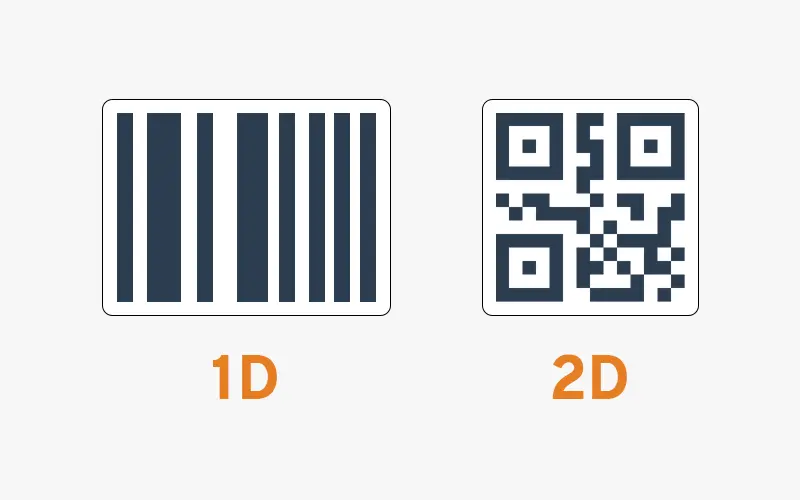
Did you know barcodes are over 70 years old? It’s true. The process of visualizing data through barcode was initially developed way back in 1948. And since then barcodes have become an integral part of virtually every industry in the world. Barcodes have revolutionized the way businesses manage inventory, track products, and streamline operations. Over the years barcodes have evolved and branched off into several variants. While many consumers may be familiar with the classic UPC barcode, also known as a 1D barcode, there are many other kinds of barcodes that serve as vital checkpoints in various industries and supply chains. Matrix barcodes, also known as 2D barcodes, offer dynamic ways to represent and store data. In this article we’ll compare and contrast 1D and 2D barcodes in order to understand when specific barcodes are ideal for certain situations.
1D Barcodes
1D barcodes, also known as linear barcodes, are the traditional and most widely recognized form of barcodes. They consist of a sequence of parallel lines and spaces of varying widths, often referred to as bars and spaces, respectively. The Universal Product Code (UPC) and the International Article Number (EAN) are common examples of 1D barcodes.
1D barcodes encode alphanumeric information, typically limited to a set number of characters. They are read using laser scanners or barcode readers, which detect the widths of the bars and spaces to decipher the encoded data. Each barcode represents a unique identifier associated with a specific product or item.
2D Barcodes
2D barcodes, on the other hand, represent a more advanced barcode technology that can store significantly more data compared to 1D barcodes. Instead of using only vertical lines, 2D barcodes incorporate both horizontal and vertical patterns, forming a square or rectangular matrix of dots, squares, or hexagons. Examples of 2D barcodes include Quick Response (QR) codes, Data Matrix, and Aztec codes.
2D barcodes use patterns of dots or squares to encode data, allowing them to store a wealth of information, including text, numbers, URLs, and even multimedia content. They can be read by specialized 2D barcode scanners or smartphone cameras equipped with barcode scanning apps.
Key Differences and Advantages
- Data Capacity: 2D barcodes have a significant advantage over 1D barcodes when it comes to data storage capacity. While 1D barcodes typically hold a limited amount of data (usually a few dozen characters), 2D barcodes can store hundreds or even thousands of characters, offering greater flexibility in encoding information.
- Error Correction: 2D barcodes incorporate error correction algorithms, enabling them to remain readable even if a portion of the barcode is damaged or obscured. This robust error correction capability enhances reliability and scanning accuracy. In contrast, 1D barcodes are more susceptible to errors when damaged or poorly printed.
- Space Efficiency: 2D barcodes can store more data in a smaller physical space compared to 1D barcodes. This compactness allows for greater versatility in printing options and placement on smaller surfaces, making them suitable for applications with limited label or packaging space.
- Content Versatility: 2D barcodes have the ability to encode different types of data, including website URLs, contact information, multimedia content, and more. They can serve as a direct link to online resources, enabling businesses to provide additional information, promotions, or interactive experiences to consumers.
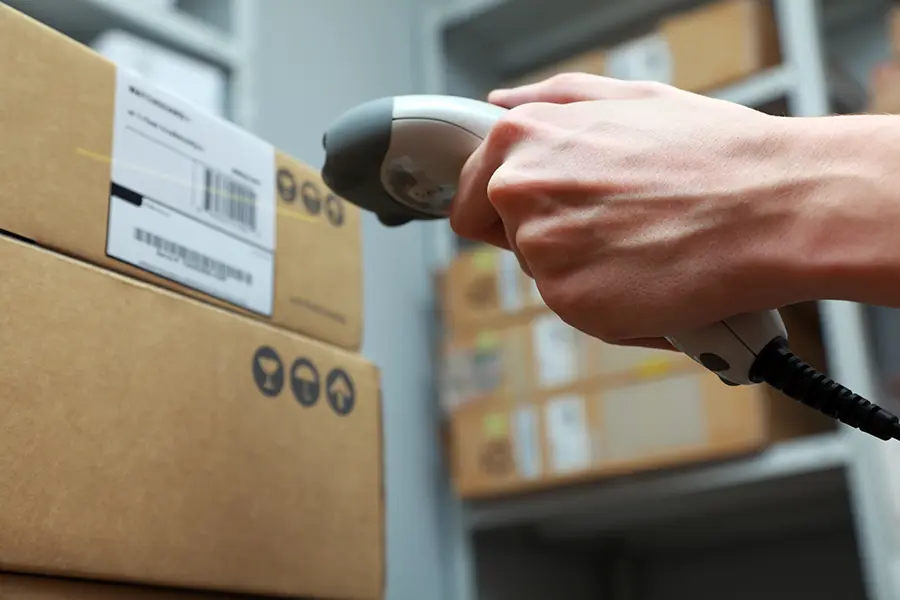
Applications and Use Cases
Barcodes play a crucial role in various industries, streamlining processes and improving efficiency. Both 1D (one-dimensional) and 2D (two-dimensional) barcodes are widely used, each offering specific advantages that cater to different applications. Here’s a breakdown of applications and use cases for 1D and 2D barcodes:
1D Barcodes Use Cases
- Basic Product Identification and Tracking: 1D barcodes are commonly used for product identification and tracking purposes. Each product is assigned a unique barcode that contains information such as the product’s stock keeping unit (SKU), manufacturer information, and other relevant details. Scanning the barcode helps track the movement and location of the product within the manufacturing and warehousing processes.
- Inventory Management: 1D barcodes play a crucial role in inventory management. By scanning barcodes on incoming and outgoing products, warehouse staff can update inventory records accurately and efficiently. This helps automate inventory management processes, reduces errors, and ensures accurate stock levels.
- Pricing and Point-of-Sale (POS): In manufacturing and warehousing, 1D barcodes are often used for pricing and point-of-sale purposes. Barcodes containing price information are printed on products or product packaging. During the checkout process, these barcodes are scanned at the point of sale, enabling automatic price retrieval and faster transaction processing.
- Shipping and Receiving: 1D barcodes are used in shipping and receiving processes to streamline operations and improve accuracy. Barcodes on shipping labels are scanned to verify and track incoming and outgoing shipments, ensuring that the right products are being shipped to the correct destinations. This helps reduce errors, improve traceability, and expedite the shipping and receiving processes.
- Batch and Lot Tracking: In manufacturing and warehousing, 1D barcodes are used to track batches and lots of products. Each batch or lot is assigned a unique barcode that contains information such as the manufacturing date, expiration date, and other batch-specific details. Scanning these barcodes helps track and trace specific batches or lots throughout the supply chain.
- Asset Management: 1D barcodes are utilized in asset management processes within manufacturing and warehousing facilities. Barcodes can be affixed to equipment, tools, or machinery to track their location, maintenance history, and other relevant information. This helps manage assets efficiently, reduce loss, and streamline maintenance processes.
- Order Picking and Fulfillment: 1D barcodes are used in order picking and fulfillment processes to improve accuracy and speed. Barcodes on picking lists or on the products themselves are scanned to ensure that the correct items are selected and packed for each order. This minimizes errors, reduces order processing time, and enhances customer satisfaction.
2D Barcodes Use Cases
- Advanced Product Identification and Tracking: 2D barcodes are used to uniquely identify products and track them throughout the manufacturing and warehousing processes. Each product can be assigned a unique barcode that contains information about the product, such as its serial number, batch number, manufacturing date, and other relevant details.
- Inventory Management: 2D barcodes are used to manage inventory efficiently. By scanning the barcodes on incoming and outgoing products, warehouse staff can update inventory records accurately and in real-time. This helps in automating inventory management processes, reducing errors, and ensuring accurate stock levels.
- Asset Tracking: 2D barcodes can be used to track and manage various assets within a manufacturing or warehouse facility. By affixing barcodes to equipment, tools, or machinery, businesses can easily track their location, maintenance history, and other relevant details. This enables efficient asset management and reduces the risk of loss or misplacement.
- Quality Control and Inspection: 2D barcodes are used in quality control processes to track and trace products during inspections. Barcodes can be scanned at different checkpoints to ensure that each step of the manufacturing or assembly process has been completed correctly. This helps identify any defects or deviations, enabling prompt corrective actions.
- Order Fulfillment and Shipping: In warehouses, 2D barcodes are used to streamline order fulfillment and shipping processes. Barcodes on products and packaging labels enable accurate picking, packing, and shipping of orders. Scanning barcodes at various stages ensures that the right products are being shipped to the correct destinations, reducing errors and improving efficiency.
- Work-in-Progress Tracking: 2D barcodes are employed to track the progress of products during the manufacturing or assembly process. Each workstation or production stage can have a barcode scanner to update the system with the completion status of each unit. This helps monitor production flow, identify bottlenecks, and manage workloads effectively.
- Recall and Warranty Management: In the event of a product recall or warranty claim, 2D barcodes can be used to identify and trace affected products quickly. The barcode can contain information about the product’s manufacturing batch, allowing businesses to identify specific units and take appropriate actions, such as contacting customers or arranging repairs/replacements.
Adding Barcodes to Your Operations
Chances are your supply chain already relies on 1D and/or 2D barcodes. But there’s a big difference between using barcodes and using them effectively. How barcodes are printed, added to labels, affixed to inventory or equipment, and scanned all must be taken into account in order ensure efficient barcoding throughout your organizations operations. If your organization is struggling with things like asset tracking, inventory management, or inbound/outbound shipping ops, it may be time to modernize your barcoding system.
Better Labeling, Better Printing
Ensure every label is accurate, compliant, and printed without delays. Discover how CYBRA’s barcode and printing solutions streamline operations and eliminate errors.