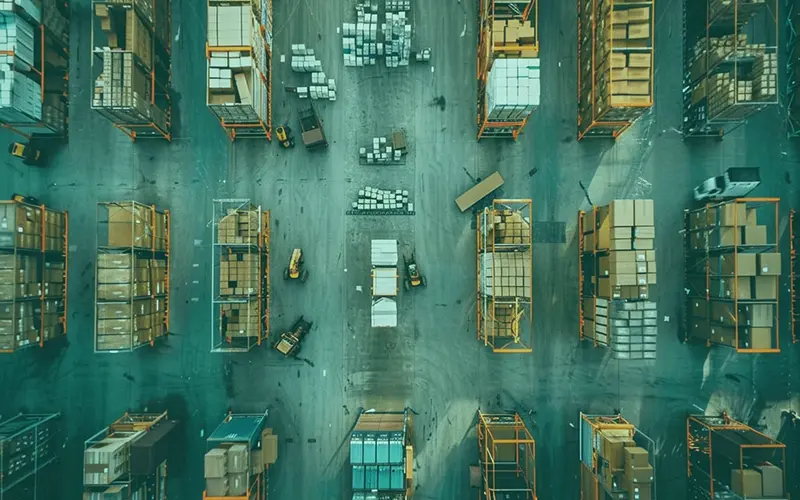
The world of logistics and warehousing has been evolving at lightning speed, and warehouse automation is no longer a luxury but a necessity for businesses aiming to stay competitive. According to ResearchAndMarkets, the global warehouse automation market is expected to reach $30 billion by 2026. With advancements in technology, businesses are adopting innovative strategies to streamline operations, reduce errors, and maximize efficiency.
In this article, we’ll explore five warehouse automation strategies that can significantly impact productivity and ensure your warehouse runs like a well-oiled machine.
Why Warehouse Automation Is More Important Than Ever
The pressures on today’s warehouses have never been greater. E-commerce growth, shrinking delivery windows, and ongoing labor shortages mean that even small inefficiencies can ripple into costly delays. At the same time, customer expectations for speed and accuracy are rising, leaving little room for error.
Automation addresses these challenges head-on by reducing reliance on manual processes, improving consistency, and giving managers real-time visibility into operations. A recent McKinsey study found that warehouses adopting automation can boost productivity by up to 25%, while also reducing operating costs. Beyond efficiency, automation also helps create safer work environments by cutting down on repetitive tasks and minimizing the risk of accidents.
In short, automation is no longer just about gaining an edge—it’s about staying competitive in a supply chain landscape that demands faster, leaner, and smarter operations.
Here are 5 warehouse automation strategies organizations are rolling out to optimize operations:
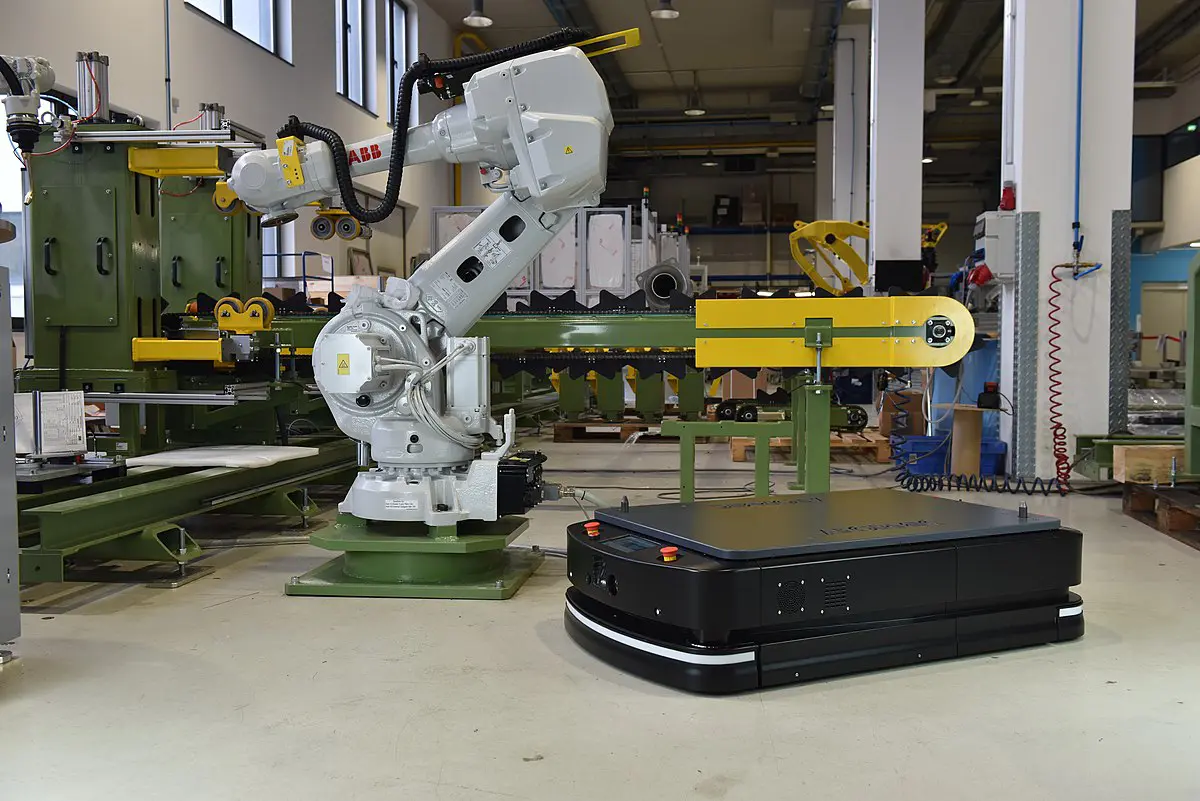
1. Automated Guided Vehicles (AGVs)
Automated Guided Vehicles (AGVs) are autonomous robots that handle material transportation within the warehouse. AGVs can carry pallets, racks, or boxes along pre-defined paths, reducing the need for human-operated forklifts and cutting down on manual labor.
How AGVs Work:
AGVs use magnetic strips, sensors, or cameras to navigate through the warehouse autonomously. They can be programmed to transport goods from one location to another without the risk of human error.
According to Grand View Research, AGVs are a critical part of the warehouse automation market, expected to grow by 7.3% annually through 2025. The ability to work around the clock, reduce workplace injuries, and minimize operational costs makes AGVs an essential investment for warehouses looking to scale efficiently.
Applications in Warehousing:
- Automating repetitive tasks: AGVs excel at transporting goods across long distances within the warehouse, eliminating the need for workers to walk back and forth.
- Reducing downtime: Since AGVs don’t need breaks, they can operate 24/7, improving warehouse throughput.
Learn more about AGVs and warehouse robotics from Robotics Business Review.
2. Pick-to-Light and Put-to-Light Systems
Pick-to-Light and Put-to-Light systems use LED indicators to direct warehouse workers during picking and sorting tasks. This method improves picking accuracy and speed by guiding workers with visual cues rather than requiring them to search for products manually.
How Pick-to-Light Works:
Pick-to-Light systems use lights installed on warehouse shelves to signal which items need to be picked and in what quantity. This allows workers to move quickly and efficiently, reducing the likelihood of errors. Conversely, Put-to-Light directs workers where to place items during sorting and packing operations.
Benefits of Pick-to-Light:
Studies show that Pick-to-Light systems can increase picking accuracy by up to 99.9% and improve order fulfillment speed by 30-50%. This is particularly useful in high-volume warehouses where manual picking errors can lead to costly returns and delays.
Applications in Warehousing:
- Order picking: Speed up the picking process by providing workers with clear, visual instructions on where to go and what to grab.
- Sorting and packing: Reduce mistakes by visually guiding workers on where to place products for outbound shipments.
For more details, check out Honeywell Intelligrated, a leader in Pick-to-Light solutions.
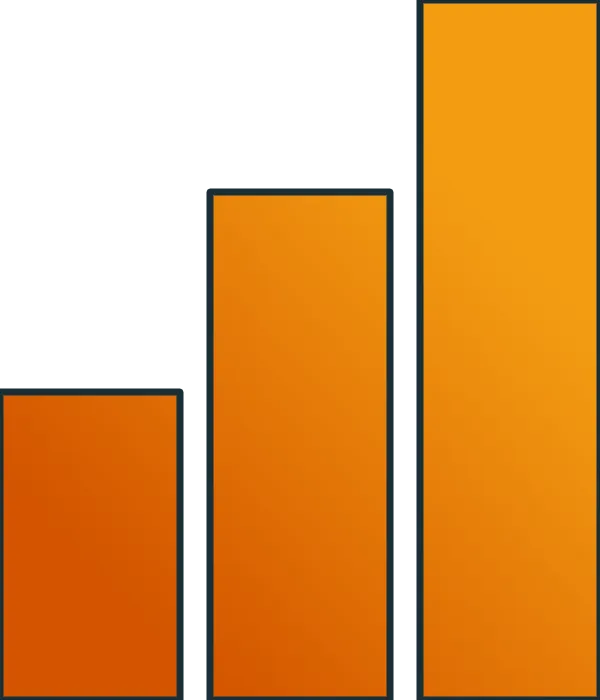
RFID ROI Calculator
Take the guesswork out of your investment with our ROI calculator. See potential savings and discover how RFID can enhance operations across industries.
3. Warehouse Management Systems (WMS)
A Warehouse Management System (WMS) is software designed to optimize warehouse operations by automating various tasks such as inventory tracking, order picking, and shipment scheduling. By integrating your WMS with other automation tools like RFID and AGVs, you can centralize operations and monitor everything in real-time.
How WMS Works:
A WMS provides a real-time overview of all warehouse activities, including stock levels, orders, and worker productivity. It helps prioritize tasks and allocate resources efficiently, ensuring smooth workflow.
According to Statista, companies using a WMS experience an average increase in efficiency of 20-30%. Additionally, WMS systems reduce labor costs by automating complex tasks such as inventory management, restocking, and order fulfillment.
Applications in Warehousing:
- Optimizing order picking: A WMS can automatically assign tasks to workers or robots, ensuring orders are picked in the most efficient way possible.
- Reducing stock discrepancies: Automated inventory updates keep your stock levels accurate, eliminating manual counting and errors.
4. Robotic Process Automation (RPA)
While robots typically handle physical tasks, Robotic Process Automation (RPA) is about automating digital and administrative processes. RPA can take over repetitive back-office tasks like order entry, inventory updates, and shipment scheduling.
How RPA Works:
RPA bots are software programs designed to mimic human interaction with computers, completing routine tasks more quickly and accurately than their human counterparts. By implementing RPA, warehouses can streamline administrative tasks that would otherwise require manual input.
According to Deloitte, RPA can reduce costs by 30-60% and improve process accuracy dramatically. In the warehouse context, this translates to faster order processing and fewer errors in paperwork.
Applications in Warehousing:
- Order processing: Automate the entry and tracking of orders to eliminate manual errors and speed up fulfillment.
- Inventory updates: Automatically update inventory levels as orders are fulfilled, reducing the need for human intervention.
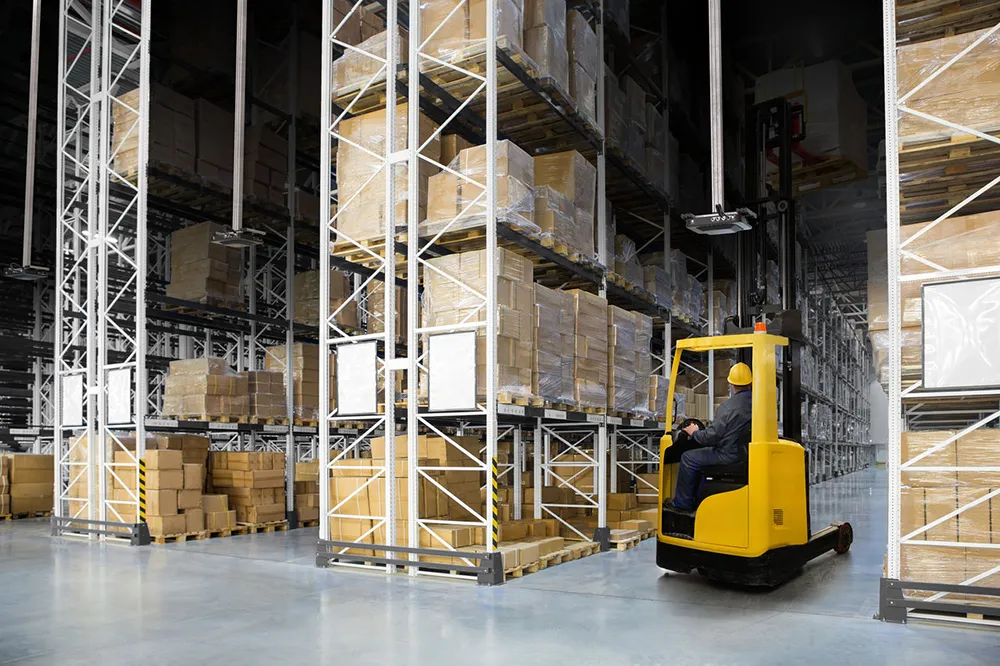
5. RFID Technology for Real-Time Inventory Tracking
One of the most revolutionary tools in modern warehousing is RFID (Radio Frequency Identification). Unlike traditional barcode scanning that requires direct line-of-sight, RFID tags can be read remotely, even when they’re tucked away on high shelves or inside boxes. This makes tracking inventory faster, more accurate, and far less labor-intensive.
How RFID Works:
RFID uses tags attached to items or pallets, which emit a signal picked up by readers placed throughout the warehouse. This allows real-time tracking of goods as they move in and out of the facility. With 99.9% accuracy in tracking inventory, RFID technology helps businesses reduce misplaced stock and prevent costly errors.
According to SupplyChain247, companies using RFID for inventory management can reduce out-of-stock instances by 30% and improve supply chain visibility in real-time.
Applications in Warehousing:
- Real-time inventory management: Get automatic updates as goods are received, stored, or shipped.
- Tracking high-value equipment: RFID isn’t limited to inventory; it’s also useful for tracking assets like forklifts or conveyor systems, ensuring they are being used effectively.
Conclusion
The warehouse of the future is here, and it’s automated. Implementing strategies like RFID, AGVs, Warehouse Management Systems, Pick-to-Light systems, and RPA can transform your warehouse operations from a labor-intensive process into a seamless, efficient system. With the right mix of automation tools, you’ll not only reduce labor costs and errors but also improve the speed and accuracy of order fulfillment, giving your business a significant competitive edge.
Interested in RFID?
An RFID tracking system can help organizations of all sizes improve their supply chain efficiency. Contact the CYBRA team to schedule a demo today.