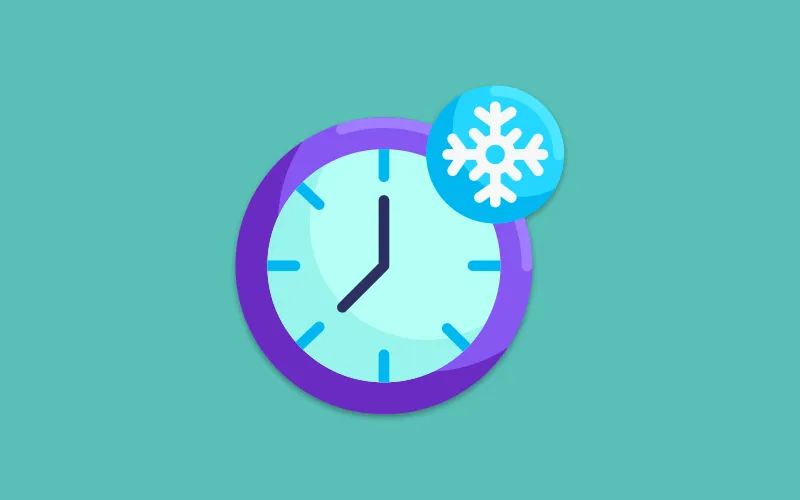
Cold chain technology plays a vital role in preserving the quality and safety of perishable goods, ensuring they reach consumers in optimal condition. According to the World Health Organization, approximately 25% of vaccines are wasted globally due to temperature control issues in the cold chain. This statistic underscores the critical importance of maintaining proper temperature conditions throughout the supply chain.
One of the key advancements revolutionizing cold chain management is the integration of RFID technology for cold tracking. In this article, we delve into the significance of cold chain technology, explore the role of RFID in inventory tracking, and discuss its benefits in ensuring the integrity of cold-sensitive products.
Understanding Cold Chain Technology
The cold chain refers to the process of transporting and storing temperature-sensitive products within a specific temperature range, typically between 2°C to 8°C for perishable goods like pharmaceuticals, vaccines, and food items. Maintaining these stringent temperature conditions is crucial to prevent spoilage, maintain product efficacy, and ensure consumer safety.
Examples of Cold Chain Tracking and Technology
Cold chain logistics involve a series of interconnected activities, including refrigerated transportation, storage facilities, and monitoring systems, all designed to preserve product quality from production to consumption.
- Transporting and storing vaccines, insulin, and other temperature-sensitive medications.
- Preserving the freshness and quality of perishable foods like meat, dairy, and produce.
- Extending the shelf life of harvested fruits and vegetables.
- Transporting blood products, organs, and tissues for transplants.
- Preserving the quality of temperature-sensitive cosmetics and personal care products.
- Ensuring the quality of fresh and frozen goods in online grocery deliveries.
- Storing and transporting cell cultures, tissues, and biological samples.
- Distributing vaccines to remote and underserved areas.
- Managing the temperature-sensitive logistics of investigational drugs.
- Preserving the stability of temperature-sensitive chemicals and reagents.
Challenges in Cold Tracking and Cold Chain Management
Despite technological advancements, managing the cold chain presents several challenges. Temperature excursions, which occur when products are exposed to temperatures outside the recommended range, pose a significant risk to product integrity. Factors such as equipment malfunction, improper handling, and unforeseen delays during transportation can lead to temperature fluctuations, potentially compromising the quality and safety of perishable goods.
Additionally, manual monitoring and tracking methods are often time-consuming, error-prone, and lack real-time visibility into inventory status.
RFID in Cold Chain Tracking
RFID technology offers a solution to the limitations of traditional tracking methods by enabling automated, real-time monitoring of inventory throughout the cold chain. RFID systems consist of tags attached to individual products or packaging, readers placed at key checkpoints, and a centralized database for data management. These tags contain electronically stored information that can be wirelessly transmitted to readers, allowing for seamless tracking and traceability of products at every stage of the supply chain.
Benefits of RFID in Cold Chain Management
- Enhanced Visibility and Traceability: RFID enables granular visibility into the movement of products, from manufacturing facilities to distribution centers to retail outlets. With RFID tags, stakeholders can accurately track the location, temperature, and condition of each item in real time, facilitating proactive decision-making and response to potential issues.
- Improved Inventory Management: Cold tracking with RFID streamlines inventory management processes by providing accurate, up-to-date information on stock levels and expiration dates. This visibility helps prevent stockouts, reduce excess inventory, and minimize waste, ultimately optimizing supply chain efficiency and reducing costs.
- Increased Compliance and Quality Assurance: RFID technology supports compliance with regulatory requirements and quality standards by providing auditable records of temperature conditions throughout the cold chain. This documentation is invaluable for demonstrating adherence to Good Distribution Practices (GDP) and ensuring product integrity during audits and inspections.
- Quick Detection of Anomalies: RFID-enabled temperature monitoring systems can automatically alert stakeholders to temperature deviations or other anomalies in real time. This early warning system allows for prompt intervention to mitigate risks and prevent potential product losses, preserving the quality and efficacy of cold-sensitive goods.
- Seamless Integration with Existing Systems: RFID technology is highly versatile and can be seamlessly integrated with existing cold chain infrastructure and enterprise systems. Whether deployed alongside temperature-controlled vehicles, storage facilities, or supply chain management software, RFID solutions complement existing processes without disruption.
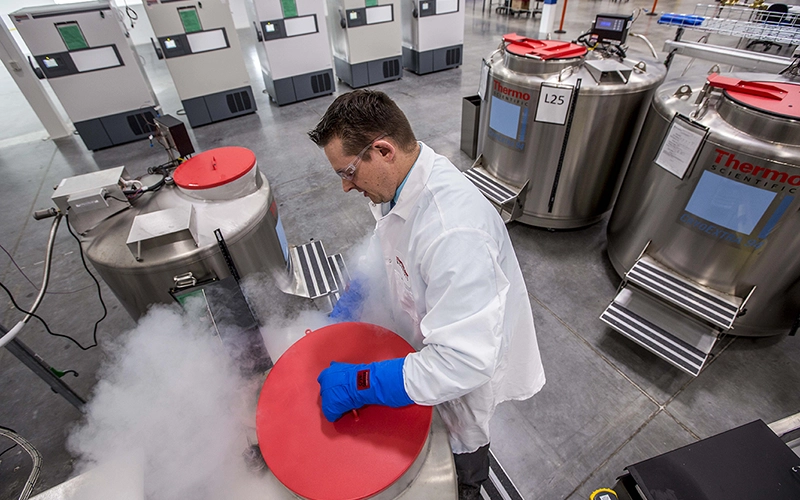
Case Study: Thermo Fisher Cold Tracks Animal Serum with RFID
Several organizations across industries have successfully implemented RFID-based cold tracking solutions to enhance their cold chain operations.
For instance, biotechnology companies, such as Thermo Fisher, leverage RFID technology to monitor the temperature-sensitive distribution of materials, ensuring compliance with regulatory requirements and safeguarding patient safety.
Getting Started with RFID in Your Cold Chain
Cold chain technology, powered by RFID innovation, continues to transform the landscape of temperature-controlled logistics, offering unprecedented visibility, efficiency, and reliability.
By leveraging RFID for cold tracking, organizations can mitigate risks, improve inventory management, and uphold the quality and safety of perishable goods throughout the supply chain.
As the demand for cold chain solutions grows, embracing RFID technology represents a strategic investment in ensuring the integrity and viability of cold-sensitive products in an increasingly interconnected world.
Interested in RFID?
An RFID tracking system can help organizations of all sizes improve their supply chain efficiency. Contact the CYBRA team schedule a demo today.