RFID in Manufacturing
[Updated for 2025]
Discover how RFID is transforming manufacturing in 2025—from real-time inventory tracking to automated production workflows. Learn how leading manufacturers are using RFID to boost efficiency, reduce waste, and streamline operations.
Updated on 3/11/2025
RFID in Manufacturing: What’s New in 2025
RFID technology is evolving rapidly in manufacturing, with AI-driven analytics, 5G connectivity, and enhanced cybersecurity improving real-time tracking and efficiency. Manufacturers are adopting UHF RFID for long-range visibility, integrating RFID-powered automation to reduce labor costs, and using sustainable RFID tags to meet environmental goals.
Additionally, new RFID designs improve readability on metal and liquid surfaces, while stricter regulatory compliance requirements are driving adoption in industries like pharmaceuticals, food production, and automotive manufacturing. As RFID continues to advance, manufacturers are leveraging it to optimize supply chains, increase accuracy, and enhance smart factory operations in 2025 and beyond.
For manufacturers, keeping track of inventory and equipment is an essential part of daily processes. Lost inventory has a direct correlation with reduced profits, and misplaced equipment slows down operations in ways that can throttle fulfillment throughput and production efficiency. And legacy tracking systems are struggling to keep up with modern supply chain demands. So what are manufacturers doing to keep up? 91% manufacturing professional are familiar with barcoding systems to track goods and assets. But the technology that’s on the rise is RFID.
RFID is Changing the Manufacturing World
RFID technology is changing the world of manufacturing. Its improved accuracy and cost-effectiveness have sped up the adoption of this technology.
According to a study by Zebra Technologies, over 90% of manufacturing companies plan to invest in RFID systems by 2028. This technology has the potential to improve operational processes and help companies meet the challenges they face in the fast-paced world.
4 Eye-Opening RFID Stats in Manufacturing
Up to 99.9% Inventory Accuracy
Manufacturers using RFID see inventory accuracy rates as high as 99.9%, compared to 60-80% with traditional barcode systems. (Source: Auburn University RFID Lab)
30% Faster Order Fulfillment
RFID-enabled automation helps manufacturers speed up picking and packing processes, reducing order fulfillment times by up to 30%. (Source: McKinsey & Co.)
20-50% Reduction in Labor Costs
RFID streamlines asset tracking and reduces the need for manual scanning, cutting labor costs by up to 50%. (Source: Deloitte)
Up to 80% Reduction in Manufacturing Errors
RFID eliminates mislabeling, misplaced parts, and production bottlenecks, significantly reducing costly errors on the factory floor. (Source: GS1 US)
How Does RFID Work in Manufacturing?
RFID (Radio-Frequency Identification) technology is fast becoming a cornerstone in modern manufacturing processes, revolutionizing the way products are produced, tracked, and managed. In manufacturing, RFID systems employ radio waves to communicate between tags attached to physical objects and RFID readers.
This seamless exchange of information enables real-time tracking, monitoring, and control of assets, components, and finished products throughout the production cycle.
By providing unparalleled visibility and automation, RFID enhances operational efficiency, minimizes errors, and enables precise inventory management. From streamlining supply chain logistics to optimizing inventory control, RFID technology has emerged as an indispensable tool in the quest for leaner, more agile, and highly efficient manufacturing operations across a diverse range of industries.
Start Using RFID with Minimal Investment
EdgeMicro from CYBRA is a simple RFID starter solution for streamlined logistics and inventory control. Perfect for small-scale needs or proof-of-concept projects. Implement RFID in your supply chain with minimal investment.
What is RFID technology used for?
RFID technology is transforming the landscape of modern manufacturing, offering a multitude of use cases that enhance efficiency, accuracy, and visibility in production processes. But an RFID system can do more than just detect inventory levels. Here are several key RFID manufacturing use cases:
Work-in-Process (WIP) Tracking
RFID facilitates the seamless tracking of goods as they undergo different stages of production – also known as WIP tracking. This ensures that each component receives the necessary processes, reducing errors and enhancing quality control measures.
Production Tracking and Monitoring
RFID tags are attached to products or components, allowing for real-time tracking as they move through various stages of production. This provides manufacturers with precise visibility into the status and location of each item, ensuring accurate production monitoring.
Tool and Equipment Management
RFID tags are affixed to tools and equipment, enabling manufacturers to track their usage, monitor maintenance schedules, and prevent loss or misplacement. This leads to optimized resource utilization and reduces downtime.
Regulatory Compliance and Reporting
RFID systems assist manufacturers in automating compliance with industry-specific regulations and reporting requirements. Accurate and auditable records can be easily accessed to demonstrate adherence to legal standards.
Automated Reordering and Restocking
RFID-triggered alerts automate the reordering of materials when inventory levels fall below a specified threshold. This proactive approach minimizes the risk of production delays due to stockouts.
Customized Manufacturing and Just-in-Time Production
RFID-enabled systems support customized or build-to-order manufacturing processes by automatically configuring production lines based on specific product requirements. This enables manufacturers to meet unique customer demands efficiently.
How RFID Works in Manufacturing
Tagging & Encoding
RFID tags are attached to raw materials, components, or finished goods, storing key data like serial numbers and production details.
Automated Scanning
RFID readers capture data from tags in real time, without requiring direct line-of-sight, improving tracking efficiency.
Data Integration
RFID systems connect with ERP and WMS platforms, providing real-time visibility into inventory, production, and asset movement.
Process Optimization
RFID automates inventory counts, tracks work-in-progress, prevents bottlenecks, and enhances predictive maintenance.
What are the Benefits of RFID in Manufacturing?
RFID is a great technology for managing manufacturing operations. It has the ability to improve accuracy, reduce cycle count time, improve traceability, and even reduce human error. These are just some of the benefits of RFID in manufacturing. Read on to learn more about the potential for RFID and the potential uses for your organization.
Improved Accuracy
Manufacturing today is more challenging than ever, with organizations turning to technology to improve inventory visibility. One major challenge is tracking spare parts and components essential for operations. Losing track of inventory is a risk businesses can’t afford in today’s on-demand economy.
RFID improves security, prevents product tampering, and enhances supply chain efficiency. It’s widely used in industries like textiles and apparel for inventory management, tracking finished goods, and warehousing.
Asset tracking is another key challenge. RFID provides fast, reliable tracking of production line components, dispatched products, industrial containers, and tools—eliminating costly human errors.
RFID integrates with ERP systems to create a holistic view of supply chain operations. It connects processes like sales planning, assembly planning, and production scheduling, improving efficiency and ensuring timely deliveries.
RFID readers strategically placed in warehouses provide real-time inventory visibility, reducing shrinkage, minimizing stock levels, and cutting costs while keeping track of valuable assets.
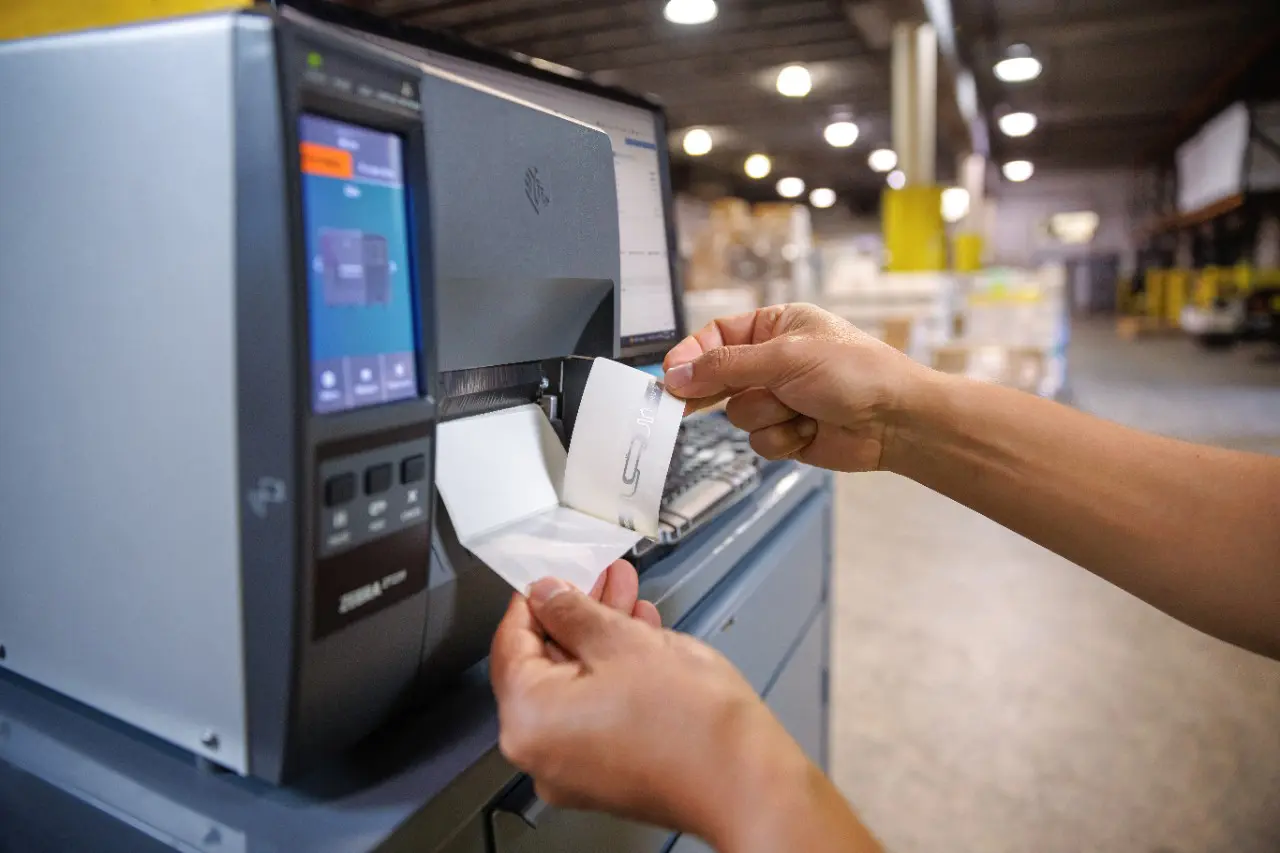
Reduced Cycle Count Time
RFID technology transmits real-time inventory data, reducing out-of-stock situations and improving customer experience. According to GS1 US, RFID can reduce cycle count times by up to 50%.
RFID tags, which can be passive or active, track assets throughout production, validating inventory at key stages to prevent delays. It also automates inbound/outbound checks, replenishment, and safety stock reordering without manual spot checks.
Unlike barcodes, RFID can scan multiple items at once without requiring line-of-sight. This eliminates the need to lift or see boxes, significantly reducing effort and improving count accuracy.
Retailers use RFID to track inventory and quality data, ensuring products are in the right place at the right time. Lululemon, for example, uses RFID chips on hang tags to enhance inventory accuracy and customer experience.
RFID allows manufacturers to track inventory to within a few feet, eliminating manual searches and improving decision-making through real-time visibility. Data collected from RFID can also be used to enhance manufacturing processes, ensuring quality and efficiency.
Improved Traceability
RFID enhances traceability across manufacturing, benefiting product genealogy, lifecycle tracking, and just-in-time (JIT) environments. It streamlines warehousing and yard management while improving supply chain efficiency, reducing costs, and increasing productivity.
With end-to-end traceability, RFID helps pinpoint production issues, identify damaged products, and improve audit processes. It also enables real-time asset tracking, reducing delivery-related frustrations and increasing customer satisfaction.
RFID is particularly valuable in the food industry, simplifying inventory management, reducing costs, and preventing duplicate orders. By automating product tracking, manufacturers maximize efficiency and minimize waste.
RFID has been commercially available for over 30 years and is now a standard in tracking equipment, containers, and materials in industrial environments. It provides superior traceability and accuracy compared to barcodes, offering more detailed product information.
Reduced Human Error
RFID significantly reduces human error in manufacturing by providing real-time item location tracking. This eliminates costly mistakes like misplaced materials, contamination, and skipped production steps, which can lead to recalls and lost business.
The technology integrates with inventory management software for real-time production tracking. RFID systems include tags, readers, servers, middleware, and application software, ensuring seamless operation.
Human errors in manufacturing can cripple operations, leading to lost revenue and potential end-user risks. RFID mitigates these risks by tracking components, semi-finished products, and finished goods while analyzing employee and department performance.
While RFID adoption involves cost and investment, it offers substantial benefits in accuracy, efficiency, and decision-making. Ongoing improvements in standardization, privacy, and security will continue to enhance its effectiveness in manufacturing.
How to Deploy RFID in Manufacturing Environments
Deploying RFID technology in a manufacturing environment, especially with a sophisticated system like Edgefinity IoT, requires a strategic and methodical approach.
The process begins with a comprehensive assessment of the manufacturing processes and the specific needs for RFID integration. First, RFID tags are selected based on the type of assets to be tracked, ensuring they are compatible with Edgefinity IoT’s capabilities. Next, RFID readers and antennas are strategically placed at key points in the production line and storage areas. These readers communicate with the RFID tags to capture data, enabling real-time tracking. The Edgefinity IoT system is then configured to process and manage the RFID data, allowing for easy access and analysis. Training for personnel on how to use the system is crucial for a successful deployment. Regular testing and monitoring ensure that the system operates effectively and any adjustments can be made promptly.
With Edgefinity IoT, manufacturers can seamlessly integrate RFID technology to enhance production tracking, streamline operations, and optimize inventory management for increased efficiency and productivity.
Interested in RFID?
An RFID tracking system can help organizations of all sizes improve their supply chain efficiency. Contact the CYBRA team to schedule a demo today.