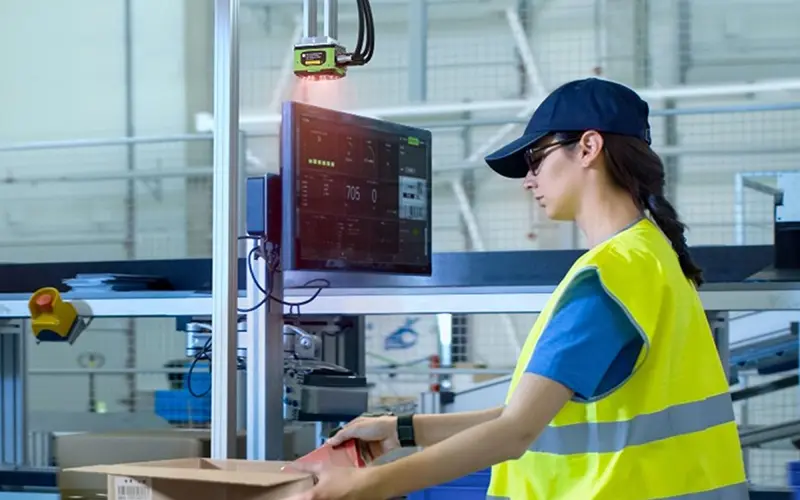
Optimizing pick and pack processes isn’t just about shaving seconds off order handling times—it’s about transforming warehouse performance from the ground up. Better pick and pack solutions lead to fewer errors, safer workflows, faster throughput, and more efficient labor utilization. In an environment where margins are tight and expectations are high, even small improvements can drive significant bottom-line results.
The numbers tell the story clearly. Labor costs make up an average of 65% of a warehouse’s operating budget (Inbound Logistics), and over half of all labor activity is tied directly to picking, packing, and shipping (Supply Chain 24/7). Even more striking, manual walking and picking can eat up more than 50% of total picking time (ConveyCo). And while traditional picking methods yield about 60–80 picks per hour, modern solutions like conveyors and sorters can push that number to 300 picks per hour (Westernacher).
In short, upgrading your pick and pack process is no longer optional—it’s essential. Below, we explore five innovative pick and pack solutions already transforming warehouses and distribution centers worldwide.
What Is Pick and Pack?
At its core, pick and pack is the process of selecting (picking) items from inventory and preparing (packing) them for shipment. While simple in theory, it becomes complex at scale, especially when dealing with high volumes, diverse SKUs, or mixed-order shipments.
Traditional methods rely on paper-based picking or basic handheld scanners, which are often slow, error-prone, and labor-intensive. However, by implementing modern pick and pack solutions, businesses can reduce fulfillment times, lower costs, and improve order accuracy—giving them a powerful edge in the logistics race.
Standard Pick and Pack Process
Receive
Check in, verify, and store goods in assigned locations.
Pick
Pull items from inventory based on order details.
Pack
Inspect, box, and label items for shipment.
Ship
Sort, hand off to carrier, and send out with tracking.
Common Pick and Pack Errors That Hurt Productivity
Before we explore advanced solutions, it’s important to understand the typical issues that slow down or compromise the pick and pack process:
- Mis-picks: Selecting the wrong SKU, size, or quantity
- Incorrect packing: Putting items in the wrong box or with incorrect labels
- Missed scans: Failing to register items due to human oversight
- Congestion and bottlenecks: Multiple workers crowding the same picking zones
- Over-reliance on manual entry: Increases chances of data errors
- Poor item location accuracy: Wastes time searching for misplaced inventory
These errors lead to delayed shipments, returns, customer dissatisfaction, and increased operational costs. The good news? Today’s pick and pack solutions are built to directly address these challenges.
5 Innovative Pick and Pack Solutions
While no two warehouses operate exactly the same, they often face similar challenges—rising labor costs, space constraints, increased order volumes, and tighter delivery windows. The right pick and pack solution addresses these challenges head-on by improving speed, accuracy, and efficiency at every step of the fulfillment process.
Each of the five solutions we’re about to explore is designed to target a specific bottleneck, whether that’s reducing walking time, minimizing human error, or speeding up order verification. Depending on your warehouse layout, SKU count, and order complexity, one or more of these methods could significantly boost your productivity and set you up for scalable growth.
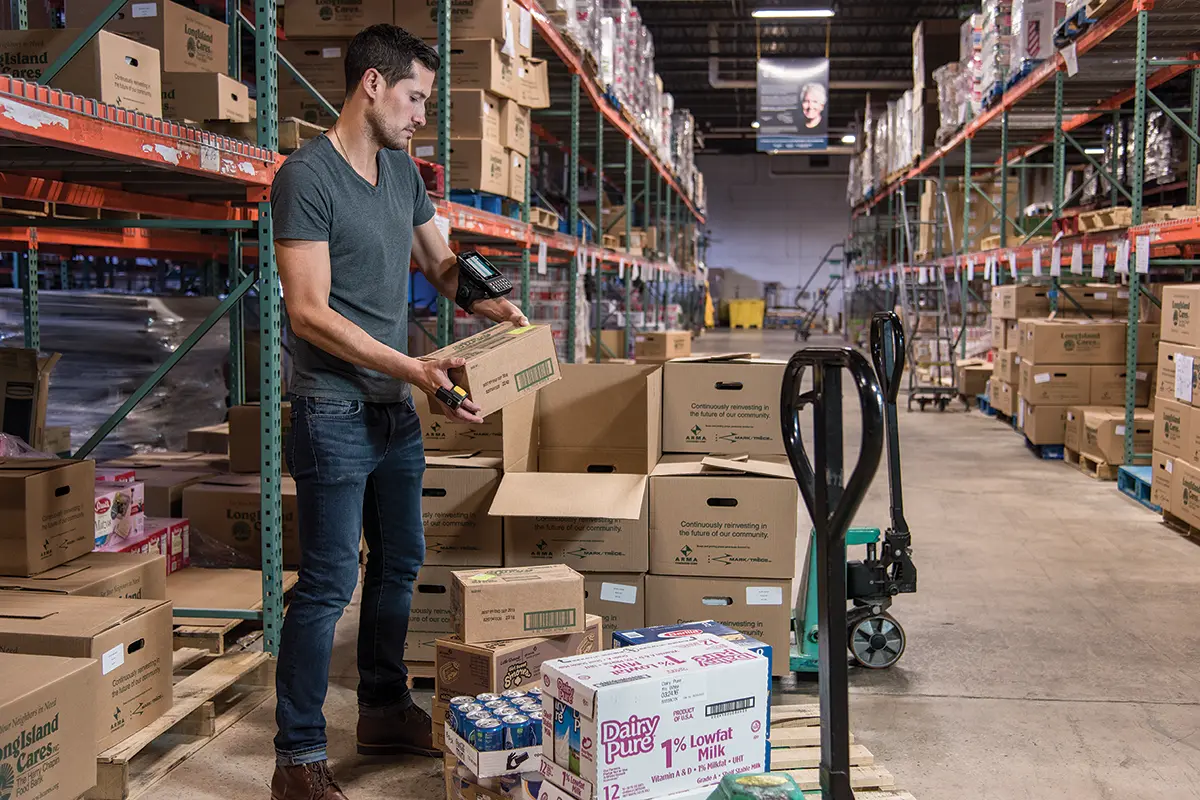
Hands Free Pick and Pack
Hands-free pick and pack systems combine wearable technology—such as ring scanners, wrist-mounted displays, and voice headsets—to enable workers to pick, scan, and pack without ever needing to hold a traditional handheld device. By freeing up both hands, employees can move faster, handle products more safely, and complete tasks with fewer interruptions.
Hands Free Pick and Pack Advantages:
- Increases pick speed by reducing the need to switch between tools
- Improves ergonomics and reduces strain from repetitive movements
- Ideal for high-volume, fast-paced environments with tight fulfillment windows
- Often integrates with voice-picking systems or smart glasses for added efficiency
Hands-free setups are especially valuable in environments where mobility and multitasking are essential—like e-commerce warehouses, cold storage, or multi-level picking zones. As wearable tech continues to improve, hands-free operations are quickly becoming a go-to choice for facilities focused on agility and output.
Voice Command Picking: Hands-Free Efficiency
Another powerful tool gaining traction is voice-directed picking. Workers wear headsets connected to a warehouse management system (WMS), which gives them verbal instructions such as aisle, bin, and quantity. Workers respond with voice confirmations, all without having to look down at a screen or hold a device.
Voice Command Pick and Pack Advantages:
- Hands-free, eyes-free operation improves speed and safety
- Greatly reduces screen-glancing errors
- Supports multi-tasking with packing or cart movement
- Useful in environments where gloves or mobility are required
Voice picking works especially well in cold storage, food distribution, or environments where workers benefit from keeping their hands free. With the rise of AI-powered voice assistants, this technology continues to improve in accuracy and adaptability.
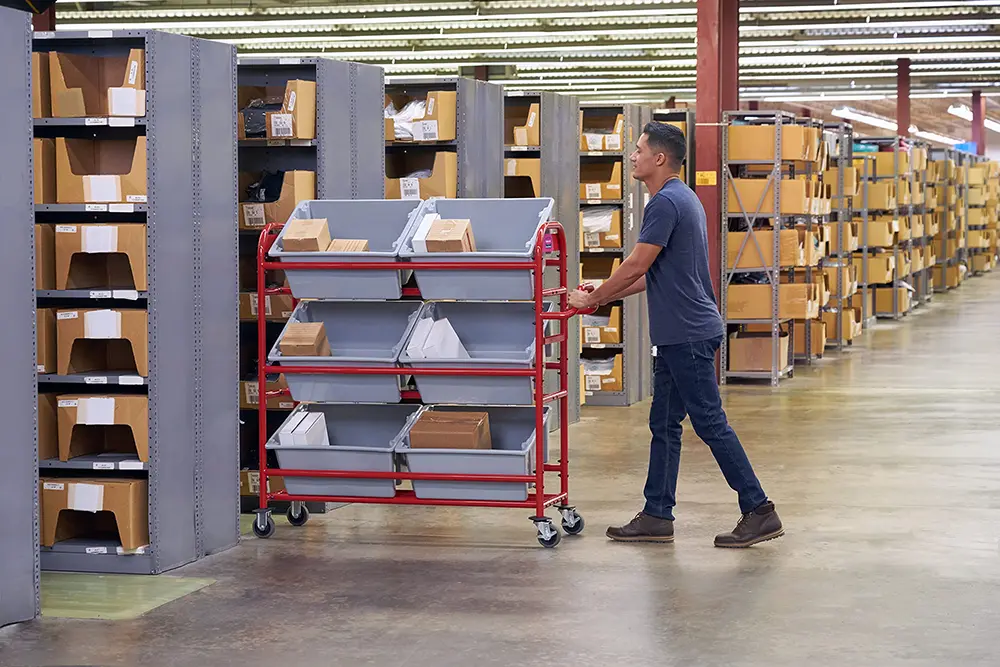
Mobile Cart Picking: Flexibility on Wheels
For facilities that handle a mix of order sizes or require zone picking, mobile cart picking offers a simple yet highly effective solution. These carts are typically equipped with tablets, barcode scanners, and sometimes even mobile printers, allowing workers to pick multiple orders simultaneously from different warehouse zones.
Mobile Carts Advantages:
- Supports batch picking and route optimization
- Reduces travel time by grouping orders efficiently
- Improves accuracy with real-time scanning and verification
- Can be upgraded with RFID or pick-to-light add-ons
By combining mobility with digital tools, mobile cart systems bridge the gap between traditional and automated picking while keeping costs manageable for mid-sized operations.
Pick-to-Light Systems: Fast and Visual
One of the most efficient solutions for high-volume operations is the Pick-to-Light system. This method uses light displays mounted on shelving or bins to visually guide workers to the correct items. When an order is initiated, lights illuminate the exact location of each product, and workers confirm the pick with the press of a button.
Pick-to-Light Advantages:
- Speeds up the picking process significantly
- Reduces search time and cognitive load
- Decreases mis-picks with visual confirmation
- Ideal for fast-moving, high-SKU environments
Because Pick-to-Light is intuitive and easy to learn, it also shortens training time for new employees. As a result, companies see quicker onboarding and smoother seasonal workforce scaling.
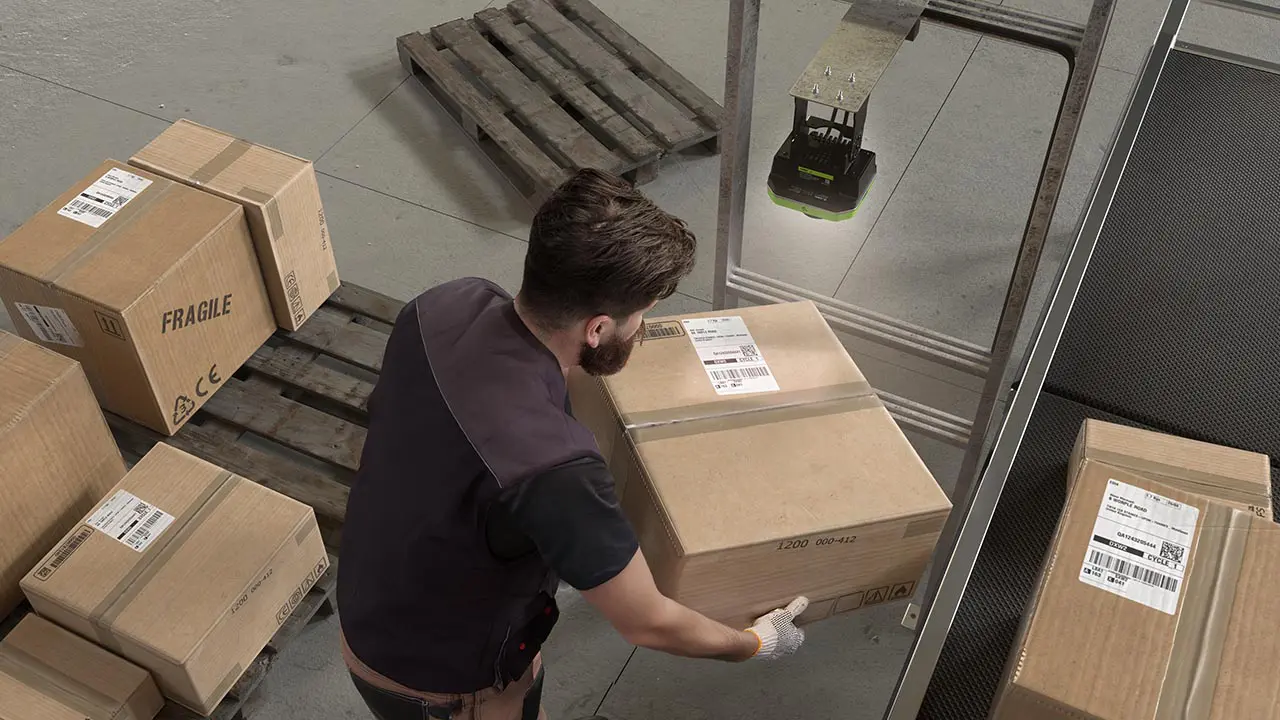
RFID in Pick and Pack: Smart, Accurate, Automated
RFID (Radio Frequency Identification) technology takes pick and pack automation to the next level. Unlike barcodes, RFID tags can be read without line-of-sight and in bulk, enabling fast scanning of multiple items at once.
RFID Pick and Pack Advatages:
- Allows batch scanning of items without manual checks
- Reduces human error in both picking and packing
- Provides real-time inventory and location tracking
- Integrates with WMS to auto-validate order accuracy
When used in packing stations, RFID can verify that every item in the box matches the order—before it’s sealed. This dramatically reduces packing errors and costly returns. As RFID becomes more affordable and scalable, more warehouses are incorporating it into their operations.
How to Choose the Right Pick and Pack Solution
With so many options available, choosing the right system depends on your specific operation size, order volume, SKU variety, and labor capacity. Here are a few guiding questions to consider:
- Are mis-picks and packing errors a current problem?
- Do workers spend too much time walking or searching?
- Are you scaling quickly and need tech that grows with you?
- Do you fulfill same-day or multi-channel orders?
- Are you investing in automation, but want to start small?
For many operations, the answer isn’t just one solution—it’s a hybrid approach. For example, you might combine mobile carts with voice picking in one zone, and Pick-to-Light in another. The goal is to create a tailored workflow that minimizes friction and maximizes throughput.
Final Thoughts: Pick and Pack Productivity Starts with the Right Tools
As order volumes grow and customer expectations rise, pick and pack operations must evolve. Modern pick and pack solutions—from light-guided picking to RFID and robotics—offer faster, more accurate, and more scalable methods for getting orders out the door.
By eliminating common errors, increasing worker efficiency, and integrating with powerful warehouse software, these solutions don’t just make warehouses faster—they make them smarter.
Whether you’re running a 5,000-square-foot eCommerce hub or a multi-facility distribution center, now is the time to assess your pick and pack strategy. Investing in the right tools today means staying competitive tomorrow—and delivering the speed and accuracy your customers demand.
Interested in RFID?
An RFID tracking system can help organizations of all sizes improve their supply chain efficiency. Contact the CYBRA team to schedule a demo today.