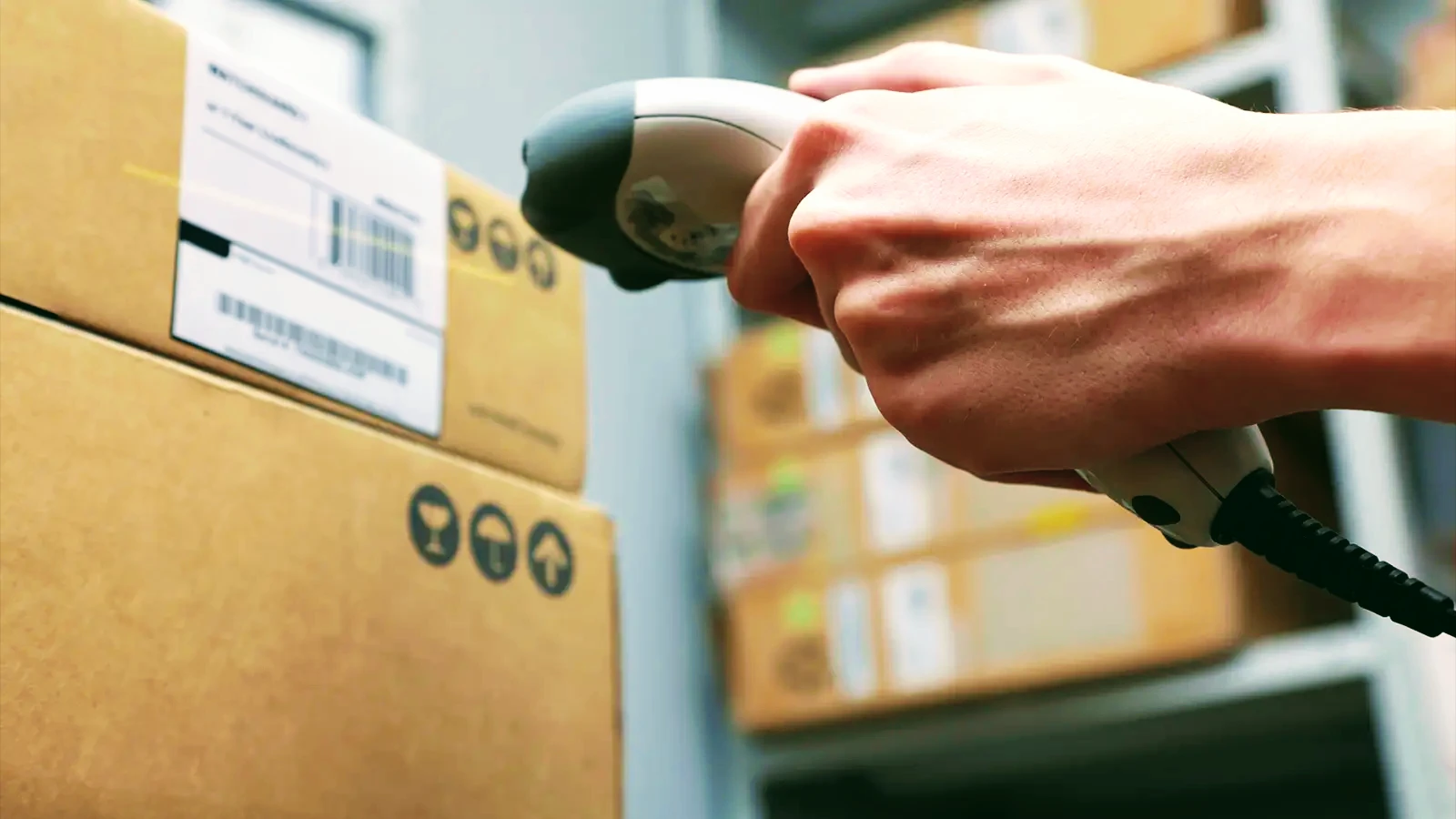
Mislabeling isn’t just a minor hiccup—it can trigger costly recalls, regulatory fallout, and customer distrust. In 2024, labeling mistakes fueled 45.5% of U.S. food recalls, translating to around $1.9 billion in direct costs—about $10 million per incident (via New Food Magazine). These errors are often tied to undeclared allergens, with 71% of major allergen-related recalls linked to label errors.
Beyond food, data quality problems, including mislabeling, are hurting supply chains more broadly. A GS1 US survey found 43% of organizations struggle to maintain full visibility in their operations, linking this directly to inaccuracies in labeling and item data.
Meanwhile, in the consumer packaged goods (CPG) sector, the Food Marketing Institute reports that recalls now average $10 million in direct costs, with 68% of consumers stopping purchases after a safety incident.
Preventing mislabeling is more than a compliance checkbox—it’s essential for protecting your bottom line, your brand, and your customers.
Read on to learn about some of the best ways to avoid mislabeling.
Avoid Printing Labels in Advance
One way to prevent mislabeling in manufacturing is to avoid printing labels in advance. Ideally, labels should be printed as close to the time of application as possible. This approach will help avoid ‘clearing the work area’ problems and ‘extra’ labels floating around.
Many discrete manufacturers will print labels in advance and then apply them to the products as they are produced. Unfortunately, it’s not always possible to know in advance how many products are going to be produced. In such a situation, extra labels may remain unaccounted for on the work surface, and a product may accidentally be mislabeled.
While the printing process can lead to fewer labeling problems, it doesn’t guarantee that a labeling job will be successful. It’s important to remember that proper application is just as important as perfect printing. By working with a labeling system integrator, you can minimize the chance of misapplication.
Data Validation
Data validation is a fundamental process used to prevent mislabeling in manufacturing. It prevents labelling errors by verifying the accuracy of data entered by users. Data validation is crucial because it forces users to enter data in a specific format, such as MM/DD/YYYY. It also prevents waste and wasted time because incorrect data will not be printed.
Data validation methods involve rigorous statistical analysis. By doing this, organizations can ensure that the products are within their specifications. Most manufacturing plants are unable to afford the expense of testing every incoming material and rely instead on statistical sampling. Random sampling is not as effective as it should be. In addition, the time and effort required to collect samples from bins and barrels can be considerable. Furthermore, the samples must be transported to a lab.
Data validation methods based on detection of outliers or anomalies are the most common way to detect mislabeling. These methods aim to clean data during preprocessing to eliminate points that deviate significantly from the model. In addition, these methods use statistical techniques to detect outliers, which are anomalies that deviate significantly from the norm.

Automated Quality Management Systems
Mislabeling is a costly problem, costing some companies millions of dollars each year. While automated quality management systems can help manufacturers identify label errors, these systems are still in their infancy. A recent Digimarc survey revealed that 67 percent of manufacturers still rely on manual inspection.
One way to avoid this problem is to automate the marking and coding process. Some companies have successfully adapted this system for their manufacturing operations. Automated coding and marking solutions use cameras to ensure proper labeling and stop production if a certain condition is met. This prevents costly recalls. Automated quality management systems can also help manufacturers reduce human errors, such as mislabeling products.
Automation can also improve productivity. It can minimize rework, scrap, and overtime. Increasing productivity leads to happier employees and customers. It can even increase market growth. Additionally, automation provides insight into production, allowing managers and line workers to adjust production processes proactively.
Traceability
Mislabeling is a common issue in manufacturing facilities. It can result in lost revenue and valuable time. In fact, it is estimated that 76% of manufacturers mislabel a minimum of 10% of their goods. Consequently, preventing mislabeling is essential to the success of any manufacturing operation. Mislabeling costs organizations on average $1.3 million per year.
The right labeling system can help manufacturers avoid such costly mistakes. A label management system can help companies centralize label design and printing to minimize errors. It also helps reduce the number of labels on the line and makes the coding process easier. With proper labeling, the production process can move more quickly and with better product quality.
Besides causing loss to customers, mislabeled products can also cause production line shutdowns. According to a survey conducted by Digimarc for Packaging World magazine, 52% of manufacturers shut down their production lines at least once a week to identify mislabeled products. Besides affecting sales, mislabeled products result in waste, resulting in a loss for the enterprise.
Deploying Label Printing Software to Improve Accuracy
Even with careful processes in place, manual label creation and disconnected printing systems leave too much room for error.
That’s where label printing software like MarkMagic comes in. Designed for manufacturers who need speed, accuracy, and compliance, MarkMagic centralizes your label creation, integrates directly with your ERP or WMS, and ensures the right data is printed on the right label—every time.
Mislabeling isn’t just costly—it’s preventable. With the right labeling software in place, you can boost efficiency, protect your brand, and stay compliant without compromising on speed.
Better Labeling, Faster Printing.
Ensure every label is accurate, compliant, and printed without delays. Discover how CYBRA’s barcode and printing solutions streamline operations and eliminate errors.