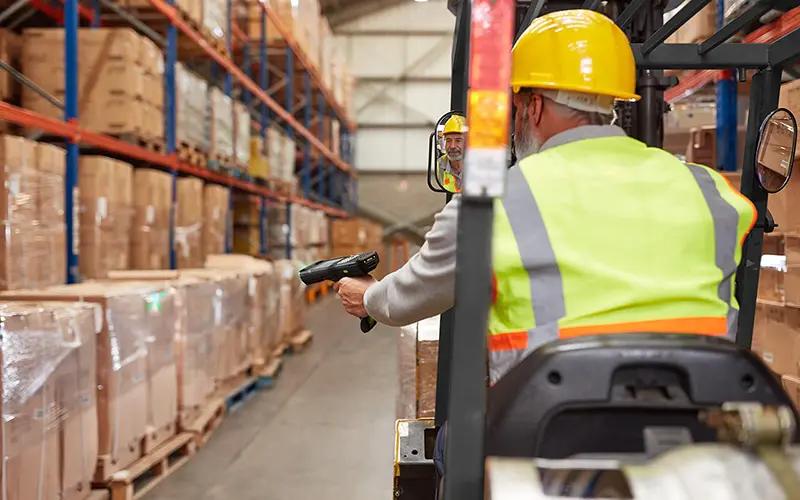
Radio Frequency Identification (RFID) technology continues to transform warehouse and manufacturing operations by delivering real-time visibility, automation, and inventory accuracy. However, while RFID systems are powerful, they are not immune to challenges. When improperly implemented or maintained, errors in RFID scanning can undermine productivity, reduce data accuracy, and frustrate workers.
Fortunately, most scanning errors are preventable. By understanding the root causes and knowing how to address them, manufacturers and warehouse managers can maintain reliable RFID performance and ensure smooth operations. In this article, we explore the most common errors in RFID scanning, what causes them, and how to correct course.
Why RFID can be Challenging
While RFID offers powerful advantages over traditional tracking methods, it’s not a plug-and-play solution. Factors like tag placement, reader configuration, and environmental conditions can all impact performance.
Without proper planning and setup, even a well-designed system can produce inconsistent results. Understanding these challenges is the first step to getting the most out of your RFID investment.
Components of an RFID System
RFID Tags
RFID Printers
Readers
Antennas
Portals & Tunnels
8 Common Errors in RFID Scanning and Tag Reading
Even the best RFID systems can fall short if small details go unchecked. From hardware issues to environmental interference, errors in RFID scanning and tag reading can disrupt workflows, delay shipments, and throw off inventory accuracy. Before you troubleshoot, it helps to know exactly what to look for.
Here are eight of the most common pitfalls to watch out for—and how to avoid them.
1. Poor Tag Placement
One of the most frequent sources of scanning issues is improper tag placement. RFID tags must be positioned in a way that ensures consistent readability by fixed or handheld readers. However, in many facilities, tags are placed in awkward or obstructed locations—on curved surfaces, near metal, or under shrink wrap—making them difficult or impossible to read.
How to fix it:
Apply tags to flat, outward-facing surfaces. Use on-metal or specialty tags for challenging materials like metal or liquid containers. Test read rates in real-world conditions before standardizing placement.
3. Tag Collision
In high-density tagging environments, tag collision becomes a serious concern. This occurs when multiple passive RFID tags respond to a reader simultaneously, making it difficult for the reader to distinguish between signals.
How to fix it:
Choose RFID systems with advanced anti-collision algorithms and ensure your software can prioritize or batch-process reads effectively. Reduce the number of tags read at once if necessary, especially in high-volume picking or packing zones.
4. Reader Interference
Another common issue arises from RF interference between multiple readers or nearby electronic equipment. When two or more RFID readers operate in close proximity, their signals can overlap or collide, creating inconsistent or failed reads.
What to do:
Adjust reader power settings and orientation. Use anti-collision protocols, time-based polling, or strategically staggered reader intervals. Additionally, ensure readers aren’t installed near high-interference equipment like industrial motors or heavy Wi-Fi zones.
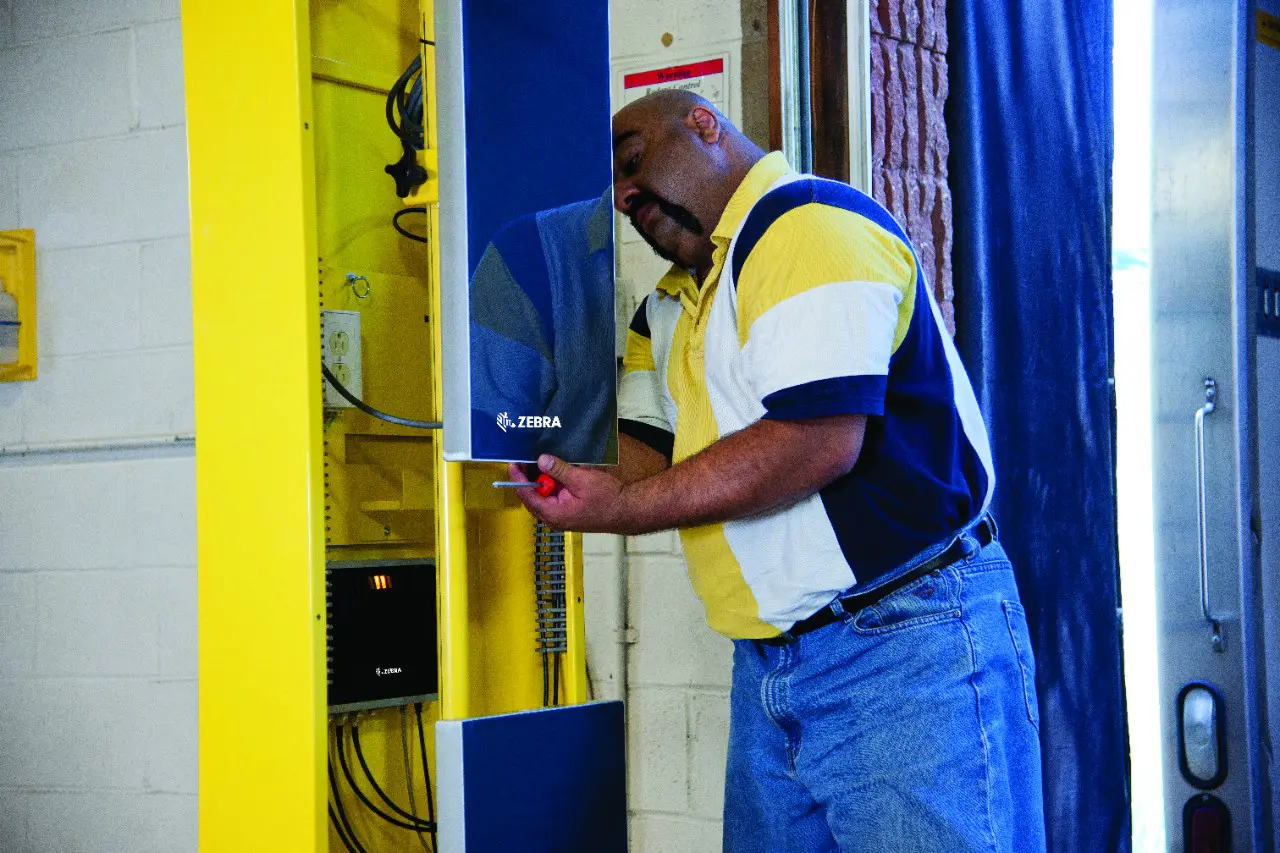
5. Inadequate Reader Coverage
If an RFID reader does not fully cover the intended scanning area, some tags may fall into dead zones. This is especially common in large warehouses, loading docks, or dynamic environments with moving inventory.
How to address it:
Perform a read zone audit using handheld scanners or reader mapping tools. Adjust antenna angles and reader placement to ensure full coverage. In some cases, adding additional antennas or repositioning equipment may be required.
6. Software Misconfiguration
Even when the hardware is installed correctly, poorly configured software can cause scanning errors. Examples include mismatched tag IDs, outdated inventory records, or integration issues between your RFID system and warehouse management software.
How to fix it:
Double-check system configurations during setup and after software updates. Sync all RFID data with your WMS in real time and use alerts to catch inconsistencies. Ongoing software testing should be part of your RFID maintenance routine.
7. Environmental Factors
Environmental conditions can significantly impact RFID performance. High humidity, electromagnetic interference, and even reflective materials near the tag can distort signals or reduce read accuracy.
What to consider:
Evaluate your facility’s environment before deployment. Use environmental shielding or tag housings as needed. For sensitive areas, consider active RFID solutions or hybrid systems that combine barcodes and RFID for failover.
8. Human Error
Despite automation, human error still contributes to RFID scanning issues. Workers may forget to scan, incorrectly orient tags, or bypass RFID zones altogether—especially in fast-paced environments where time is tight.
How to reduce it:
Train workers on proper scanning workflows and reinforce best practices regularly. Use hands-free RFID systems where possible to eliminate manual steps, and implement real-time alerts when scans are missed.
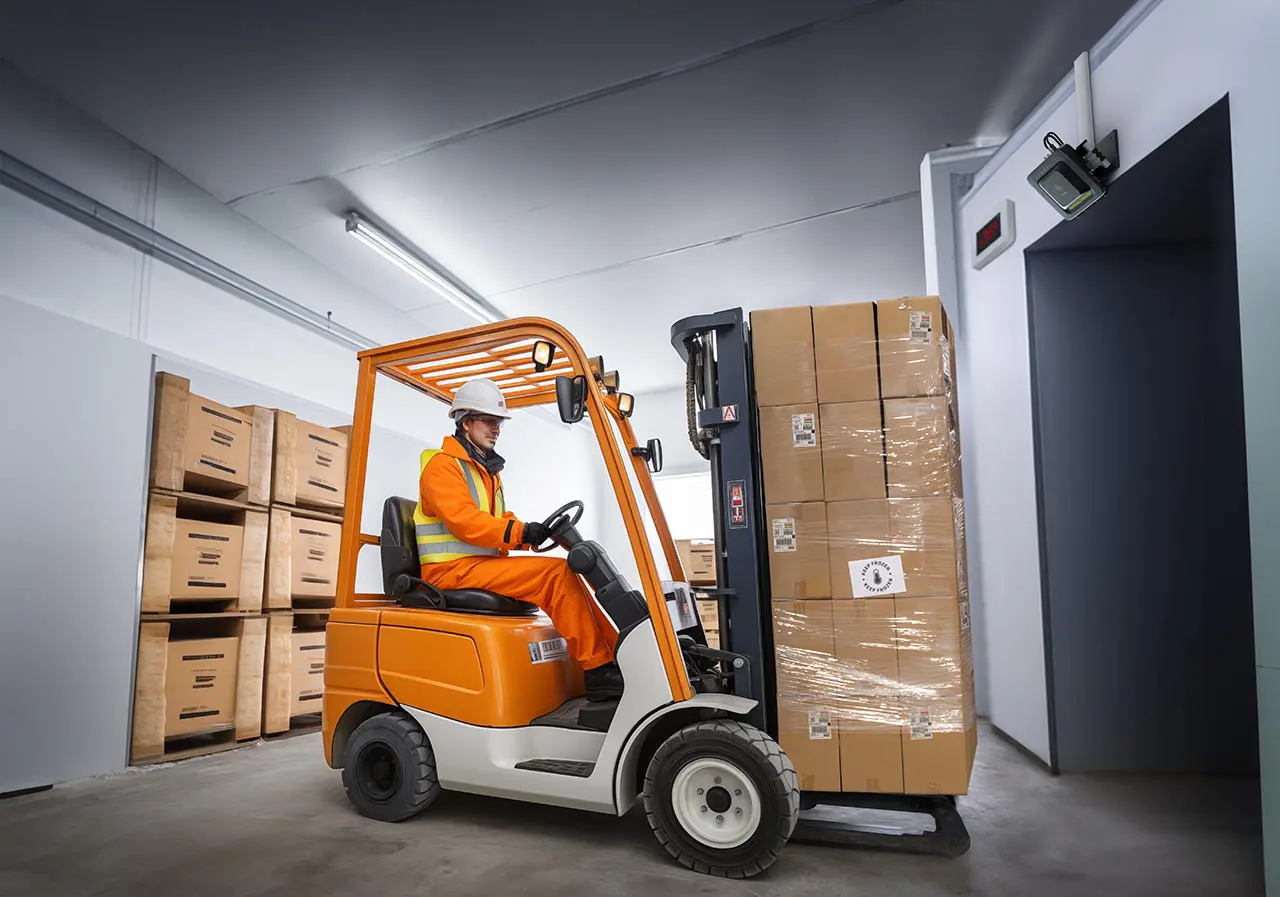
Why It Matters: The Cost of Ignoring RFID Errors
When scanning errors go unaddressed, they create ripple effects across operations. Inventory records become unreliable, shipments get delayed, and customer satisfaction suffers. In manufacturing, missed reads can disrupt production schedules or result in compliance issues. Therefore, identifying and eliminating scanning errors is not just a technical concern—it’s a strategic imperative.
Moreover, the financial impact is real. Misreads and system faults can lead to unnecessary labor costs, lost inventory, and even regulatory penalties in industries like healthcare or aerospace. By investing in robust training, hardware testing, and smart system design, businesses can maximize their RFID ROI.
Final Thoughts: Mastering RFID Scanning for Operational Excellence
RFID systems offer enormous potential—but only when they function reliably. By proactively addressing common errors in RFID scanning, warehouse and manufacturing teams can maintain high accuracy, reduce waste, and scale with confidence.
Whether you’re rolling out a new system or refining an existing one, prioritize tag quality, reader placement, and worker training. Regular audits and software tuning go a long way in maintaining peak performance.
With the right attention to detail and a commitment to continuous improvement, RFID can become one of the most dependable tools in your operational toolkit.
Interested in RFID?
An RFID tracking system can help organizations of all sizes improve their supply chain efficiency. Contact the CYBRA team to schedule a demo today.