
Supply chain 4.0, also known as Industry 4.0, is one of the most significant trends in manufacturing and supply chains today. It is a digital innovation that can help organizations create an integrated network for better visibility and responsiveness.
The benefits of Industry 4.0 include a more resilient network and increased operational efficiency. Businesses that are ready to embrace this digital innovation can move from crisis to agile shift sourcing and faster manufacturing.
What is Supply Chain 4.0?
Supply Chain 4.0 is the next evolution of supply chain management that integrates advanced digital technologies to create smarter, faster, and more responsive operations. Inspired by Industry 4.0, it transforms traditional, linear supply chains into interconnected, agile networks using tools like:
- RFID: Provides visibility of inventory, assets, and shipments. Unlike barcodes, RFID tags can be scanned automatically and in bulk, enabling faster, more accurate tracking throughout warehouses, factories, and transportation hubs.
- IoT (Internet of Things): Sensors and RFID tags provide real-time tracking of goods, equipment, and conditions (e.g., temperature, location).
- AI & Machine Learning: Enables demand forecasting, anomaly detection, and autonomous decision-making.
- Big Data & Analytics: Helps process and interpret large volumes of supply chain data to improve performance and planning.
- Robotic Process Automation (RPA): Automates repetitive logistics and procurement tasks.
- Cloud Computing: Centralizes data access and collaboration across the entire supply chain ecosystem.
- Digital Twins: Creates virtual replicas of physical supply chains for simulation, testing, and optimization.
- Blockchain: Improves traceability, trust, and security, especially for global and multi-party operations.
What You Can Do with Supply Chain 4.0
Supply Chain 4.0 isn’t just a buzzword—it’s a blueprint for smarter, faster, more resilient operations. By integrating advanced technologies and data-driven processes, companies can unlock powerful capabilities across their entire supply chain.
Here’s what that looks like in action:
Interoperability
Connect machines, systems, and teams across your supply chain. With enterprise interoperability, your software and hardware—from different vendors, countries, and workflows—can speak the same language. The result? Faster decisions, streamlined operations, and more effective use of both data and human insight.
End-to-End Visibility
See everything—from raw materials to customer delivery. Real-time visibility helps you anticipate disruptions, track inventory instantly, and respond to demand faster. It also improves customer satisfaction by offering accurate order status and product availability updates.
Integrated Planning
Break down silos between demand, supply, and logistics. Integrated planning tools powered by AI and automation let you optimize inventory, reduce waste, and respond to market shifts with agility. Think: autonomous trucks, warehouse robots, and smarter transport routes all working in sync.
Streaming Data
Turn raw data into real-time intelligence. By combining sensor data, machine logs, and IoT inputs, you can spot inefficiencies, predict equipment failures, and dynamically adjust production schedules—all before problems arise.
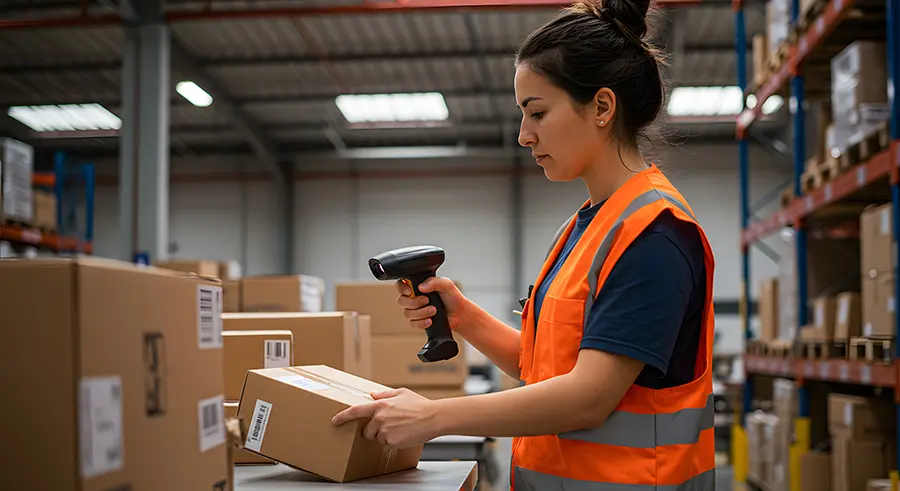
How to Get Started with Supply Chain 4.0
Getting started with Supply Chain 4.0 doesn’t require a full-scale transformation from day one. The best approach is to start small, focus on areas with clear inefficiencies, and scale up gradually. Begin by assessing your current systems, technologies, and workflows. Identify where delays, errors, or blind spots occur—these are prime targets for digital improvement.
Next, define clear, measurable goals tied to your business strategy. Whether you’re aiming to reduce inventory costs, improve forecasting accuracy, or streamline fulfillment, aligning your efforts with specific KPIs will help you stay focused and demonstrate ROI.
From there, choose the right technologies to solve your most pressing problems. Many companies start with real-time visibility tools like RFID or cloud-based inventory platforms because they deliver fast, tangible results.
Whatever tools you choose, make sure your systems can support real-time data sharing, analytics, and future integration with other digital technologies.
Final Thoughts
Finally, don’t forget the people behind the process. A successful Supply Chain 4.0 rollout depends on training your teams to use new tools, interpret data, and make more agile decisions. Start with pilot programs in one facility or region, learn from the results, and use those insights to drive broader transformation across your supply chain.
Interested in RFID?
An RFID tracking system can help organizations of all sizes improve their supply chain efficiency. Contact the CYBRA team to schedule a demo today.