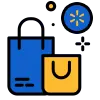
What You Need to Know About Walmart’s Latest RFID Tagging Mandate
In early 2022, Walmart announced the expansion of its RFID mandate program to additional products and departments. The retail giant is mandating its suppliers to tag home goods, sporting goods, electronics, and toys with RFID. As one of the biggest retailers in the world, this news will have major repercussions with virtually all of Walmart’s manufacturers, distributors, and vendors.
Since the initial mandate Walmart has continued to add to its RFID initiatives with requirements for additional departments going live in early 2024 with the expectation of most general merchandise categories to require RFID tagging by 2025. It is full speed ahead with RFID for Walmart. If you are partners with Walmart, it is imperative that you understand what this mandate is, and how it will affect your organization’s operations.
For 2025, Walmart is further expanding its RFID mandate and introducing updated specifications for RFID tags in some previously mandated categories.
In this article we will cover all the key information you need to know to best prepare for Walmart’s RFID mandate.
Article Highlights
- Walmart has expanded its RFID mandate to additional product categories, including stationery, automotive, and lawn & garden, with compliance required by February 1, 2024.
- Most general Walmart merchandise categories to require RFID tagging by 2025.
- The RFID tags used must be Gen 2 UHF tags operating at 902-928 MHz and sourced from Auburn University-approved manufacturers.
- RFID implementation improves inventory accuracy to 95% and reduces out-of-stocks by up to 50%.
- Key compliance steps include selecting the right RFID technology, conducting pilot testing, and integrating new processes into daily operations.
- Suppliers must ensure data quality and maintain consistent RFID tag performance for smooth implementation.
What is RFID?
RFID, or Radio Frequency Identification, plays a pivotal role in the retail industry, revolutionizing inventory management, supply chain logistics, and customer experiences. Unlike traditional barcodes, RFID tags contain electronically stored information that can be wirelessly read and captured by RFID readers, enabling real-time tracking and monitoring of items throughout the retail ecosystem. Here are some statistics and facts about RFID usage in the retail industry:
- Enhanced Inventory Accuracy
- Reduced Out-of-Stocks
- Improved Operational Efficiency
- Omnichannel Integration RFID
- Loss Prevention
RFID technology serves as a powerful tool for loss prevention and shrinkage reduction in retail environments. By accurately tracking the movement of items, RFID helps retailers identify and mitigate instances of theft, unauthorized removal, or misplacement of merchandise.
Why RFID is a Top Technology for Retail
RFID enhances the overall shopping experience for customers by ensuring product availability, reducing wait times at checkout, and enabling personalized services such as inventory lookup, product recommendations, and self-checkout options.
Industry Adoption of RFID
The adoption of RFID technology in the retail industry continues to grow steadily. According to a report by Grand View Research, the global RFID in retail market size was valued at USD 4.3 billion in 2020 and is expected to reach USD 11.2 billion by 2028, with a compound annual growth rate (CAGR) of 13.6% from 2021 to 2028.
Overall, RFID technology has become an indispensable tool for retailers seeking to optimize their operations, improve inventory visibility, and deliver seamless shopping experiences in an increasingly competitive marketplace.
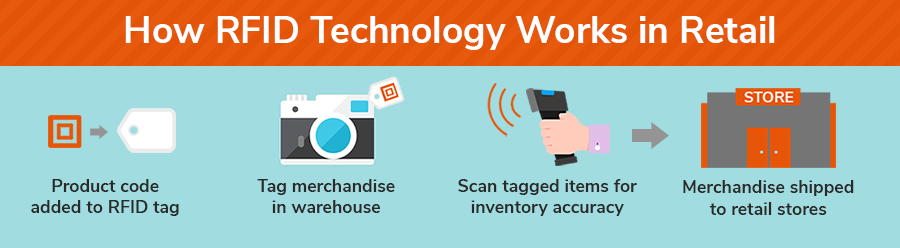
Free RFID Consultation
Have you been handed an RFID mandate? Let us help! We’ve been working with companies to help them leverage RFID implementation mandates, and identify ways they can benefit from RFID.
Key solutions include:
- Tracking and tracing inventory and goods.
- Preventing items from unauthorized usage.
- Ensuring equipment is not taken off premises.
- Check where items are stored for quick finding.
Walmart’s RFID Guidelines for Supply Chain Efficiency
Walmart’s approach to supply chain management has consistently set industry standards, with RFID (Radio Frequency Identification) technology being a key component. The company’s guidelines for RFID implementation, as outlined in their comprehensive Supply Chain Packaging Guide, are designed to enhance inventory accuracy, streamline processes, and ensure seamless integration into their extensive supply chain network.
This summary highlights the critical aspects of Walmart’s RFID guidelines, focusing on the requirements for different product categories, tag application, and compliance standards.
RFID Requirements for Product Categories
Walmart mandates the use of RFID tags across various product categories, particularly in apparel and hardline departments. All apparel items shipped to Walmart U.S. stores require RFID tags, with specific exclusions for certain eCommerce-only brands and items where RFID technology is incompatible. The categories requiring RFID tagging include a broad range of apparel, from men’s and women’s wear to accessories, as well as hardlines like toys, sporting goods, and electronics.
RFID Tag Application Guidelines
Walmart’s guidelines provide detailed instructions on how RFID tags should be applied based on packaging type. The general rule is that RFID tags must be integrated into the packaging in a way that ensures readability without compromising the product’s packaging integrity. For example, RFID inlays should be embedded in branded hangtags or applied as separate stickers depending on the packaging type. Notably, embedding RFID tags directly into the product (such as sewing them into apparel) is strictly prohibited .
The document also specifies placement restrictions to avoid interference with the tags’ functionality. For instance, RFID tags should not be placed at the bottom of poly bags or near metal objects that could disrupt signal transmission.
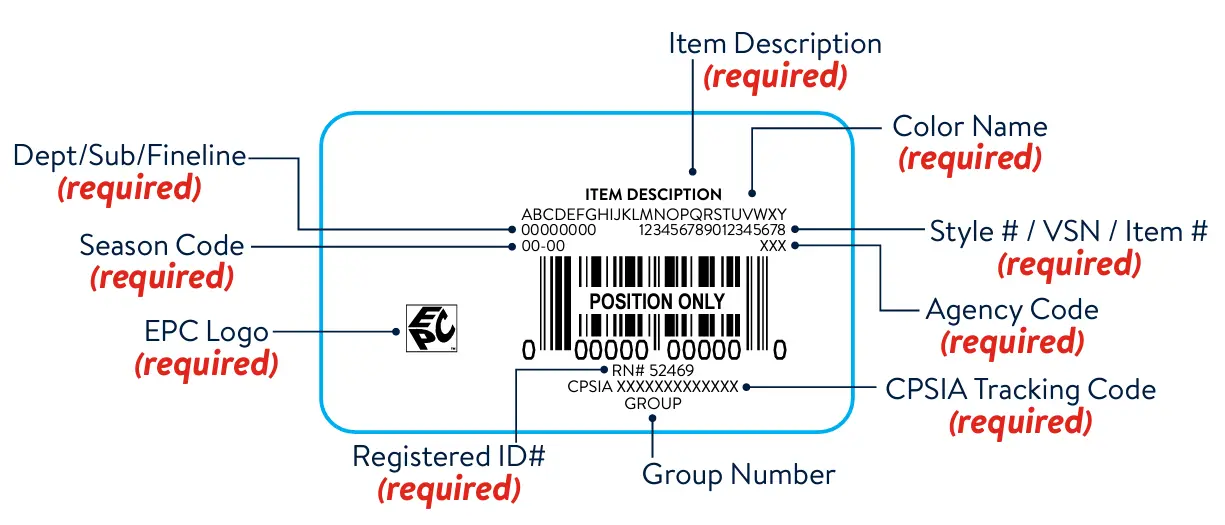
Example of an EPC combo sticker
Compliance and Quality Assurance
To ensure the quality and consistency of RFID tags, Walmart requires that all RFID inlays come from Auburn University-approved manufacturers. Even when using an approved supplier, samples must be submitted to Auburn for final approval before being deployed in the supply chain. This stringent process helps maintain the integrity of Walmart’s RFID program, ensuring that all tags are correctly encoded and free of duplication errors .
Walmart also emphasizes the importance of displaying the Electronic Product Code (EPC) symbol on all packaging containing an RFID tag. This symbol must be prominently placed where it is easily visible to both customers and store associates, ensuring that the presence of RFID is clearly communicated.
Impact on Supply Chain Efficiency
The adoption of RFID technology in Walmart’s supply chain brings numerous benefits, including enhanced inventory accuracy, faster processing times in distribution centers, and better product visibility throughout the supply chain. By following Walmart’s detailed guidelines, suppliers can ensure their products integrate seamlessly into this high-efficiency system, ultimately leading to better product availability and reduced operational costs.
In conclusion, Walmart’s RFID guidelines are a crucial part of their supply chain strategy, driving efficiency and accuracy across their operations. Suppliers who adhere to these guidelines not only meet Walmart’s requirements but also contribute to the overall effectiveness of one of the world’s largest retail supply chains.
What Are the RFID Tag Specifications?
Walmart will be requiring suppliers to use Gen 2 UF RFID tags. These kinds of tags have a frequency of 902-928 megahertz. Tag dimension requirements will vary depending on the item’s department.
According to Walmart’s Supply Chain Standards Guide:
Brand owners may select any Auburn University-approved inlay manufacturer listed on their website. Any inlay manufacturer not listed on the Auburn website cannot produce inlays for packaging being shipped to Walmart. Even if using an approved inlay provider, you must still submit samples to Auburn for final approval.
Here is how the tag specs are broken down according to Auburn University’s RFID program.
ARC Certification
All Walmart suppliers are required to secure certification for their RFID tags from the RFID Lab at Auburn University, known as the Auburn Renewal Center (ARC). Established in 2009, the ARC program verifies that RFID tags adhere to or surpass the retailer’s performance standards. The program is utilized by roughly a dozen retailers nationwide, as well as by various manufacturers and other entities.
The implementation of this RFID mandate has occurred in stages, with compliance deadlines varying according to product category. The most recent categories required to comply are additions to those already designated for inclusion in the program.
Key Dates and Deadlines
Here are a few dates to keep in mind while you and your team prepares for Walmart’s RFID compliance mandate.
- June 3rd 2022 – Deadline to submit RFID tag samples to Auburn University.
- August 17th 2022 – All RFID-tagged products must arrive to its respective distribution center or facility.
- September 2nd 2022 – All products that are going to stores must be tagged.
- February 1st 2024 – Compliance mandates expand to general merchandise categories
To learn more about Walmart’s RFID packaging expectations, download their supply chain standards document.
Walmart RFID Mandate FAQs
How Do I Implement RFID to Stay Compliant?
Implementing RFID for retail compliance involves several strategic steps to ensure the technology aligns with industry regulations and meets specific retailer requirements. First, assess your compliance needs by understanding the RFID mandates from your retail partners, such as specific tagging protocols or data requirements. Next, choose the appropriate RFID tags and technology that match the product types and operational environment of your store. Partnering with experienced RFID technology providers can offer valuable insights and solutions tailored to your specific needs. Then, integrate RFID with your existing IT infrastructure, ensuring your systems can capture and utilize RFID data effectively. Training staff on the new technology is crucial for smooth operations and compliance adherence. Conduct pilot testing to refine the system and address any issues before full-scale deployment. Finally, establish ongoing monitoring and reporting processes to maintain compliance, track performance, and continuously improve the RFID implementation. This proactive approach not only ensures compliance with retailer mandates but also leverages RFID’s benefits to enhance overall business efficiency.
What are Walmart's Minimum Requirements for RFID Packaging?
Minimum Requirements Private/Proprietary Brands:
- Barcode/UPC #
- EPC logo (place at bottom of UPC bars and scale to half of the bar height, minimum of 4.5 mm))
- Item Description (from primary packaging)
- Season code
- Dept/Sub/Fineline
- Color name
- Style number/VSN number /Item number
- Agency Code
- Registered Identification Number (RIN)
- CPSIA Tracking Code (D24/D26/D33 Only)
Minimum Requirements for National/Supplier Brands:
- Barcode/UPC #
- EPC logo (place at bottom of UPC bars and scale to half of the bar height, minimum of 4.5 mm)
- Item Description (from primary packaging)
- Additional information is allowed
Where Should You Avoid Placing RFID Tags?
For retail manufacturers, it’s crucial to strategically place RFID tags to ensure they function correctly without being obstructed or damaged. Here are several key areas where RFID tags should generally be avoided:
- Metal and Liquid: RFID tags should not be placed directly on metal surfaces or containers filled with liquid. Metal can interfere with radio waves, which can either detune the RFID antenna or reflect the signal entirely, reducing the tag’s read range. Liquids, particularly water, can absorb the radio frequency signals, rendering the tags unreadable.
- Electrical Interference: Avoid placing RFID tags near items or areas with strong electromagnetic fields, such as power generators or heavy electrical equipment. Such fields can disrupt the communication between the tag and the reader.
- Underneath Packaging Layers: Placing RFID tags underneath multiple layers of packaging material, especially metallic or dense materials, can severely limit the effectiveness of the tag. The materials may block the radio signals, making the tags difficult or impossible to read.
- Direct Product Contact: Tags should generally not be placed in positions where they will be in direct contact with the product if there is a risk of contamination or if the product could damage the tag. This is particularly important in industries dealing with food, pharmaceuticals, or delicate items.
- Extreme Corners or Edges: Tags placed on extreme corners or edges of a product or packaging might be more prone to physical damage during handling and shipping. They may also be less likely to be in the optimal position for scanning by RFID readers, especially if the alignment is inconsistent.
- Hidden or Inaccessible Areas: While it might be tempting to conceal RFID tags for aesthetic or security reasons, placing them in overly obscured or inaccessible areas can hinder their detectability. Tags should be positioned where they can be easily accessed by RFID scanners from a reasonable range.
Proper placement of RFID tags is essential for maximizing the efficiency and accuracy of the RFID system, which in turn can enhance inventory tracking, supply chain management, and overall operational productivity for retail manufacturers.
Can Apparel Manufacturers Sew RFID Inlay Tags to the Physical Apparel Item?
According to Walmart’s Supply Chain Standards Guide:
Sewing RFID inlay tags into the physical apparel item is NOT ALLOWED. Tags Sewn in that are easily removable by the customer are acceptable. RFID inlay stickers are required to be placed on packaging only.
How CYBRA’s RFID Experience Can Help
CYBRA’s expertise with RFID technology goes back nearly 20 years. We literally wrote the book on RFID integration. Rely on our experience and scar tissue to help guide your organization through your RFID installation process. Request a free consultation today!