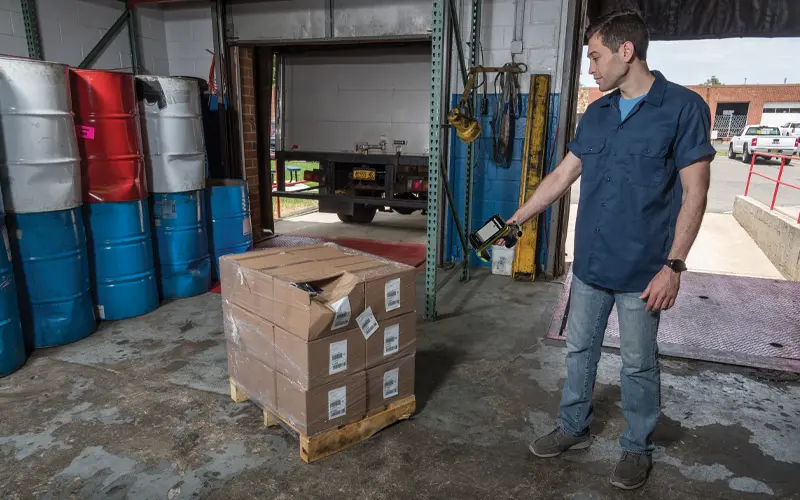
RFID is no longer a niche technology—it’s quickly becoming a cornerstone of modern operations. From warehouses and hospitals to retail giants and construction sites, RFID is being adopted by major brands looking to boost visibility, automation, and efficiency.
Companies like Walmart, Delta Airlines, Target, Macy’s, Nordstrom, Lowe’s, and Decathlon have already integrated RFID into their logistics, inventory, and customer experience strategies—and the results are hard to ignore.
According to a report by Statista, the global RFID market is expected to grow from $14.5 billion in 2023 to over $35 billion by 2030, as businesses across industries turn to the technology to solve age-old challenges like asset loss, manual data entry, and inventory inaccuracy.
But jumping into a full-scale RFID implementation without testing the waters can be risky. That’s why starting with a focused, well-planned pilot project is the smartest way to explore RFID’s potential—without overwhelming your team or your budget.
Starting an RFID pilot project is a smart way to test the technology in a controlled environment before rolling it out at scale. Below is a step-by-step breakdown to get you going, whether you’re in logistics, manufacturing, retail, healthcare, or any asset-heavy industry.
What is an RFID Pilot?
An RFID pilot is a test for new RFID solutions. Pilots might be run by companies to help meet mandate requirements or to test new applications of RFID technologies.
Pilots that indicate a good return on investment (ROI) are then put into expanded deployment known as rollouts. This benefits the testing company and the RFID industry as a whole.
Improving Operational Efficiency
Implementing RFID technology can significantly enhance operational efficiency. For instance, a study by the Auburn University RFID Lab found that RFID can increase inventory accuracy from 63% to 95%, leading to more precise stock management and reduced errors.
Why Start with a Pilot?
An RFID pilot gives you a low-risk opportunity to validate the technology within your own operational environment. It allows you to:
- Test performance in real-world conditions
- Identify unexpected challenges
- Train staff on new workflows
- Fine-tune RFID tag placement and reader coverage
- Build a business case for scaling
The best pilots are narrow in scope but rich in insight—they focus on a specific process or location that reflects broader operational goals.
RFID Pilot Benefits
An RFID pilot program allows organizations to do the following:
Test Your
System
Identify
Challenges
Train
Staff
Fine-tune Tag
Placement
Build a
Business Case
Steps to Starting a Pilot
If you’re wondering how to launch your first RFID initiative, we can walk you through every step to successfully kickstart an RFID pilot program—from goal-setting and hardware selection to data collection and scaling.
Step 1: Define a Clear Objective
The success of your RFID pilot hinges on having a clear and specific objective. Before implementing any technology, take time to define exactly what you’re trying to learn or prove. Ask yourself: What problem are we solving? What measurable outcome will indicate success? And who will use the data, and how will it impact their workflow?
Here are some common goals RFID pilots address:
- Reduce manual inventory time
- Prevent asset loss or theft
- Improve shipping accuracy
- Track movement of high-value items
- Automate check-in/check-out processes
Whether you’re aiming to reduce inventory errors, cut down on manual labor, or track the real-time movement of assets, your goal should be focused, measurable, and directly tied to a business challenge. A well-defined objective ensures that your pilot remains targeted, actionable, and aligned with long-term value.
Tip: Avoid vague goals like “make things more efficient.” Instead, go for something measurable: “Reduce inventory audit time by 60%.
Step 2: Choose a Strong Use Case
Not all parts of your operation need RFID. Focus on a high-impact area where visibility gaps are costing time or money. Ideal pilot environments include:
- One warehouse aisle or zone
- A specific fleet of tools or vehicles
- High-turnover inventory in a backroom
- Controlled areas like clean rooms or lab storage
This should be small enough to control, but representative enough to scale later.
Industrial Use Cases
RFID technology is being widely adopted across industries to improve visibility, reduce manual labor, and boost accuracy. In supply chain and logistics, it enables real-time tracking of shipments, automates warehouse inventory, and ensures greater accuracy at loading docks.
In manufacturing, companies use RFID to track work-in-progress, monitor equipment, and streamline production workflows. Retailers benefit from accurate inventory counts, theft prevention, and faster fulfillment, especially in omni-channel environments.
In healthcare, RFID is used to monitor medical equipment, track patient interactions, and manage sensitive assets like blood or surgical tools. Construction sites rely on it to track tools, enforce safety compliance, and prevent asset loss across large job areas.
Meanwhile, data centers and IT departments use RFID to monitor server equipment and automate compliance audits. From retail shelves to airport tarmacs, RFID is helping organizations save time, reduce errors, and operate with real-time precision.
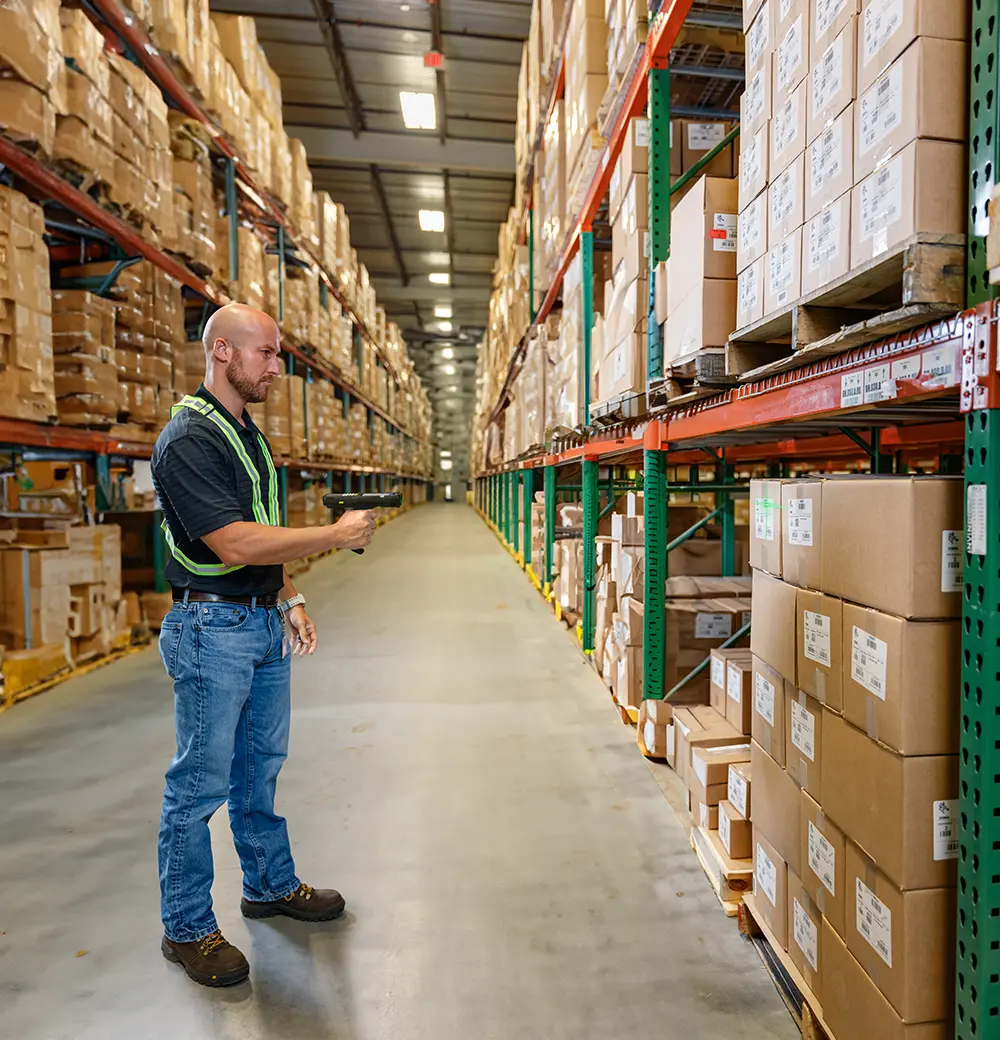
Step 3: Identify What You’re Tagging
Once you’ve chosen a use case, the next step is to define what you’ll be tracking—and how. Start by selecting the actual items or assets to be tagged. Consider:
- Are the items fixed or mobile?
- What material are they made of (metal, plastic, fabric, liquid)?
- Are they stored indoors or outdoors?
- How many assets do you need to track?
In most pilots, tagging 100 to 500 assets strikes the right balance between sample size and manageability. After this, you’ll need to select the appropriate RFID technology stack.
RFID Tags:
- Passive tags: battery-free, low-cost, short to medium range.
- Active tags: battery-powered, longer read range, higher cost.
- Specialty tags: designed for metal surfaces, high temperatures, wash cycles, etc.
RFID Readers:
- Handheld readers: flexible, mobile, great for inventory auditing or inspections.
- Fixed readers: mounted near doors, conveyors, gates, or loading docks.
- Portal/gate systems: for tracking bulk movement through specific zones.
Matching the right tags and readers to your asset type and environment is critical. A trusted RFID provider can help you choose the best combination based on your specific needs and budget.
Tip: A successful RFID pilot isn’t just about hardware—it’s about people. Involve team members early, show how the tags and readers work, and explain how the system makes their jobs easier. Simple training and clear SOPs go a long way in ensuring smooth adoption.
Step 4: Set Up Software to Deploy in Your Environment
With the hardware selected, it’s time to build out the digital and physical infrastructure for your pilot.
On the software side, you’ll need a platform that can collect tag reads, process the data, and visualize the results. This could be a standalone RFID application, an integration into your ERP or WMS, or a custom dashboard tailored to your use case. Look for features like:
- Asset location tracking
- Inventory status updates
- Alerts and exceptions
- Real-time dashboards and historical reporting
On the physical side, the RFID environment must be set up to support accurate reads. That includes:
- Mounting readers and antennas in strategic zones
- Testing read ranges and angles
- Eliminating signal interference (especially from metal or liquids)
- Labeling or mapping zones (e.g., Aisle 1, Dock 2)
Many companies use read zone heatmaps to visually confirm that tag reads are accurate throughout the space.
By the end of this phase, you should have a fully functional environment where tagged items can be tracked and data flows seamlessly into your chosen system.
Step 5: Run Your RFID Pilot
With your environment and systems in place, it’s time to launch the pilot in real operating conditions. This is where the rubber meets the road—where you’ll test not just the technology, but how well it integrates with your existing processes and people.
Let the pilot run for 30 to 90 days, depending on your use case and business cycle. This duration allows enough time to generate meaningful data while keeping the pilot focused and manageable. Throughout the pilot, it’s essential to observe both the technical performance and the human interaction with the system.
Key things to monitor:
- Tag readability: Are all items being picked up at expected checkpoints or zones? Are there blind spots or inconsistent reads?
- Reader performance: Are antennas and gateways functioning reliably under typical usage and movement patterns?
- Data accuracy: Are the movements and status updates being reflected correctly in the dashboard or reports?
- Process impact: Are manual steps being reduced? Are team members saving time or avoiding errors?
- User behavior and feedback: Are staff adapting to the system easily? Do they trust the information they’re seeing? Are there any points of confusion or resistance?
It’s also a good time to document any surprises—positive or negative. For example, you might notice a process bottleneck you didn’t anticipate or discover that RFID works better than expected in a certain area. These insights are crucial and often lead to improvements that extend beyond the scope of RFID.
Establish a regular cadence for reviewing data and feedback during the pilot. Weekly check-ins with your team (and your RFID partner, if you’re working with one) can help you catch issues early and adjust on the fly if needed.
Remember: the goal of this phase is not perfection, but proof—proof that RFID delivers measurable value and integrates well with your workflow. What you learn here will directly inform your rollout strategy and help you avoid costly mistakes at scale.
Analysis and Next Steps
Once your pilot has run its course, the most important work begins: analyzing the results and making a clear decision about what comes next.
Start by returning to the original objectives you set. Did the pilot meet those goals? For example, if your aim was to reduce inventory time, compare your baseline data with the RFID-enabled process. If you wanted to improve asset visibility, evaluate how accurately and consistently the system tracked movements and locations. Use both quantitative results (like read accuracy, time saved, labor hours reduced, or error rate improvements) and qualitative feedback from users to tell the full story.
Some key metrics to consider:
- Inventory accuracy improvement (%)
- Time savings (e.g., cycle counts, tool retrieval)
- Reduction in lost or misplaced items
- Read failure or signal dropout rates
- User satisfaction and ease of adoption
From there, assess the overall return on investment. Even in a small-scale pilot, you should be able to project cost savings or operational gains if the system were deployed at full scale.
No matter the outcome, a well-run pilot always yields insight. Even challenges you encounter are valuable—they help you avoid those pitfalls in a broader deployment. Think of the pilot as an investment not just in RFID, but in your organization’s ability to adapt, improve, and scale smart technologies.
Interested in RFID?
An RFID tracking system can help organizations of all sizes improve their supply chain efficiency. Contact the CYBRA team to schedule a demo today.