performance can be affected by environmental factors such as metal and liquids, which can interfere with radio waves. Proper planning and placement of readers are essential to mitigate these issues.
Conclusion
RFID technology, when integrated with the FEFO inventory management principle, offers a powerful solution for managing perishable goods. It enhances accuracy, efficiency, and waste reduction, providing businesses with a competitive edge in today’s dynamic supply chain environment.
Despite the challenges, the benefits of RFID and FEFO integration make it a worthwhile investment for businesses looking to optimize their inventory management processes. As technology continues to advance, the capabilities of RFID systems will only improve, further revolutionizing the way we manage and utilize inventory.
Interested in RFID?
An RFID tracking system can help organizations of all sizes improve their supply chain efficiency. Contact the CYBRA team schedule a demo today.