O’Neill Logistics Unlocks High-Speed Accuracy with the CYBRA Cage RFID Tunnel Technology
Facing rising order volumes and manufacturing and packaging accuracy concerns, O’Neill Logistics turned to RFID technology to streamline outbound validation and provide 100% order picking accuracy, reducing retailer charge backs.
In today’s high-speed fulfillment environment, accuracy isn’t a luxury — it’s a requirement. For third-party logistics providers (3PLs), the pressure to get orders right the first time is especially intense. One incorrect shipment can lead to costly chargebacks, lost client trust, and operational slowdowns.
In fact, each picking error can result in significant chargeback penalties equivalent to 5% of the transaction price.
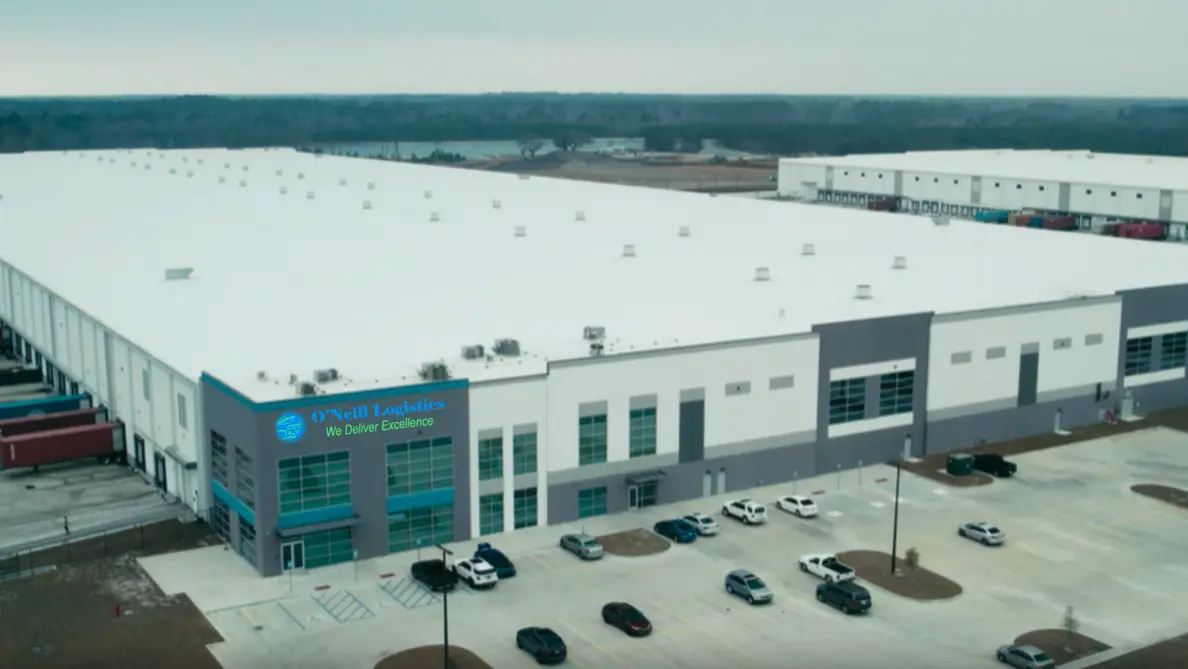
O’Neill Logistics’ one million square foot warehouse in Bloomingdale, GA
The Customer
O’Neill Logistics
O’Neill Logistics is a full-service 3PL specializing in pick and pack fulfillment for fashion and apparel brands. From garments and intimate wear to denim and accessories, they handle thousands of cartons daily across three strategically located distribution centers. Their clients ship to big box retailers with tight compliance requirements, meaning accuracy and speed are non-negotiable.
Founded in 2012 as a family-owned business in New Jersey, O’Neill Logistics has grown into a nationwide 3PL provider with operations spanning New Jersey, Southern California, and Savannah, Georgia.
Today, the company operates over 2 million square feet of omni-channel distribution space, including a newly launched, state-of-the-art 1 million square foot facility in Bloomingdale, GA.
Known for flexibility, high-touch service, and efficiency, O’Neill Logistics prides itself on helping brands scale without sacrificing quality or control.
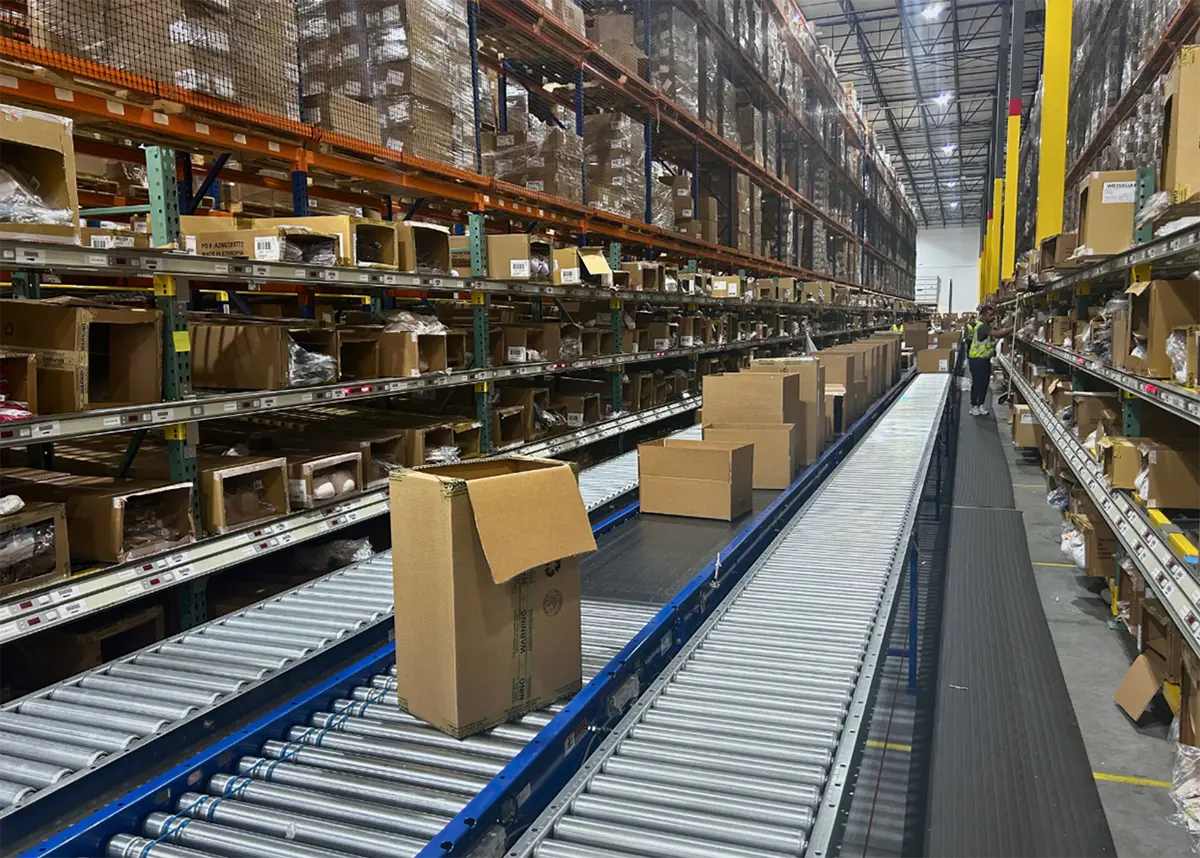
The Challenge
Outbound Accuracy Under Pressure
As O’Neill Logistics scaled operations across multiple facilities, one issue kept surfacing: outbound unit order accuracy. Despite robust pick and pack systems and processes, incorrect items were still making it into cartons.
The core of the issue was caused by external factors, with majority of errors stemming from upstream manufacturing errors — incorrect contents or mislabeled goods arriving from manufacturers. Still, once the cartons left O’Neill’s facilities, the responsibility landed on their shoulders. O’Neill began extensive AQL audits, and the result indicated production packaging errors. O’Neill deployed RFID technology as a scalable solution to manual labor-intense physical audits. The result was 100% accuracy, elimination of chargebacks and more accurate POS sell-throughs, while strengthening its relationships.
The Solution
RFID Tunnel Technology for Seamless Carton Validation
O’Neill Logistics partnered with CYBRA to implement RFID tunnel systems at their facilities in New Jersey, Georgia, and California.
The goal: automate the verification of carton contents without disrupting throughput or increasing labor.
Unlike traditional barcode scanning — which requires workers to scan each item individually — RFID tunnels allow cartons to be scanned in motion. As a carton passes through the tunnel, the system automatically reads all the RFID tags inside and compares the scanned items against the order data. If the contents are correct, the carton moves on. If not, the system flags the issue for review — no manual scanning required.
This solution dramatically reduced the steps involved in validating orders. Instead of relying on visual checks and barcode guns, warehouse staff can now verify every carton in seconds, with minimal handling and maximum accuracy.
Even better, the RFID tunnel integrates seamlessly with O’Neill’s existing system, Synapse by Made4Net, creating a hands-free quality control checkpoint that doesn’t add friction to the fulfillment process. This allows them to introduce carton-level audits after pick and pack, without increasing labor costs or delaying shipments.
The result is a faster, smarter, and more scalable way to ensure outbound accuracy — giving both O’Neill and their clients greater confidence in every shipment.
%
Since rolling out CYBRA’s RFID tunnel technology, O’Neill Logistics has a 100% outbound unit pick order accuracy.
The Results
Accuracy, Efficiency, and Peace of Mind
Since rolling out CYBRA’s RFID tunnel technology, O’Neill Logistics has a 100% outbound unit pick order accuracy — and a significant reduction in manual touchpoints during the fulfillment process.
The RFID tunnels now serve as an automated safety net, verifying the contents of thousands of cartons per day across multiple locations. This added layer of validation has allowed O’Neill to:
- Improve outbound accuracy and reduce costly shipping errors
- Minimize labor requirements by replacing manual barcode scans with automated reads
- Respond faster to client concerns with detailed, carton-level validation data
- Deliver higher service levels to major retail customers with strict compliance expectations
With RFID tunnels in place, O’Neill can confidently move high volumes of apparel — from garments and intimate wear to jeans and accessories — while meeting their clients’ growing demands for speed and precision.
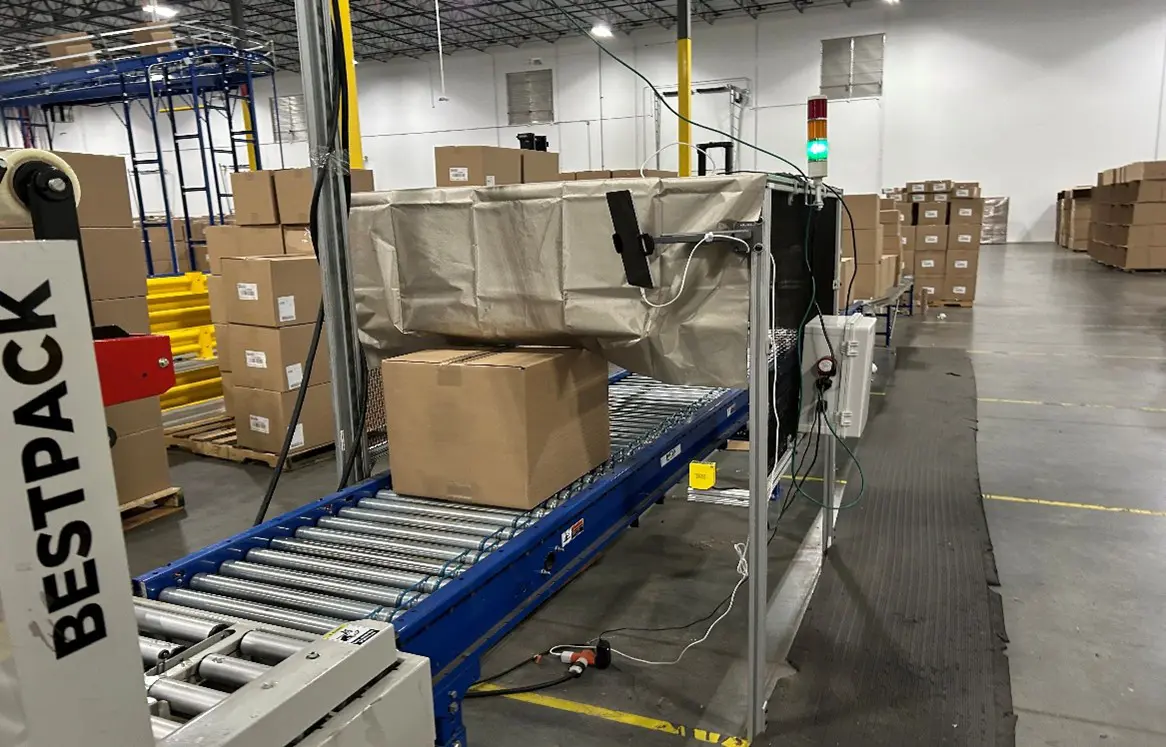
Looking Ahead
A Smarter, Scalable Future
The success of RFID at O’Neill’s current facilities has opened the door to future innovation. With plans to build on the RFID infrastructure already in place, the company is exploring additional use cases — from inbound validation and returns processing to more advanced carton auditing and inventory tracking.
By investing in RFID early and strategically, O’Neill Logistics is positioning itself as a modern 3PL partner that combines cutting-edge automation with the flexibility of a family-run business — and proving that order accuracy doesn’t have to come at the expense of scalability or labor efficiency.
Interested in RFID?
An RFID tracking system can help organizations of all sizes improve their supply chain efficiency. Contact the CYBRA team to schedule a demo today.