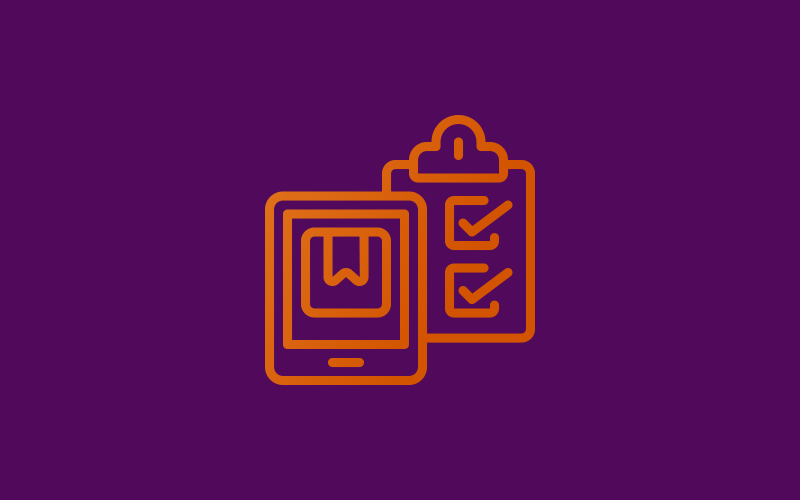
Effective inventory replenishment is critical for businesses to ensure that products are always available for customers without overstocking or running into stockouts. Inventory replenishment is the process of restocking products and materials when they are used up or sold. By adopting the right replenishment strategies, companies can maintain the delicate balance between supply and demand, minimizing costs and maximizing customer satisfaction.
3 Inventory Replenishment Strategies
In this article, we’ll explore three key inventory replenishment strategies that can improve your supply chain management. Among these strategies is the use of RFID (Radio Frequency Identification) technology, which can automate and optimize the replenishment process.
What is Inventory Replenishment?
Inventory replenishment is the process of restocking products or materials to ensure that a business maintains adequate levels of inventory to meet customer demand. It involves identifying when stock levels are low and ordering new supplies or products to prevent stockouts, which occur when items are unavailable for sale or use. Effective inventory replenishment helps businesses avoid overstocking, minimize storage costs, and keep operations running smoothly.
In essence, inventory replenishment ensures that the right quantity of goods is available at the right time, balancing the need for continuous supply without tying up excessive capital in unused stock. This process is a critical part of supply chain management and helps businesses maintain an optimal inventory flow.
Benefits
Inventory replenishment offers several key benefits to businesses, helping them maintain efficient operations and meet customer demand. Here are some of the primary advantages:
- Prevents Stockouts
- Reduces Overstocking
- Improves Cash Flow
- Enhances Supply Chain Efficiency
- Reduces Holding Costs
- Improves Forecasting and Planning
- Increases Customer Satisfaction
- Optimizes Operational Efficiency
- Supports Scalability
- Minimizes Risk of Obsolescence
1. Reorder Point Strategy
The reorder point strategy is one of the most widely used methods for inventory replenishment. This approach involves setting a predefined inventory level, known as the reorder point, which triggers a new order when the stock reaches or falls below this threshold. The reorder point is calculated based on factors such as average demand, lead time, and safety stock levels.
How It Works:
Let’s say a business sells 100 units of a product each day, and it takes 5 days for a supplier to deliver new stock. If the company wants to ensure it never runs out of stock, it should set a reorder point that covers the demand during the lead time. In this case, the reorder point would be 500 units (100 units per day x 5 days lead time). Once the stock drops to 500 units, an order is automatically placed to replenish inventory.
Benefits:
- Simplicity: The reorder point strategy is straightforward and easy to implement.
- Customization: Businesses can adjust reorder points based on demand fluctuations, seasonal trends, or supplier reliability.
Challenges:
- Accuracy: The strategy relies on accurate demand forecasting and lead time estimates. If demand suddenly spikes or the supplier delays shipments, a stockout could still occur.
- Overstocking Risk: Setting reorder points too high can lead to excessive inventory levels, increasing holding costs.
2. Just-in-Time (JIT) Replenishment
Just-in-Time (JIT) replenishment is a lean inventory strategy that aims to reduce waste and carrying costs by replenishing inventory only when it is needed, based on real-time demand. Instead of holding large quantities of stock, businesses using JIT aim to keep inventory at the lowest possible level while ensuring products are available when customers order them.
How It Works:
In a JIT system, inventory is replenished in small, frequent batches based on current sales or production needs. For example, a manufacturer using JIT might order materials only when a customer places an order for a product, rather than holding large amounts of raw materials in advance. This requires close collaboration with suppliers and highly efficient supply chain processes.
Benefits:
- Reduced Holding Costs: By minimizing inventory levels, JIT reduces the cost of storing and managing excess inventory.
- Increased Flexibility: JIT allows businesses to respond quickly to changes in customer demand, reducing the risk of overstocking and obsolescence.
Challenges:
- Supply Chain Dependence: JIT requires a highly reliable and efficient supply chain. Any disruptions, such as delays from suppliers, can lead to stockouts and lost sales.
- Risk of Stockouts: Because inventory levels are kept very low, there is little buffer in case of unexpected demand surges or supply chain disruptions.
3. RFID-Enabled Automated Replenishment
Radio Frequency Identification (RFID) technology is revolutionizing the way businesses manage their inventory replenishment. RFID uses small tags attached to products or packaging that emit signals readable by RFID scanners. This technology allows for real-time tracking of inventory levels, automating the replenishment process and reducing the need for manual counting or barcode scanning.
How RFID Works for Inventory Replenishment:
RFID tags can be placed on individual products, pallets, or storage bins. These tags contain unique identification information about the product, including its quantity, location, and status. RFID readers placed at strategic points throughout the warehouse or store continuously scan the tags, providing real-time visibility into inventory levels.
As inventory is sold or used, the system automatically updates the stock levels. When a product reaches a predetermined threshold (similar to the reorder point strategy), the system can automatically trigger a replenishment order from suppliers. This process can be integrated with an inventory management system to streamline the entire supply chain, from suppliers to warehouse to store shelves.
Benefits of RFID for Inventory Replenishment:
- Automation: RFID eliminates the need for manual counting or barcode scanning, significantly reducing labor costs and errors. Replenishment orders can be placed automatically, ensuring that stock is always at optimal levels.
- Real-Time Visibility: RFID provides continuous, real-time data on inventory levels, allowing businesses to monitor stock levels across multiple locations simultaneously. This reduces the risk of stockouts or overstocking.
- Improved Accuracy: RFID tags offer higher accuracy than traditional barcodes. Since RFID readers can scan multiple tags at once, businesses can conduct faster and more accurate stock checks.
- Enhanced Efficiency: RFID speeds up the replenishment process by providing automated alerts when stock is low and reducing the time it takes to place orders and receive new stock.
Challenges of RFID:
- Initial Investment: Implementing an RFID system requires an upfront investment in tags, readers, and software. While the long-term benefits are substantial, smaller businesses may find the initial cost prohibitive.
- Tag Costs: Although RFID tags are becoming more affordable, they are still more expensive than traditional barcodes, especially when used on individual items.
Use Case: RFID in Action
A well-known global retailer uses RFID for inventory replenishment across its stores. The company tags its products with RFID labels, which are scanned automatically as they move from warehouse to store shelves. The RFID system provides real-time stock updates, enabling the company to automatically replenish stock when it falls below a certain threshold.
This automation has led to a significant reduction in stockouts and improved customer satisfaction by ensuring that popular products are always available. Additionally, the company has been able to optimize its inventory levels, reducing the costs associated with overstocking.
Choosing the Right Strategy for Your Business
Each inventory replenishment strategy has its strengths and weaknesses, and the right approach depends on your business’s size, industry, and specific needs. Here’s a quick guide to help you decide:
- Reorder Point Strategy: Ideal for businesses with relatively stable demand patterns and predictable lead times. It’s simple to implement and effective for managing stock levels in industries like manufacturing and retail.
- Just-in-Time Replenishment: Best suited for businesses that want to minimize inventory holding costs and are confident in their supply chain’s reliability. This approach works well in industries with fast-moving products or those using a build-to-order model.
- RFID-Enabled Replenishment: Perfect for businesses that handle large volumes of inventory and want to automate the replenishment process. RFID is particularly valuable in industries like retail, healthcare, and logistics, where real-time tracking and accuracy are essential.
Conclusion
Inventory replenishment is crucial for maintaining the right balance between supply and demand. Whether you opt for the reorder point strategy, Just-in-Time replenishment, or the automation power of RFID, each strategy has unique benefits and can enhance your inventory management.
RFID, in particular, represents the future of inventory replenishment by providing real-time data, improving accuracy, and reducing labor costs. As more businesses adopt RFID technology, inventory management will become faster, more efficient, and more reliable. Choosing the right strategy for your business will depend on your specific requirements, but regardless of the approach, the goal remains the same: to keep your shelves stocked, customers satisfied, and costs under control.
Interested in RFID?
An RFID tracking system can help organizations of all sizes improve their supply chain efficiency. Contact the CYBRA team schedule a demo today.