5 RFID Statistics Manufacturers Need to Know
Bill Hardgrave, dean of Auburn University’s Harbert College of Business and founder of the RFID Lab, may say it best…
“RFID increases inventory accuracy, from an average of 65 percent to more than 95 percent. And high inventory accuracy can lead to increased sales—but only if retailers use the data to improve their operations and processes. This is an important distinction, and it’s key to the success of any RFID deployment.”
It’s important to understand that RFID is not an expense or some magical tool. It’s an investment that can cut costs out of your supply chain if implemented correctly. If you have been hesitant on implementing RFID tags into your supply chain, consider the following statistics.
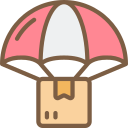
Manufacturers & distributors who implement RFID technology into their supply chain see an 80% improvement in shipping/picking accuracy.
Chargebacks can cost thousands of dollars. With the right combination of RFID hardware and software, you can verify outbound shipments at incredibly high rates. By minimizing chargebacks, RFID adoption can quickly pay for itself.
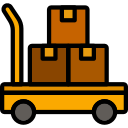
Manufacturers & distributors who implement RFID technology into their supply chain see an 90% Improvement in receiving time.
Fixed RFID readers read the tags of every single item in the carton. The system compares the ASN (Advance Ship Notice) from the factory and confirms that each carton contains exactly what was ordered. This validation is an audit of every single carton arriving from overseas and it happens in real time without any misreads and without slowing down the receiving line. For one customer whose goods are tagged at source, fixed RFID readers on inbound conveyors read the tags of every single item in the carton.
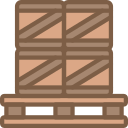
Warehouses and DC’s take their inventory visibility and availability from 2% to 20% when implementing RFID technology.
Simple item location technology fueled by RFID changes everything. Faster item retrieval and more accurate inventory are just the start. Customer satisfaction will improve with the right items being found faster, and your employees will be far more effective at inventory cycle counts and item retrieval.
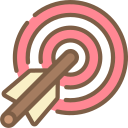
On average, companies that adopt RFID see their inventory count accuracy go from 63% to 95%.
Inaccurate inventory numbers hinders your ability to make smart purchasing decisions. For example, purchasing more of something you already have, and not on something that needs to be replenished. And, how much work is required just to get that 63% inventory accuracy? Hours of physical labor? Shutting down your warehouse for days? If you’re striving for mediocre inventory accuracy rates, you are likely paying much more than you have to.

With merchandise tagged with RFID, manufacturers can increase inventory count rates from 200 to 12,000+ items per hour.
So, what does that do for you? No more shutting down your warehouse to do inventory. No more bogging down your team when it’s time to do inventory. Now, your employees can be elsewhere doing other important things. It’s efficiency on a whole new level.